Конструкції зубчастих коліс і технологія їх виготовлення
Конструкції зубчастих коліс і технологія їх виготовлення
Конструкції зубчастих коліс
Залежно від призначення, розмірів і технології отримання заготовки зубчасті колеса можуть мати різну конструкцію.
Циліндричні і конічні шестерні виконують заодно ціле з валом (вал-шестерня). Це пов'язано з малими розмірами шестерень і з тим, що роздільне виготовлення знижує точність і збільшує вартість виробництва внаслідок збільшення кількості посадкових поверхонь, що вимагають точної обробки, а також внаслідок необхідності застосування з'єднань (шліцьових, шпонкових), що знижують точність передачі та властивості міцності елементів механізму.
Насадні шестерні застосовують при великих діаметрах і в тих випадках, коли вони повинні переміщатися уздовж вала за умовами роботи або складання.
При діаметрі dа ≤ 150 мм колеса виготовляють у формі суцільних дисків з прокату або з поковок (рис. 1).
Зубчасті колеса діаметром менше 500 мм отримують ковкою (рис. 2). відливанням (рис. 3, а) або зварюванням (рис. 3, б).
Колеса діаметром понад 500 мм виконують відливанням або зварюванням.
Іноді зубчасті колеса виконують у вигляді вузлів, утворених складанням окремих частин (рис. 4). Так, вінці коліс можуть бути напресовані на маточину (бандажірованного колеса) (рис. 4, а), кріпитися різьбових з'єднань (з'єднувальні колеса) (рис. 4, б) або приклепують (клепані колеса) (рис. 4, в).
Бандажірованного, з'єднувальні або клепані колеса застосовують в цілях економії легованих сталей або кольорових металів, якщо такі використовуються при виготовленні колеса.
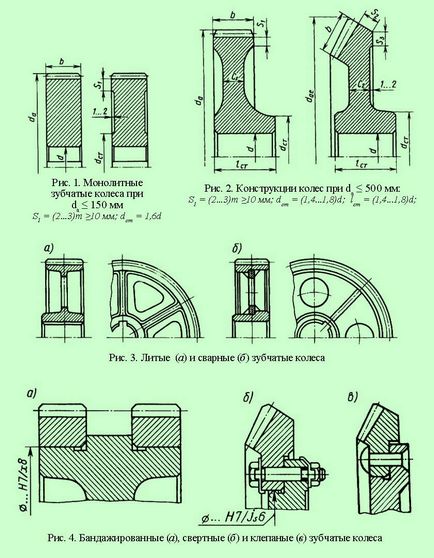
Виготовлення зубчастих коліс
Заготовки зубчастих коліс отримують куванням в штампах або вільним куванням, рідше литтям в залежності від розмірів, матеріалу, форми і масштабу випуску. Зуби евольвентних коліс виготовляють так, щоб кожне колесо могло входити в зачеплення з колесами того ж модуля, що мають будь-яке число зубів.
Зуби отримують нарізуванням або накочуванням.
Метод копіювання полягає в прорізуванні западин між зубами модульними фрезами (рис. 5): дисковими (а) або кінцевими (б). Після прорізання кожної западини заготовку повертають на крок зачеплення. Профіль западини є копією профілю різальних крайок фрези, звідси і назва - метод копіювання.
Точність нарізаються зубів невисока, метод є малопродуктивним, тому його застосовують, переважно, в ремонтному виробництві.
Метод обкатки має основне застосування. Нарізування зубів за цим методом грунтується на відтворенні зачеплення зубчастої пари, одним з елементів якої є ріжучий інструмент - черв'ячна фреза (рис. 6, а), долбяк (рис. 6, б) або рейковий долбяк - гребінка (рис. 8.).
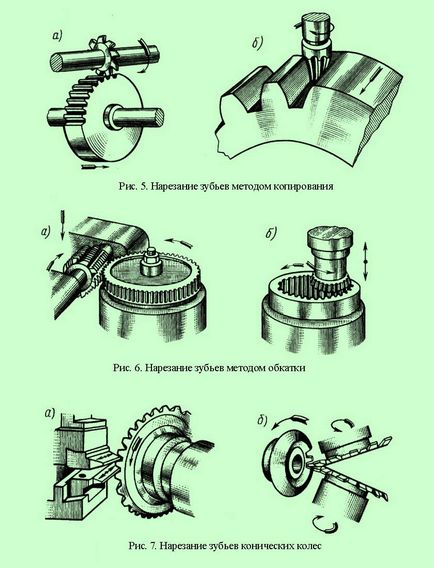
Черв'ячна фреза має в осьовому перерізі форму інструментальної рейки. При нарізанні зубів заготовка і фреза обертаються навколо своїх осей, забезпечуючи безперервність процесу.
Нарізування зубів черв'ячними фрезами широко застосовують для виготовлення коліс з зовнішнім розташуванням зубів.
Для нарізування коліс з внутрішнім розташуванням зубів застосовують долбяки.
Гребінками (див. Рис. 8) нарізають прямозубі і косозубиє колеса з великим модулем зачеплення.
Нарізування зубів конічних коліс методом обкатки проводять струганням (рис. 7, а), фрезеруванням (рис. 7, б), різцьовим головками.
Накочення зубів застосовують в масовому виробництві. Попереднє формоутворення зубів циліндричних і конічних коліс виробляють гарячим накочуванням. Вінець сталевої заготовки нагрівають струмами високої частоти (ТВЧ) до 1200 ˚С. а потім обкатують між колесами-накатнику. При цьому на вінці видавлюються зуби. Для отримання коліс більш високої точності виробляють подальшу механічну обробку зубів або холодне накочення - калібрування. Холодне накочування зубів застосовують при модулі до 1 мм.
Накочення зубів - високопродуктивний метод виготовлення коліс з мінімальним відходом металу в стружку.
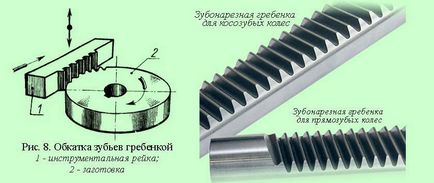
Оздоблення (доведення) зубів
Зуби коліс точних зубчастих передач після нарізування піддають обробці Шевінгування, шліфуванням, притиранням або обкаткою.
Шевінгування застосовують для тонкої обробки незагартованих зубів.
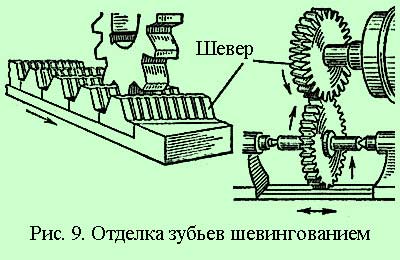
Шліфування застосовують для обробки загартованих зубів. Виконують шліфувальними кругами способом копіювання або обкатки.
Притирання використовують для обробки загартованих зубів коліс. Виконують притиром - чавунним точно виготовленим колесом з використанням притиральних паст.
Обкатку застосовують для згладжування шорсткостей на робочих поверхнях зубів незагартована коліс. Протягом 1 ... 2 хвилин зубчасте колесо обкатують під навантаженням з еталонним колесом високої твердості.
Ковзання при взаємодії зубів
При роботі коліс зачеплення двох зубів відбувається по робочих ділянках профілів, при цьому робочі ділянки профілів одночасно перекочуються і ковзають один по одному. Ковзання викликано тим, що за один і той же проміжок часу контактують ділянки головок більшої довжини з відповідними їм ділянками ніжок зубів меншої довжини. Швидкість ковзання зубів в крайніх точках зачеплення має максимальне значення, і дорівнює нулю в полюсі зачеплення, при цьому при переході точки зачеплення через полюс швидкість ковзання змінює знак (рис. 10).
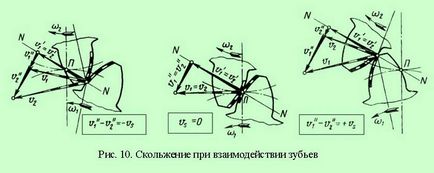
Точки профілів головок зубців мають бόльшіе дотичні швидкості, ніж точки ніжок, отже, поверхні головок є випереджаючими. Бόльшему зношування схильна ніжка, меншому - головка, що призводить до спотворення профілю зуба, особливо у відкритих передачах.
Нерівномірний ковзання зубів є недоліком евольвентного зачеплення. Малі значення швидкості ковзання в околополюсной зоні збільшують коефіцієнт тертя в цій зоні, що створює передумови для викришування робочих поверхонь зубів в результаті контактних напружень.
Вплив числа зубів на форму і міцність зуба
Зміна числа зубів призводить до зміни форми зуба. У рейки з числом зубів z прагнуть до нескінченності зуб прямобочного (рис. 11, а); зі зменшенням кількості зубів збільшується кривизна евольвентного профілю, а товщина зуба біля основи і вершини зменшується.
При зменшенні кількості зубів нижче граничного з'являється підріз ніжки зуба ріжучої кромкою інструмента (рис. 11, в), в результаті чого міцність зуба різко знижується. Через зрізу частини евольвенти у ніжки зуба (рис. 12) зменшується довжина робочої ділянки профілю, в результаті чого знижується коефіцієнт перекриття εα і зростає зношування.
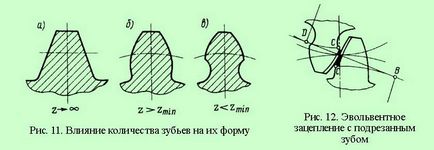
Щоб виключити підрізання ніжки зуба при малому z інструментальної рейки необхідно повідомити зміщення xm (рис. 13, а), при якому вершина її зуба вийде із зачеплення з зубом колеса 2 в точці S і евольвента профілю вийде повною, що не підрізаній (рис. 13, б). При цьому надмірна частина рейки НЕ буде підрізати зуб.
Величину xm називають абсолютним зсувом рейки, величину x - відносним зсувом рейки, або коефіцієнтом зсуву.
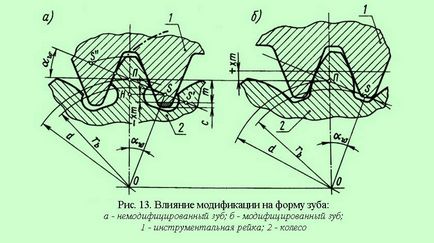
Мінімальна кількість зубів шестерні, у якій виключено підрізання зубів без зміщення рейки (т. Е. При x = 0) можна визначити за формулою:
При αw = 20 ˚ мінімальна кількість зубів zmin = 17.
Зі збільшенням кількості зубів зростає коефіцієнт перекриття εα. підвищується плавність роботи передачі, зменшуються втрати на тертя і вартість виготовлення коліс. Оптимальна кількість зубів коліс, використовуваних в зубчастих передачах і редукторах, приймають рівним zmin = 18 ... 35.
Зубчасті передачі зі зміщенням
Передачу зі зміщенням утворюють зубчасті колеса, у яких нарізування зубів здійснюють зі зміщенням рейки на величину xm (рис. 13). Зміна форми зуба в порівнянні з вихідним зачепленням при нарізанні зі зміщенням називають модифікацією профілю.
Модифікований профіль зуба окреслюється іншим (зміщеним) ділянкою тієї ж евольвенти, що і профіль немодифицированного зуба.
Модифікацію застосовують:
- для усунення підрізання зубів шестерні при малій кількості зубів;
- для підвищення згинальної міцності зубів, що досягається збільшенням їх товщини;
- для підвищення контактної міцності, що досягається збільшенням радіуса кривизни в полюсі зачеплення;
- для отримання заданого міжосьової відстані передачі.
Позитивним називають зміщення рейки від центру зубчастого колеса, негативним - до центру.
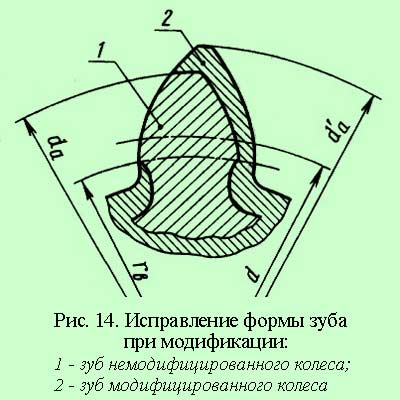
При негативному зміщенні має місце зворотне явище.
У зубчастих коліс зі зміщенням товщина зуба і ширина западини по ділильної окружності неоднакові, але в сумі залишаються рівними кроці р.
Залежно від поєднання зсувів при нарізанні зубів парних зубчастих коліс модифікація буває висотної і кутовий.
висотна модифікація
При висотної модифікації шестерню виготовляють з позитивним коефіцієнтом зсуву, а колесо - з негативним, при цьому абсолютні величини зсувів повинні бути рівні, в результаті чого сумарний коефіцієнт зміщення буде дорівнює нулю. Такі передачі називають равносмещеннимі.
При висотної модифікації зубчастої пари діаметри ділильних кіл шестерні і колеса збігаються, як і в передачі без зміщення, отже, міжосьова відстань, коефіцієнт перекриття і кут зачеплення залишаються незмінними. Загальна висота зубів також не змінюється в порівнянні з її нормальним значенням, але змінюється співвідношення між висотою головок і ніжок зубів. Тому така модифікація і називається висотної.
Висотну модифікацію застосовують при малому числі зубів шестерні і великому передавальному числі, коли потрібно забезпечити такі форми зубів шестерні і колеса, при яких вони будуть приблизно равнопрочность на вигин.
кутова модифікація
Кутова модифікація є загальним випадком модифікування, при якому сумарний коефіцієнт зміщення пари коліс не дорівнює нулю, т. Е. Зсув у шестерні і у колеса неоднакові по абсолютній величині.
Кутова модифікація в порівнянні з висотної дає значно бόльшіе можливості впливати на різні параметри зачеплення (міжосьова відстань, кут зачеплення, кут перекриття і т. П.), Тому вона застосовується частіше.
Модифіковані зубчасті колеса виготовляють тим же стандартним інструментом і на тому ж обладнанні, що і немодифіковані. Для отримання нормальної висоти зуба діаметри заготовок відповідно збільшують або зменшують на величину подвоєного зміщення інструменту.
Іноді модифіковані колеса називають коригувати (застаріла термінологія).
Точність зубчастих передач
При виготовленні зубчастих передач неминучі похибки, які виражаються в радіальному битті зубчастого вінця, відхиленнях кроку, профілю зуба, співвісності осей коліс, коливанні міжосьової відстані та ін.
Ці похибки призводять до підвищеного шуму під час роботи передачі, втрати точності обертання веденого колеса, порушення правильності і плавності зачеплення, підвищення динамічності і зниження рівномірності розподілу діючої в зачепленні навантаження по довжині контактних ліній і, в кінцевому рахунку, визначають ресурс і працездатність передачі.
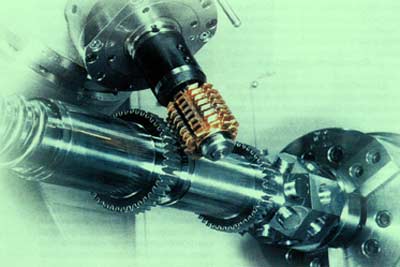
Проте, виконувати зубчасті передачі з дуже високою точністю не завжди доцільно, оскільки це призводить до подорожчання механізму в цілому. Тому стандартом регламентується точність зубчастих коліс і передач в залежності від їх призначення і умов роботи.
Допуски на цилиндрически зубчасті передачі визначаються стандартом ГОСТ 1643-81.
Цим стандартом встановлено 12 ступенів точності зубчастих коліс і передач: 1, 2, 3 ... 12 в порядку убування точності. Для ступенів точності 1 і 2 і 12 допуски стандартом не передбачені (для перспективи).
Найбільшого поширення мають 6,7, 8 і 9-я ступеня точності: 6-я ступінь відповідає високоточним швидкісним передачам, 7-я - передачам нормальної точності, які працюють з підвищеними швидкостями і помірними навантаженнями або з помірними швидкостями і підвищеними навантаженнями, 8-а передачам загального машинобудування зниженою точності, 9-я - тихохідним передачам машин низької точності.
Для кожного ступеня точності встановлені незалежні норми допустимих відхилень параметрів, що визначають:
- кінематичну точність коліс і передачі (регламентує похибка кутів повороту зачіпляються пар коліс за один оборот);
- плавність роботи (регламентує коливання швидкості за один оборот колеса, що викликають шум і динамічні навантаження);
- контакт зубів зубчастих коліс у передачі (регламентує концентрацію навантаження на зубах, визначальну працездатність силових передач).
Також ГОСТ 1643-81 встановлює шість видів сполучень визначальних гарантований бічний зазор між неконтактірующімі поверхнями суміжних зубів.
Бічний зазор необхідний для запобігання заклинювання зубів передачі від нагрівання, розміщення мастильного матеріалу і забезпечення вільного обертання коліс.
Розмір зазору задають видом сполучення зубчастих коліс у передачі: Н - нульовий зазор, Е -малий зазор, D і С - зменшені зазори, В - нормальний зазор, А - збільшений зазор.
У загальному машинобудуванні найчастіше застосовують вид сполучення В. а для реверсивних передач - С.
Отримання бічних зазорів пов'язано з точністю виготовлення коліс.