Вічне »свердло
Засвердлюванням називається операція виготовлення круглих отворів в суцільному матеріалі оброблюваної деталі за допомогою ріжучого інструменту, званого свердлом.
Збільшення діаметра вже наявного в деталі отвори за допомогою свердла називається розсвердлюванням, а виконання в суцільному матеріалі неглибоких (некрізних) отворів називається Засвердлювання.
За конструкцією і характером виконуваної роботи свердла поділяються на такі групи: перові, спіральні, центрові, кільцеві (рис. 1).
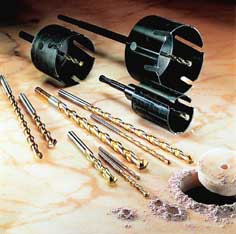
Виготовляються свердла з інструментальних вуглецевих, легованих або швидкорізальної сталей. У кожній групі свердла можуть оснащуватися твердосплавними пластинами.
перові свердла
Перові або плоскі свердла відрізняються простотою конструкції, дешеві у виготовленні, можуть бути виготовлені самостійно, мало чутливі до перекосу в роботі. Перові свердла бувають двосторонні й односторонні; відмінність їх лише у формі заточування різальних крайок (рис. 2).
Мал. 2. Перове свердло: а) для дерева; б) для пластмаси
Перові свердла мають пласку ріжучу частину з двома ріжучими крайками, розташованими симетрично щодо осі свердла і утворюють кут різання в 45 °, 50 °, 75 °, 90 °.
Діаметр свердла вимірюється по ширині лопатки. Товщина пера у ріжучих ребер залежить від діаметра свердла і становить:
- у свердел діаметром 5. 10 мм від 1,5 до 2 мм;
- діаметром 10. 20 мм від 2 до 4 мм;
- діаметром понад 20 мм від 6 до 8 мм.
Ріжучі ребра при своєму перетині утворюють пряму лінію, яка називається поперечної кромкою. або перемичкою.
Недолік пір'яних свердел полягає у відсутності автоматичного відведення стружки під час свердління, що псує ріжучі кромки і змушує часто виймати свердло з просвердлюваного отвори. Крім того, перові свердла в процесі роботи втрачають напрямок і зменшуються в розмірах діаметра при переточуванні.
спіральні свердла
Мал. 3. Спіральні свердла
Спіральні свердла мають найширше застосування. Спіральні свердла (рис. 3) являє собою циліндричний стрижень, робоча частина якого забезпечена двома гвинтовими спіральними канавками, призначеними для відводу стружки і освіти ріжучих елементів. Нахил канавок до осі свердла становить 10. 45 ° (рис. 4).
Мал. 4. Нахил канавок до осі свердла
Робочий кінець свердла має конусоподібну форму. На утворюють цього конуса лежать дві, симетрично розташовані відносно осі свердла ріжучі кромки.
Хвостовик призначається для закріплення свердла.
Спіральні свердла виготовляють з циліндричним, конічним шестигранним. хвостовиками (рис. 5). Свердла з циліндричним хвостовиком виготовляють діаметром до 12 мм, з конічним - від 6 до 60 мм.
Мал. 5. Хвостовики свердел
Лапка - кінцева частина свердла (2) - служить упором при вибиванні свердла (1) з гнізда конуса (3) за допомогою клина (4).
Спіральні свердла стандартизовані. Тому вибирають тільки такі розміри отворів, для яких є відповідний діаметр свердла. Основним розміром свердла прийнято вважати діаметр.
Довжина робочої частини свердла, в залежності від діаметру, становить: у свердлах з циліндричним хвостовиком діаметрів плюс 50 мм, а з конічним - 2 діаметра плюс 120 мм.
Кут а при вершині свердла (кут між ріжучими крайками) вибирається в залежності від оброблюваного матеріалу і становить:
для свердління м'яких металів
Допустима швидкість різання під час свердління залежить:
Від якості матеріалу свердла. Свердла зі швидкорізальної сталі допускають більш високі швидкості різання, ніж свердла з вуглецевої сталі.
Від механічних властивостей оброблюваного матеріалу. Чим пластичнее матеріал, тим важче відводиться стружка, швидше нагрівається свердло і знижуються його ріжучі властивості. Тому крихкі матеріали можна свердлити з більш високою швидкістю, ніж в'язкі.
Від діаметра свердла. Зі збільшенням діаметра швидкість різання можна підвищити, так як масивне свердло має більшу міцність і краще відводить тепло від різальних крайок.
Від глибини свердління. Чим глибше просвердлений отвір, тим важче відведення стружки, більше тертя і вище нагрів ріжучих крайок. Тому за інших рівних умов свердління неглибоких отворів можна виробляти з більшою швидкістю, а глибоких - з меншою.
Від величини подачі свердла. Чим більше подача, тобто чим товще перетин стружки, тим швидкість різання менше.
Від інтенсивності охолодження свердла. Свердло працює краще при більшій швидкості різання і малої подачі. Якщо під час роботи свердло швидко затупляется в кутах ріжучої кромки (на початку циліндричної частини свердла), це вказує на те, що швидкість різання взята занадто великий і її треба зменшити. Якщо ж свердло затупляется або фарбували по ріжучих крайок, це вказує на те, що подача занадто велика. Затуплення і поломка свердла найчастіше відбуваються в кінці свердління наскрізних отворів (при виході з металу).
Щоб попередити затуплення або поломку свердла на проході, треба в кінці свердління зменшити подачу.
Охолодження і змащування свердла. Несприятливі умови відводу теплоти при свердлінні викликають необхідність охолодження свердла. При свердлінні в'язких матеріалів охолодження повинно бути особливо рясним.
Для охолодження свердла в роботі застосовують:
- при свердлінні твердих матеріалів - гас, скипидар, емульсію;
- під час свердління м'яких матеріалів - содовий розчин;
- при свердлінні сірого чавуну - гас, струмінь стисненого повітря.
Застосуванням охолодження під час свердління можна підвищити швидкість різання для стали на 10%, а для чавуну до 40% і отримати більш чисту поверхню отвори.
Вибір діаметра свердла
У практиці, в залежності від призначення, зустрічаються різні види свердління отворів, наприклад наскрізні (на прохід) глухі, під розгортку, під різьбу і т.п.
У всіх цих випадках для одного і того ж номінального діаметра отвору вибирають свердла різних діаметрів.
Слід мати на увазі, що в процесі свердління свердло розробляє отвір і робить його трохи більшого діаметра. Середніми величинами розробки отвори свердлом (різницю між діаметром отриманого отвору і діаметром свердла) можна приймати такі:
Діаметр свердла, мм
Розробка отвори, мм
Для отримання отворів з точним діаметром слід враховувати величину розробки і відповідно підбирати свердло трохи меншого діаметру.
Існують два способи свердління: по розмітці і по кондуктору.
Свердління по розмітці застосовується у всіх ремонтних роботах, а також в дрібносерійному і індивідуальному виробництвах.
Свердління по кондуктору проводиться без попередньої розмітки і застосовується в тих випадках, коли потрібно просвердлити велика кількість однакових деталей.
Перевірка правильності свердління
Призначене до свердління отвір повинен бути попередньо розмічено і накерніть як по колу, так і по центру отвору.
Перед початком свердління необхідно міцно закріпити свердло в патроні і жорстко закріпити оброблюваний виріб у відповідних пристроях. Оброблюваний виріб закріплюють так, щоб центр отвору (поглиблення від кернера) і вершина свердла точно збігалися. Для перевірки правильності установки вироби засверливают отвір на глибину діаметра свердла, а потім оглядають отриману окружність; якщо вона збігається з накерненной при розмітці окружністю, це означає, що установка свердла проведена правильно і свердління можна продовжувати.
При розбіжності окружності роблять відповідне виправлення.
Мал. 9. Крейцмейселі
Для цього крейцмейселем (рис. 9) з напівкруглим лезом прорубують канавку з того боку, куди треба змістити центр свердла, накернівают, виправляють установку деталі, домагаючись повного збігу засверленним отвори з розміченій окружністю.
Причина поломки свердла
Практикою встановлено такі основні причини поломки свердел:
1) зустрічаючи на своєму шляху раковину, свердло сильно відхиляється в сторону і ламається;
2) якщо нижня частина отвору у виробі обмежена не горизонтальної, а похилою площиною, свердло виходить з виробу нерівномірно, застряє в отворі й ламається;
3) під час свердління глибоких отворів, коли глибина свердління більше ріжучої частини свердла, канавки, занурюючись в вироби, закупорюються стружкою, при цьому свердло сильно нагрівається, притупляється і ламається;
4) під час виходу свердла з вироби, тобто в кінці свердління, якщо подача не зменшилася, а залишилася колишньою, свердло часто ламається;
5) поломка також відбувається при роботі тупим свердлом.
зенкування
Мал. 10. Зенковка
Зенкування - це обробка вихідної частини отвору з метою зняття задирок і освіти поглиблень під потайні головки гвинтів, болтів і шурупів. Інструмент, застосовуваний для цієї мети, називається зенковкой (рис. 10). Зенковки за формою ріжучої частини поділяються на конічні і циліндричні.
Конічні зенковки з кутом при вершині в 30, 60, 90 і 120 ° служать для зняття задирок в вихідний частини отвори і для отримання конічного поглиблення в отворах під опори конічних головок гвинтів і заклепок.
Циліндричні зенковки з торцевими зубами служать для розширення вихідний частини циліндричних отворів під плоскі шайби, головки гвинтів, а також для підрізання уступів і бобишек.
Спосіб роботи зенковки такий же, що і під час свердління отворів свердлом, тобто хвостовик закріплюється в патроні і інструменту повідомляється обертальний і поступальний рух.
Макієнко Н.І. Загальний курс слюсарної справи. - М. Вища. шк. 1989.