Реферат виникнення доменної печі - банк рефератів, творів, доповідей, курсових і дипломних
Перші доменні печі з'явилися в Європі в середині 14 століття.
ВУкаіни до 30-х рр. 17 в. єдиним відомим на території країни способом отримання заліза з руд був одностадійний спосіб, заснований на прямому відновленні металу з оксидів і здійснювався в печі, що отримала назву сиродутного (ручного) горна, що називався також Домна (домницю).
Спочатку термін "Домниця" означав "кузню", тобто приміщення, де встановлювалися сиродутние горна для отримання заліза. Однак зараз під цим словом розуміють плавильний горн, прототип сучасної доменної печі. Домниці XVI-XVII століть працювали зовсім інакше, ніж доменні печі. Вони представляли собою шахтні печі висотою близько 1 м з круглим перетином діаметром 500-600 мм, які будувалися зазвичай за два-три дні. Продуктивність такого горна була до 0,1 т на добу.
В ході процесу виходив губчастий кому зварювального заліза (точніше - низкоуглеродистого залізного сплаву), змішаного зі шлаками - залізна криця. Таке залізо називали сирим. Для перетворення його в ділове крицю проковували в особливій железцовой кузні.
Поява вУкаіни перших домен не знищило металургії, заснованої на одностадійному способі - домни і домни тривалий час співіснували.
Наступна спроба будівництва доменного заводу була зроблена через 62 роки. Нова спроба будівництва вУкаіни вододействующіе доменної мануфактури виявилася більш вдалою, ніж попередня.
Більшість перерахованих заводів будувалися іноземними купцями ( "гостями"). Важлива роль останніх у створенні російської доменної мануфактури була обумовлена низкою об'єктивних причин:
- іноземні купці краще українських були знайомі з технікою, економікою і організацією виробництва, заснованого на використанні невідомих вУкаіни технологій;
- їм легше було підібрати в Європі майстрів, готових виїхати для роботи в Україні;
вони (принаймні, деякі) володіли засобами, достатніми для реалізації навіть такого дорогого проекту, як будівництво мануфактури.
Серед іноземних комерсантів, пов'язаних зі становленням української доменної металургії, відзначимо А. Вініуса, Ф. Акему, В. Меллера (всі - уродженці Нідерландів), а також відбувалися з Гамбурга Бутенанта і представників декількох поколінь роду Марселіс. У XVII столітті вони засновують понад два десятки залізних заводів під Москвою, Тулою, в Олонецком, Вологодському і інших краях.
Людини, завдяки знанням, наполегливості і підприємливості якого перший завод був побудований і пущений, людини, що стала батьком російської доменної металургії, звали Андрієм Денисовичем Вініусом.
Доменні заводи були вододействующіе, спорудження їх ставало можливим тільки при наявності річок, які задовольняли певним, досить жорстким вимогам, а саме, що володіли водотоком, досить потужним для забезпечення потреби в гідроенергії, і досить керованим для безпечної експлуатації водяних двигунів і пов'язаних з ними механізмів. Важливу роль грав і рельєф місцевості: будівництво заводів на рівнинних ділянках вимагало для пристрою ставків-накопичувачів споруди довгих гребельних насипів і відчуження земельних угідь великої площі.
У 1636 р заводи дали першу продукцію: 100 пудів прутового і 43,5 пуда дощатої заліза (1,64 і 0,71 т відповідно). Не виключено, правда, що це було залізо, отримане в сиродутних горнах. Але не пізніше наступного, 1637 року на заводах виплавили і перший вУкаіни доменний чавун. Тоді ж вперше вУкаіни він був використаний в якості ливарного сплаву, тоді ж в ході кричного переділу перероблений в залізо.
У початковий період своєї історії (до 1648 р) металургійний комплекс на Туліца включав не менше трьох заводів, два з яких були доменними, один (нижній) - переробні. Обслуговували їх іноземні майстри, які приїхали за договором з заводчиком з різних країн в Україну з сім'ями на певний термін. Згадаємо з їх числа двох: "плавильного справи майстра Нємчина" селян (Християна) Вільде, який працював на заводі в 1647 році - його ім'я відкриває на сьогоднішній день список імен доменних майстрів з Європи, які працювали на металургійних заводахУкаіни, і пов'язаного з обслуговуванням доменної плавки ( відав складанням шихти і завантаженням її в піч) майстра Юрія Ведена. Кожен з них обслуговував по дві печі.
Основною продукцією заводів в перше десятиліття їх існування були чавун, залізо і вироби з них. Чавун, призначений для переділу, відливали в чушки, що називалися свинями або багнетами, інший - відразу використовували в якості ливарного матеріалу. Значну частку в обсязі виробництва займали гармати і ядра до них.
На рубежі 18 ст. починається промислове освоєння Уралу - нового, багатого ресурсами, величезного за площею гірничо-металургійного району, незабаром став головним металургійним центром країни.
Перші уральські залізоробні заводи, що виникли ще в XVII столітті, не мали доменних печей і представляли собою просту кооперацію - об'єднання окремих плавильних горнів, які мало чим відрізнялися від звичайних селянських домниц. Ще на початку XVIII століття плавка руди в малих домницях була поширена в багатьох районах Уралу: поблизу Кунгура, Невьянска, Нижнього Тагілу, Далматовского монастиря, Алапаївського заводу і в інших місцях. Селяни-промисловці виробляли крічное і смуговий залізо і уклад. «З криці в расковочних кузнях виробляли напівфабрикат - коване залізо, очищене від шлаку, окалини і сміття, яке представляло собою смуги, прути і ін. І називалося" укладом ". З 1,6 кг кричного заліза виходило 1,1 укладу, з якого потім виготовляли вироби ».1
Спочатку висота домен коливалася від 10 до 20 аршин (аршин - російська міра довжини, рівна 0,71 м.), 4,5 аршини в розпаді, добова виплавка коливалася від 400 до 570 пудів. Однак добова виплавка чавуну визначався не стільки розмірами домен, скільки обмеженими резервами водяній енергії, яку застосовували для подачі дуття. Тому для посилення дуття на заводі використовували чавунні циліндричні міхи більш високу ефективність, якими замінено дерев'яні клинчасті. Кожна піч мала чотирма чавунними циліндричними хутром.
Найважливіший компонент металургійної шихти - вугілля. До 30-х рр. 18 в. коли в Англії почався переклад доменної плавки на мінеральне паливо, повсюдно застосовувався єдиний його вид - деревне вугілля, який отримували безпосередньо в лісі купчастим углежжением - "Кабан" способом.
Застосування циліндричних повітродувних машин, винайдених в Англії в 1760 році, було найбільш суттєвим нововведенням в російській металургії кінця ХVIII століття. Про його значення можна судити вже по тому, що заміна шкіряних міхів навіть такими недосконалими дерев'яними циліндричними машинами давала до 20% економії вугілля. Разом з тим, прискорюючи металургійні процеси, нові повітродувки різко підвищували добову виплавку, а отже, і продуктивність праці доменного персоналу.
Починаючи з 1863 р виплавка чавуну стала підвищуватися. У цей період з'являється парова машина як підсобна в зимовий час для дії доменної повітродувки. Одно-фурмені домни перероблені на двуфурменние. Встановлено регенератор Сіменса.
Пристрій сучасної доменної печі
Для роботи доменної печі необхідні великі кількості руди, палива (кам'яного вугілля), вапняку і води (для охолодження). Руду підривають, витягають, дроблять і перетворюють у дрібний порошок. При випалюванні утворюється оксид заліза, що виявляє магнітні властивості, завдяки чому з водної суспензії його відокремлюють від пустої породи магнітною сепарацією. Магнітний оксид брикетують обкаткою в барабані, потім злегка спекают до отримання окатишів, придатних для доменного процесу. Таким способом з бідної руди (
20% оксиду заліза) отримують майже чистий Fe3O4, який спільно з вапняком і коксом використовується для виплавки чавуну в доменній печі.
При досить високій температурі оксид заліза реагує з моноксидом вуглецю (CO), даючи діоксид вуглецю (CO2) і металеве залізо. Доменна (шахтна) піч влаштована так, щоб реакція могла протікати безперервно. На практиці зверху вниз по шахті печі безперервно просуваються вуглець і оксид заліза, а назустріч їм знизу рухається повітря. Вуглець у вигляді коксу грає двояку роль: при згорянні він нагріває піч і утворює газ CO, який відновлює оксид заліза до металу. У верхній частині печі з неї відводиться діоксид вуглецю, а в нижній - випускається рідкий метал. Зазвичай піч працює безперервно до її зупинки для ремонту внутрішньої цегляної кладки (футеровки).
Зі сказаного вище випливають основні вимоги до конструкції доменної печі. Вона повинна забезпечувати безперервну завантаження паливом, рудою і флюсом зверху, безперервну подачу повітря і періодичний відведення рідких продуктів знизу. Піч повинна бути досить високою, щоб встигали протікати необхідні хімічні реакції. Повітря вдувається в піч через фурми, розташовані в її нижній частині, і піднімається крізь шихту вгору. Відновлене губчасті залізні і шлак плавляться на рівні «заплічок», в найширшій частині печі, а рідина накопичується в горні, нижче фурм. У горні періодично пробивають забиті глиною летку для випуску металу і (трохи вище) шлакову летку. Доменна піч дає майже стільки ж шлаку, скільки і чавуну. Затвердевая, шлак перетворюється в темний склоподібний матеріал, який в минулому накопичувався в великих шлакових відвалах біля передільних металургійних заводів. В наші дні шлак йде на виготовлення заповнювача для бетону, залізничного баласту, шлаковати і протівоюзового покриття автомобільних доріг.
Сучасна доменна піч є велике спорудження. Висота печі, що виробляє 1000 т чавуну на добу, становить близько 30 м, а діаметр на рівні заплічок - ок. 8 м. Піч встановлюється на бетонному фундаменті, на якому в сталевому кожусі виводиться кладка з вогнетривкої цегли. Нижня частина цієї конструкції охолоджується водою.
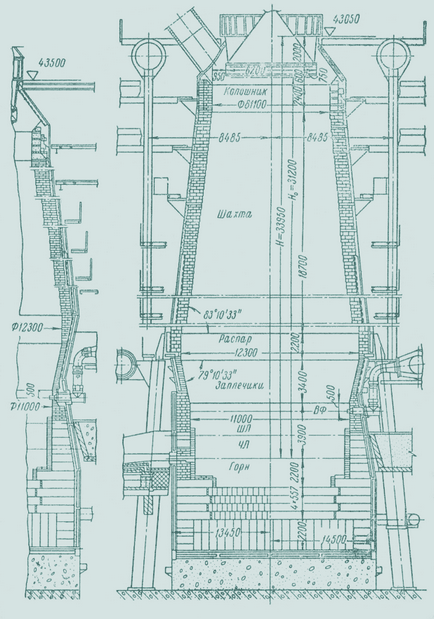
Хоч які значні розміри доменної печі, сама вона - лише мала частина чугуноплавильного заводу. Для її нормальної роботи потрібні ще відділення шихтових матеріалів, вантажопідйомні пристрої для завантаження печі, насоси для подачі повітря (дуття) і повітронагрівачі (Каупер), шлаковози і ливарний цех або приймальна система для розплавленого металу. Для завантаження доменних печей іноді застосовуються стрічкові конвеєри, але частіше руда, паливо і флюс подаються скіповими підйомниками - невеликими судинами (скіпа), що рухаються на колесах по похилих рейках від нижніх засипних бункерів до верхньої завантажувального майданчика, де вони автоматично перекидаються, розвантажуючи в прийомну лійку засипного апарату.
Ефективність доменної печі істотно підвищується при використанні гарячого дуття. Повітря, що підводиться до фурмам, попередньо нагрівається до температури, яка може досягати 1000 ° C. Нагрівання здійснюється в кауперах, кожен з яких не набагато поступається в розмірах самої доменної печі. Каупер є вертикальний циліндричний сталевий кожух з внутрішньої «шахової» насадкою з вогнетривкої цегли.
Газ, що відводиться з верхнього кінця доменної печі, містить монооксид вуглецю та інші гази, здатні горіти. Цей газ по широким похилим газоходам підводиться до нижньої частини Каупера, де, пройшовши через пиловий фільтр, спалюється в камері горіння. Продукти горіння піднімаються вгору, нагріваючи цегляну насадку. Коли насадка досить нагріта, перекривають подачу палива і газу в камеру горіння і включають повітродувки, які женуть повітря через Каупер у фурми доменної печі. Для кожної доменної печі зазвичай передбачають чотири Каупера: два нагріваються, а два інших подають гаряче дуття. Потоки газу і повітря періодично переключаються так, що безперервно підтримується задана температура дуття.
Існує ряд способів додаткового підвищення ефективності доменної печі. Один з них - робота при тиску внутрішніх газів, вдвічі перевищує атмосферне. Це дозволяє підвищити продуктивність приблизно на 15% і знизити споживання коксу приблизно на 10%. Економічні переваги підвищення продуктивності в якійсь мірі знижуються витратами на більш потужне повітродувне обладнання і можливим зменшенням терміну служби вогнетривкої кладки.
При випуску плавки з доменної печі шлак витікає зі своєї льотки, а метал - зі своєї, розташованої нижче. Раніше шлак заливали в шлаковози - великі ковші на залізничних колісних візках, які доставляли незатверділий шлак до відвалам. Тепер же шлак зазвичай відводять на переробну установку, розташовану поруч з домною, де він охолоджується водою і при цьому гранулюється, після чого використовується як заповнювач для бетону та ін.
Рідкий метал, що випливає з льотки, прямував по жолобах, підготовленим в пісочної «ліжку» перед піччю. З жолобів він розтікався по подовженим бічним заглибинах в піску, де і затвердевал у вигляді болванок, званих чушками (через схожість з численними поросятами, що смокчуть свиноматку). Хоча лиття в пісок припиняє застосовуватися, метал, що виплавляється в доменних печах, як і раніше називають чушкового (застосовується і термін «багнетною» чавун). У наші дні в тих випадках, коли потрібно чушковий чавун, розплавлений метал розливають по сталевим ливарним формам, безперервно рухаються перед домною на стрічковому конвеєрі. Коли метал твердне, форми перевертаються і, звільнившись від чушки, повертаються за наступною відливанням. Щоб чавун не приставав до форм, їх покривають кам'яновугільної смолою або вапном.
Настав час випуску чавуну, для чого необхідно було просвердлити отвір в річки, через яке гарячий метал покине доменну піч. Японський горновий дістав з кишені мініатюрний пристрій і підніс його до рота. Пролунав свист, складний механізм приступив до дії: повернувся до річки, знайшов потрібну позицію, пробурив отвір і відійшов в початковий стан. Після закінчення випуску, все той же свисток скомандував "розумної" машині повернутися до річки і закупорити її. Чи це не фантастика? Ні, це сьогоднішній день нашої металургії. Хто ж це зробив? Екологи? Ні! Металурги і фахівці з автоматизації, які чудово володіють специфікою металургійних процесів. Мало знати екологічні проблеми, недостатньо просто володіти програмуванням і знати електронну техніку. Тільки симбіоз знань по металургії і проблемам комп'ютеризації може дозволити ефективно вирішувати проблеми поліпшення умов праці в чорній металургії, зробивши її "металургією в білих рукавичках". Настає час геть забути про кострубатих і брудних робах і перейти до клавіатури комп'ютера, переносячи свої зусилля на мозкову діяльність, пов'язану з тим - що, де, як і чому відбувається. І в кінцевому підсумку, яке рішення ми повинні прийняти в тій чи іншій ситуації.
Основи металургії, тт. 1-6. М. 1961-1973
Струмилин С.Г. Вибрані твори. Історія чорної металургії в СРСР. М. +1967.
1 Струмилин С.Г. Вибрані твори. Історія чорної металургії в СРСР. М. +1967.