Основні процеси виготовлення плівкових матеріалів
Виробництво плівок характеризується високим ступенем механізації і автоматизації. Разом з тим, виробництво ще занадто різноманітне і не виявлені оптимальні методи і схеми.
В даний час застосовуються три методи виробництва плівок: каландрові, екструзійний, пневморастяженіем.
Кожен метод має свої достоїнства і дозволяє отримати плівку певної якості.
Каландрові метод виробництва плівки. Полівінілхлоридний пластикат або гранульований поліетилен пластикується на вальцях, а потім формують в плівку на Z-образному четирехвалковую каландрі. Схема каландровій лінії представлена на рис. 48. З цієї схеми видно, що поліетилен або полівінілхлорид спочатку змішують з інгредієнтами на перших вальцах при 160 ° С. Другі вальці нагріті до температури приблизно на 5 ° С нижче, щоб підвищенням в'язкості збільшити напругу зсуву і, отже, ефект змішування.
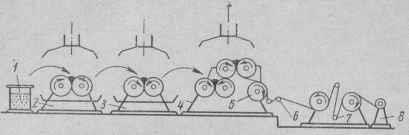
Мал. 48. Схема каландрового способу виробництва плівки: 1 - полімер (пластикат); 2, 3 - вальці; 4 - каландр; 5 - охолоджуючий валок; 6 - пристосування для розгладження плівки; 7 - охолоджуюча лінія; 8 - намотування готової плівки.
Температури валків каландра послідовно рівні 145, 150, 155, 160 ° С. Залежно від типу матеріалу, товщини виготовленої плівки і швидкості її відбору робочі температури можуть бути трохи нижче або вище.
Температура охолоджуючого валка зазвичай дорівнює 120 ° С. Якщо потім для досягнення підвищеної прозорості плівка миттєво охолоджується водою, то температура охолоджуючого валка Каландра встановлюється на 20 ° С вище температури кристалізації розплаву.
При отриманні поліетиленових і полівінілхлоридних плівок на каландрі валки його працюють з зростаючій від першого до четвертого окружною швидкістю. Якщо плівка оптично неоднорідна (має різні інгредієнти), то краще каландрованні її з постійною швидкістю. Методом каландрования можна виготовляти плівки товщиною 0,08-1,0 мм. Цей діапазон товщини задовольняє вимогам до матеріалів виробів зі шкіри.
Екструзійний метод виробництва плівки. Для отримання плівок високої прозорості і високої продуктивності (60-120 м / хв) застосовується метод екструзії - витискування (шприцювання) через щілинну головку екструдера. Схема установки для виготовлення плівки екструзією представлена на рис. 49.
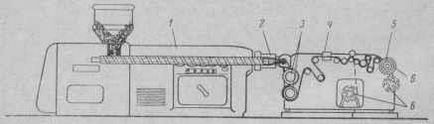
Мал. 49. Схема екструзійного способу виробництва плівки з охолодженням на валках: 1 - екструдер, пластифікуючий полімер; 2 - щілинна головка, через яку видавлюється розплавлений полімер; 3 - охолоджуючі валки; 4 - радіоактивний калібромер для контролю за товщиною плівки; 5 - пристосування для намотування плівки; 6 - пристосування для намотування обрізаних кромок.
Екструдер (шприц-машина) являє собою гвинт (або, як його ще називають Черняк або шнек), укладений в кожух з обігрівом. Полімерний матеріал у вигляді гранул засипають в приймальний бункер. Під впливом високої температури полімерний матеріал розплавляється і пересувається черв'яком до щілинної голівці. Переробка здійснюється на черв'яків дуже великої довжини: ставлення його довжини до діаметру дорівнює 20.
Розплав видавлюється на екструдері через щілинну головку з розмірами щілини: ширина - до 2,5 м, товщина 0,01-0,7 мм (рис. 50). Дуже важливим і тонким процесом є подальше охолодження утворюється плівки: він визначає майбутні властивості і зовнішній вигляд плівки. Температура головки при виготовленні поліетиленової плівки 250-280 ° С.
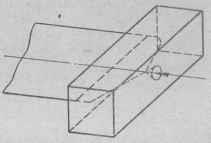
Мал. 50. Схема течії розплаву в щілинний голівці.
У схемі на рис. 49 охолодження здійснюється на валках. Валки хромовані і ретельно відполіровані. Після охолоджуючих валків встановлюється радіоактивний γ-калібромер, контролюючий товщину получающейся плівки.
За нею йдуть пристосування для обрізки крайок і пристосування для намотування з приводом, що забезпечує постійне зусилля намотування.
В даний час впроваджується метод охолодження у водяній ванні. Схема екструзійної установки з охолодженням у водяній ванні для виробництва плівки представлена на рис. 51. Плівка з щілинної головки видавлюється в ванну, де охолоджується і набуває остаточну форму і блиск.
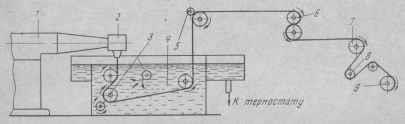
Мал. 51. Схема екструзійного способу виробництва плівки з охолодженням у водяній ванні: 1 - екструдер; 2 - щілинна головка; 3 - вхід охолоджуючої води (від термостата); 4 - перегородка для забезпечення спокійної поверхні води; 5 - пристосування для обрізки крайок; 6 - відводять ролики; 7 - розгладжує валок; 8 - натяжний пристрій; 9 - намотувальний пристрій.
За нею йдуть, як зазвичай, обрізка крайок і намотувальний пристрій. Температура ванни від 30 до 76 ° С - в залежності від виду полімеру. Взагалі підвищення температури охолоджуючої води покращує механічні властивості плівок, але знижує економічні показники процесу. Більш товсті плівки повинні охолоджуватися при температурах нижчих, ніж тонкі.
До числа недоліків екструзійного методу потрібно віднести порівняно невелику ширину одержуваної плівки (не більше 2,5-3 м) і нерівномірні (анізотропні) механічні властивості плівки через сильну поздовжньої витяжки.
Виробництво плівки методом пневморастяженія. Найбільш перспективним методом отримання плівок є метод пневморастяженія (рис. 52). Цей метод забезпечує отримання дуже широкої плівки (до 12 м) з механічними властивостями вище, ніж в разі двох попередніх методів. Плівки відрізняються високою прозорістю.
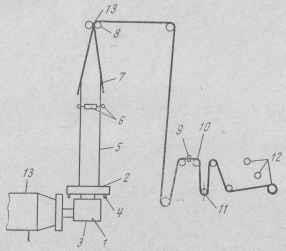
Мал. 52. Схема виготовлення плівки способом пневморастяженія: 1 - кільцева головка екструдера; 2 - охолоджувальний кільце; 3 - отвір для подачі повітря всередину рукава; 4 - отвір для подачі повітря в охолоджуючу кільце; 5 - роздувається рукав плівки; 6 - напрямні ролики; 7 - стискають щоки, додають плівку; 8 - затискні ролики; 9 - механізм для обрізки крайок плівки; 10 - тягнуть ролики; 11 - натяжна ролик; 12 - намотувальний пристрій; 13 - екструдер.
Розплавлений полімерний матеріал надходить в головку екструдера (шприц-машини) з кільцевої щілиною.
Розплавлена маса видавлюється через цю кільцеву щілину у вигляді циліндричної труби і кілька охолоджується повітрям, а що утворився рукав роздувається вступником знизу стисненим повітрям.
У верхній частині установки рукав складається напрямними роликами і щільно затискається тягнуть роликами. Плівка у вигляді подвійної плоскої стрічки намотується на закочувати ролик. При бажанні отримати широку плівку у цій подвійній плоскої стрічки обрізають край з одного боку. В результаті виходить плівка з шириною, що дорівнює периметру роздутого рукава (без обрізаного краю). Якщо потрібна тонка плівка, то обрізають обидва краї цієї подвійної стрічки і приймають дві плівки з половинкою шириною на два закочувати ролика. Швидкість прийому плівки на подібних установках 3-30 м / хв. Регулювання товщини і механічних властивостей плівки відбувається завдяки поздовжньої витяжці і ступеня роздування, величина якої легко регулюється.