Категорія екструзія
Екструзія застосовується для виробництва плівок, труб, профілів, листів з полімерів. Крім того, цей метод переробки використовується для випуску сучасної теплоізоляції.
Пінополістирол екструзійний - досить давно використовується для теплоізоляції різних поверхонь, особливо широко його застосування при будівництві - для теплоізоляції фундаментів, бетону і навіть залізниць. В результаті застосування цього матеріалу істотно знижується ризик зміни поверхні грунту в результаті промерзання.
Даний вид спіненого полістиролу, а також пластикові труби, листи, плівки та профілі виходять шляхом екструзії, тобто продавлювання матеріалу через спеціальну фільєру, яка надає йому форму.
Формування профілів, труб, плівок, листів і спіненого екструзійного пінополістиролу здійснюється на спеціальних екструзійних лініях, які представляють собою один з найпоширеніших типів обладнання для переробки пластмас, як правило складається з одного або декількох екструдерів, екструзійного інструменту і ряду додаткових пристроїв.
Екструзія - спосіб отримання виробів або напівфабрикатів з полімерних матеріалів необмеженої довжини шляхом видавлювання розплаву полімеру через формующую головку (фільєру) потрібного профілю. Екструзія, поряд з литтям пластмас під тиском, є одним з найпопулярніших методів виготовлення пластмасових виробів. Екструзії піддаються практично всі основні типи полімерних матеріалів, як термопласти, таки і реактопласти, а також еластомери.
В основному для екструзії пластмас застосовують шнекові, або черв'ячні, екструдери. Також існують дискові екструдери. Для успішного виробництва продукції методом екструзії недостатньо тільки одного екструдера. Крім нього необхідно мати ще кілька одиниць обладнання, разом складових екструзійну лінію. Крім того, існують видувні екструдери, які застосовуються в установках по одержанню виробів методом екструзійно-видувного формування. Їх опис, не входить в дану статтю. Практично не зустрічаються екструдери з вертикальними шнеками.
1. Черв'ячні екструдери підрозділяються на Одношнекові, двухшнековие і многошнековий.
Найбільш простим устаткуванням для екструзії є одношнековий (однечерв'ячні) екструдер без зони дегазації (рис. 1). Такі екструдери широко застосовуються для виробництва плівок, листів, труб, профілів, в якості однієї зі складових частин ліній-грануляторів і т.д. Основними елементами екструдера є обігрівається циліндр, гвинтовий шнек (з охолодженням або без нього), сітки, що розміщуються на решітці, і адаптер.
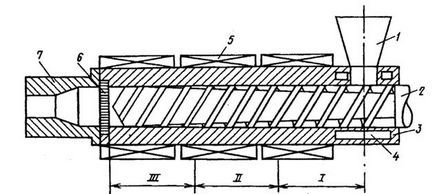
Мал. 1. Схема одношнекового екструдера: 1 бункер; 2 черв'як (шнек); 3 циліндр; 4 порожнину для циркуляції води; 5 нагрівач; 6 решітка з сітками; 7- формуюча головка з адаптером.
Залежно від природи полімеру, технологічних режимів переробки застосовуються шнеки різного профілю з різним кроком і глибиною витків. Залежно же від виду виробу, що випускається застосовують або коротко-, або длінношнековие машини, т. Е. З малим або великим відношенням довжини L до діаметру D шнека (L / D). Значення D і L / D є основними характеристиками одношнекового екструдера. Типорозмірний ряд екструдерів, що випускалися в Радянському Союзі був заснований на діаметрах шнека: D = 20; 32; 45; 63; 90; 125; 160; 200; 250 і 320 мм.
2. Двошнекові екструдери можуть застосовуватися як в тих же випадках, що і Одношнекові, так і в спеціальних умовах, коли Одношнекові екструдери не справляються з завданнями. В українських реаліях двухшнековие екструдери в переважній більшості випадків використовуються для екструзії ПВХ (полівінілхлориду) в вироби будівельного призначення. Технологія процесу екструзії ПВХ часто має на увазі застосування порошкоподібного основної сировини (ПВХ-композиції), яку неможливо переробити на стандартній одношнекових екструзійної лінії. Як правило, двушнековие екструдери в обов'язковому порядку оснащуються пристроєм дегазації. Двухшнековие екструдери розрізняють двох основних типів:
- екструдери зі шнеками, що знаходяться в зачепленні (з односпрямованим або протилежно спрямованим обертанням шнеків);
- екструдери зі шнеками, що не перебувають в зачепленні (з односпрямованим або протилежно спрямованим обертанням шнеків).
3. многошнековий екструдери застосовуються порівняно рідко. До таких екструдера можна віднести четирехшнековий екструдер, а також планетарний екструдер. Черв'ячна система останнього складається з одного центрального черв'яка і ще, як правило, 6 додаткових шнеків, розташованого навколо основного на однаковому радіальному відстані. Ці шнеки називають планетарними, звідси і назва екструдера. Така конструкція дозволяє переробляти матеріали, схильні до швидкої термічної деструкції (часто - композиції ПВХ) без застосування високих температур, але зі значним змішувальним ефектом і інтенсивної дегазацією розплаву.
4. Дискові екструдери відносяться до досить рідкісного типу екструзійних машин сучасності. Робота дискового екструдера заснована на переміщенні полімерного матеріалу і створенні тиску за рахунок адгезії полімеру до рухомих частин екструдера. Такі екструдери можуть бути як однодисковими, так і багатодисковими. Останній є найбільш сучасним варіантом і дозволяють давати тиск розплаву на виході в кілька разів перевищує тиск розплаву стандартного одношнекового екструдера. Однак, зазвичай це перевага нівелюється високою вартістю багатодискового екструдера внаслідок його конструкційної складності.
Поведінка полімеру при екструзії
Поведінка полімеру всередині екструдера розглянемо на прикладі одношнекових екструзії гранульованого матеріалу. Технологічний процес екструзії складається з послідовної пластикации і переміщення матеріалу обертовим шнеком в зонах матеріального циліндра. Розрізняють такі зони - харчування (I), пластикации (II), дозування розплаву (III).
Можна сказати, що поділ шнека на зони I-III досить умовно, воно здійснюється за технологічною ознакою і вказує на те, яку операцію в основному виконує дану ділянку шнека. Циліндр також має певні довжини зон обігріву. Довжина цих зон визначається розташуванням нагрівачів на його поверхні і їх температурою. Межі зон шнека I-III і зон обігріву циліндра можуть не збігатися. Для забезпечення успішного переміщення матеріалу велике значення мають умови просування твердого матеріалу з завантажувального бункера і заповнення межвиткового простору, що знаходиться під лійкою бункера.
Завантаження сировини. Полімерний матеріал для екструзії, що подається в бункер, може бути у вигляді порошку, гранул, стрічок. Останній вид сировини характерний для переробки відходів промислового виробництва плівок і здійснюється на спеціальних екструдерах, забезпечених примусовими живильниками-дозаторами, що встановлюються в бункерах. Рівномірний дозування матеріалу з бункера забезпечує хорошу якість екструдата.
Найбільш часто екструзією переробляються гранульовані пластики. Переробка полімеру у вигляді гранул - оптимальний варіант харчування екструдера. Гранули полімеру менше схильні до "зависання" і утворення пробок в бункері, ніж порошок, а також гранули легше пластикується і гомогенізуються.
Завантаження межвиткового простору щнека під лійкою бункера відбувається на відрізку довжини шнека, що дорівнює (1 - 1,5) D. При переробці багатокомпонентних матеріалів для завантаження їх в бункер застосовуються індивідуальні дозатори: шнекові (об'ємні), вібраційні, вагові та т. П. Сипучість матеріалу сильно залежить від його вологості: чим більше вологість, тим менше сипкість. Тому гігроскопічні матеріали необхідно сушити перед завантаженням в екструдер.
Застосовуючи пристосування для примусової подачі матеріалу з бункера в матеріальний циліндр, також вдається істотно підвищити продуктивність машини. При ущільненні матеріалу в межвиткового просторі шнека витіснений повітря виходить назад через бункер. Якщо видалення повітря буде неповним, то він залишиться в розплаві і після проходження через головку утворює в виробі небажані порожнини.
При тривалій роботі екструдера можливий перегрів циліндра під лійкою бункера і самого бункера. В цьому випадку гранули почнуть злипатися і припиниться їх подача на шнек. Для запобігання перегріву цієї частини циліндра в ньому робляться порожнини для циркуляції охолоджуючої води. Зазвичай зона завантаження є єдиною охолоджувальної зоною сучасних екструдерів.
1. Зона харчування (I). Вступники з бункера гранули або порошок полімеру заповнює межвитковое простір шнека зони I і ущільнюється.
2. Зона пластикации і плавлення (II). У зоні II відбувається Підплавлення полімеру, що примикає до поверхні циліндра. У тонкому шарі розплаву полімеру відбуваються інтенсивні зсувні деформації, як наслідок матеріал пластикується, що призводить до інтенсивного змішувальному ефекту.
Основний підйом тиску P розплаву відбувається на кордоні зон I і II. На цьому кордоні утворюється пробка з спресованого матеріалу як би ковзає по шнеку: в зоні I це твердий матеріал, в зоні II- плавиться. Наявність цієї пробки і створює основний внесок в підвищення тиску розплаву. Запасеної на виході з циліндра тиск витрачається на подолання опору сіток, течії розплаву в каналах головки і формування екструдіруемого профілю.
3. Зона дозування (III). Розплавлена маса полімеру продовжує гомогенізований, проте вона все ще не є однофазної і складається з розплавлених і твердих частинок. В кінці зони III пластик стає повністю однорідним і готовим до продавлювання через чистять сітки і формующую головку.
Основні параметри процесу екструзії
До технологічними параметрами переробки пластмас методом екструзії відносяться:
- температура по зонам екструдера
- тиск розплаву,
- температура зон головки
- режими охолодження екструдованого профілю
Основними технологічними характеристиками екструдера є довжина шнека L, діаметр шнека D, співвідношення L / D, швидкість обертання шнека N, а також профіль шнека і ступінь зміни обсягу каналу шнека.
Основною характеристикою формуючого інструмента, що складається в основному з екструзійної головки (разом з фільтруючими сітками) і калібрує вузла, є коефіцієнт опору течією розплаву K. Перепад тиску на фільтруючих сітках служить показником засмічення, т. Е. Збільшення опору сіток і, отже, сигналом до їх заміні.
Укрупненим показником роботи будь-якого екструдера можна назвати його ефективність, вимірювану як відношення продуктивності екструдера до його споживаної потужності.
Обслуговувати стандартний одношнековий екструдер нескладно. Для підготовки оператора екструдера зазвичай потрібно від одного до декількох місяців. Ремонт і обслуговування одношнекового екструдера зводиться до заміни і прочищення фільтруючих сіток, заміні трансмісійного масла в приводі, заміни електричних запобіжників, ремонт або заміна нагрівачів циліндра. Після напрацювання прописаного виробником екструдера кількості машино-годин необхідно розібрати екструдер і замінити при необхідності шнек і циліндр.
До необхідної технічної документації на екструдер відноситься:
- Паспорт на екструдер, що випускається заводом-виготовлювачів
- Електрична схема екструдера
- Опис роботи екструдера (часто входить до складу паспорта)
- Складальне креслення екструдера
У висновку варто знову зупинитися на тому, що в сучасних умовах екструдер як такої рідко здатний вирішити завдання, які стоять перед переробниками пластмас. Відповідно до технологічних схем, що використовуються в наші дні, необхідне застосування екструзійних ліній. У них, крім екструдера, можуть входити:
- калібру пристрій
- Ко-екструдери
- охолоджуючі ванни
- тягнучий пристрій
- Маркіруюче пристрій
- ламінуванн пристрій
- Відрізне / намотувальний пристрій
- Інші допоміжні технологічні одиниці
На жаль, промислове виробництво екструдерів і екструзійних ліній вУкаіни практично згорнуто. Компанії, що пропонують екструзійне обладнання на нашому ринку, як правило, займаються купівлею обладнання за кордоном і наступним продажем вУкаіни. Дещо інша ситуація спостерігається на Україні, де ще зберігаються спеціалізовані машинобудівні підприємства.