Деталі з пластмас
Способи виготовлення деталей
Листи і плити з термопластів найчастіше виготовляють Каландрирование - вальцюванням на багатовалкових прокатних верстатах. Вальцюванням на профільних валках виготовляють також гофровані листи для сотопластов. Фасонні вироби з листів отримують пресуванням в матрицях жорстким або пружним пуансоном (повітронаповненим гумовим мішком)
При пневматичному формуванні листову заготовку, нагріту до пластичного стану, затискають по периметру матриці, після чого тиском стисненого повітря осаджують заготовку на матрицю. При вакуумному формуванні всередині матриці створюють вакуум, в результаті чого заготовка втягується в матрицю, облягаючи її поверхню. Таким способом виготовляють фасонні кришки, відкриті резервуари, обтічники, коки та інші тонкостінні вироби
пресування
Пресування застосовують для виготовлення фасонних виробів з реактопластів і отверждаємих термопластів. Вихідним матеріалом служать таблетки, гранули, крихта; для виробів з порошковими наповнювачами - прес-порошки. Процес здійснюють в прес-формах, що складаються з матриці і пуансона. Формування проводиться при підвищеній температурі (прес-форми нагрівають), що забезпечує затвердіння матеріалу
У матрицю засипають мірне кількість попередньо підігрітого прес-матеріалу, після чого до пуансону прикладають механічне або гідравлічне зусилля і піддають виріб короткочасної витримки в формі під постійним тиском, в результаті чого відбувається затвердіння матеріалу. Потім пуансон відводять; а затверділе виріб з матриці віддаляється виштовхувачами
Режими формування (температура попереднього підігріву, температура і тиск пресування, тривалість витримки) залежать від рецептури прес-матеріалу, від розмірів і конфігурації вироби і підбираються дослідним шляхом. Зазвичай температура попереднього підігріву 130-180 ° С, температура пресування 200-220 ° С, тиск пресування 100-300 кгс / см 2 тривалість витримки 15 - 30 з
Якість поверхні деталей високе. При належній обробці оформляють поверхонь матриці і пуансона (хромування, полірування) можна отримати поверхню шорсткістю Ra = 0,080 - 0,160 мкм
Лиття під тиском
Лиття під тиском застосовують для формування термопластів. Вихідний матеріал (гранули, таблетки) піддають нагріванню до повного розм'якшення. Ливарна маса рідких консистенції подається в обігрівається циліндр, звідки видавлюється поршнем через літніковие канали в охолоджувані металеві форми. Після охолодження і затвердіння прес-форма розкривається, і виливки видаляються виштовхувачами. Літники і задирки, які утворюються в порожнині роз'єму форми, обрубують і зачищають. Температура розм'якшення литтєвий маси залежить від її складу. Тиск пресування 1000 - 1500 кгс / см 2. Температура форми 20-40 ° С
Лиття під тиском більш продуктивно і забезпечує більш високу і рівномірний якість виробів, ніж пресування. Можна отримати поверхню шорсткістю Ra - 0,020 - 0,040 мкм
Для усунення внутрішніх напружень і збільшення однорідності структури виливки піддають нормалізації. нагрів без доступу повітря (зазвичай в мінеральному маслі) при 140-160 ° С протягом 1,5-2 год з подальшим повільним охолодженням
Екструзійне формування застосовують для виготовлення з термопластів прутків, труб, шлангів, плит, плівок, фасонних профілів (поручнів, плінтусів і т. Д.) Процес здійснюється на шнекових пресах безперервної дії (екструдерах). Ливарна маса подається через завантажувальний бункер в обігрівається циліндр шнека, підхоплюється витками шнека (в свою чергу підігрівається) і переміщається уздовж циліндра, піддаючись перемішування і ущільнення. Ущільнення маси досягається зменшенням кроку або висоти витків шнека. На вихідному кінці циліндра встановлюють фільєру з отвором, відповідному формі поперечного перерізу вироби. Відформоване виріб, що виходить безперервним джгутом з фільєри, охолоджується. Після затвердіння його ріжуть на шматки необхідної довжини
формування склопластів
Малогабаритні вироби з склопластів отримують гарячим пресуванням в металевих формах
Великогабаритні оболонкові конструкції найчастіше виготовляють методом набризкування на модель наведеного в в'язко-текучий стан пластика разом зі скляним волокном. Пластик і нарубані волокно подають в потрібній пропорції в розпилювач. Що виходить з розпилювача струмінь наносять на модель до утворення шару потрібної товщини
Позитивні моделі. відтворюють внутрішній контур вироби, застосовують у випадках, коли треба отримати гладку і точну внутрішню поверхню. Негативні моделі. відтворюють зовнішній контур вироби, застосовують для отримання чистої і точної зовнішньої поверхні
При виготовленні виробів з пластиків холодного затвердіння моделі роблять з дерева, гіпсу, цементу, а також з термореактивних пластиків. При гарячому отверждении застосовують металеві підігріваються моделі. Поверхня нанесеного на модель шару ущільнюють прикочуванням роликами або обпресуванням стисненим повітрям
Точність розмірів виробів, одержуваних методом набризкування, невелика. У великогабаритних деталей різницю в розмірах може досягати декількох міліметрів. Міцність таких виробів поступається міцності виробів, пресованих під високим тиском
Для виготовлення порожнистих деталей, що мають форму тіл обертання (труби, конуси і т. Д.), Застосовують метод намотування на обертову оправку безперервних пасом скляного волокна, просочених синтетиком. Прядепітатель встановлюють на супорті, що здійснює зворотно-поступальний рух щодо оправлення. Намотування зазвичай виконують наперекрест декількома шарами. Намотувати шари, ущільнюють роликами
При виготовленні високоміцних плит з орієнтованою волокном намотування виробляють на барабан великого діаметру, розрізають ще неотверділі обмотку по котра утворює, розправляють і піддають пресуванню в плоских або фігурних штампах
Сварка пластмас
Термопласти всіх видів добре піддаються зварюванні. Високоеластичні пластмаси (полиолефини, поліаміди, поліметилметакрилати) зварюють контактної зварюванням без застосування присадочного матеріалу. Тонкі листи і плівки зварюють внахлестку пропусканням плівок між роликами, що підігріваються електричним струмом. Плити, бруски та інші подібні вироби зварюють встик. Зварювані поверхні стискають під тиском 1-3 кгс / см 2; стик розігрівають струмами високої частоти або ультразвуком. Міцність зварного стику близька до міцності самого матеріалу
Пластмаси меншою пластичності (Вініпласти, фторопласти) зварюють із застосуванням присадочного прутка, отриманого з того ж матеріалу, що і деталі, що зварюються, але з добавкою пластифікатора. Сполучаються кромки обробляють для освіти, зварювальної ванни. Зварювання виробляють струменем гарячого повітря. Міцність зварного шва становить 70- 80% міцності самого матеріалу
Пластмаси добре склеюються за допомогою клеїв, що представляють собою розчин даного полімеру у відповідному розчиннику. Деякі клеї (ацетат полівінілу, фенолнеопреновие, на основі модифікованих епоксидів та ін.) Мають широку універсальністю по відношенню до склеюваних матеріалами. Цими клеями можна склеювати пластмаси з металом, склом, керамікою і т. Д
Правила конструювання пластмасових деталей
Проектування деталей слід починати з того, що необхідно намітити площину роз'єму, визначальну конфігурацію деталі, напрям формувальних ухилів, розташування отворів та розміщення арматури.
Як правило, форма повинна мати тільки одну площину роз'єму. Роз'єм за кількома площинах ускладнює конструкцію. Особливо небажані додаткові роз'єми в напрямку, перпендикулярному напрямку основного роз'єму
Слід мати на увазі, що позитивні, т. Е. Опуклі частини форми, що утворюють внутрішні поверхні деталі, обробляти простіше, ніж негативні (гнізда матриць), що утворюють зовнішні поверхні деталі. Тому всі складні профільні елементи деталі рекомендується переносити на внутрішні поверхні, намагаючись надати зовнішніх поверхнях найпростіші обриси. Профільні поверхні рекомендується розташовувати так, щоб формуючі поверхні можна було виконати тільки в матриці
Товщина стінок. Слід уникати місцевих масивів і потовщень. Стінок деталі слід надати по можливості однакову товщину. Практично встановлено, що разностенность деталі не повинна перевищувати 1: 3. Переходи між стінками різної товщини повинні бути плавними
Збільшення товщини стінок понад певної межі викликає неоднорідність структури матеріалу поперек стінки і послаблює деталь. Орієнтовно середню товщину стінок фасонних деталей можна визначати за формулою
s = (0,25 - 0,5) √L. де L - максимальний габаритний розмір деталі, мм
Ребра. Збільшення міцності і жорсткості деталей слід домагатися не потовщенням стінок, а за доцільне ребрами деталі. При конструюванні ребер необхідно дотримуватися наступних правил. Товщина ребер повинна бути дорівнює 0,6 - 0,8 товщини стінок, однак (в дрібних деталях) не менше 0,8 - 1 мм. Висота ребер не повинна перевищувати трьох - п'яти товщини ребра. Поверхня ребер слід виконувати з ухилом в бік роз'єму форми. Ребра повинні бути з'єднані зі стінками плавними галтелями. Верхівка ребер повинна бути закруглена.
Ділянки перегину ребер, а також ділянки приєднання до стінок повинні бути виконані з галтелями
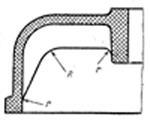
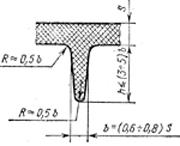
При розташуванні ребер необхідно враховувати, що при затвердінні і охолодженні ребра всідаються і після вилучення з форми деталі стягують її стінки. Тому слід уникати з'єднання ребрами частин деталі, які потребують точних розмірах, наприклад вінців шестерень
Жолобники. Зовнішні та внутрішні кути виробів повинні бути виконані по радіусу. Зовнішні кути вироби, формовані входять кутами гнізда матриці, слід виконувати по радіусу R, погодженим з діаметром пальцевих фрез, що застосовуються для фрезерування гнізда в матриці. Мінімальний радіус заокруглення R = 2 - 3 мм. Радіус заокруглень повинен бути тим більше, чим глибше гніздо. Інакше пальцеві фрези виходять недостатньо жорсткими, що змушує застосовувати при фрезеруванні малі швидкості різання і малі подачі
Деталі ручного управління, а також навертние пробки і ковпачки зазвичай мають рифлення під захоплення пальцями.
Приклади рифлених деталей
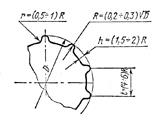
армування деталей
Слід застосовувати арматуру лише в необхідних випадках, так як установка арматури ускладнює конструкцію форми і знижує продуктивність.
Арматура повинна бути зафіксована в прес-формі в поперечному і поздовжньому напрямках
Арматура повинна при роз'ємі форми вільно сходити з фіксуючих елементів. Осі арматури повинні бути перпендикулярні площині роз'єму форми. Розташування деталей паралельно площині роз'єму або під кутом до неї вкрай ускладнює конструкцію форми, вимагаючи застосування розсувних форм або прибираються фіксаторів.
При армуванні деталей стрижнями необхідно забезпечити вільну установку стержня в центрир гнізді і безперешкодне його витяг з гнізда при виштовхуванні деталі. Діаметр вільної частини стержня повинен бути менше діаметра центрирующей частини гнізда. Застосування вигнутих стержнів неприпустимо. В необхідних випадках стрижні слід гнути після формування
Способи кріплення листової арматури
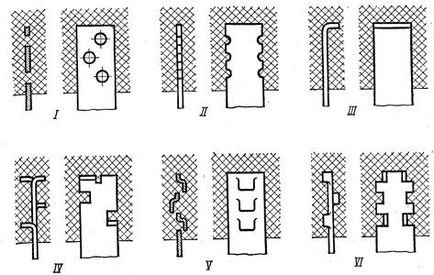
Способи кріплення втулок у виробах і сферичних рукоятках
При конструюванні пластмасових деталей слід крім технологічних факторів враховувати механічні властивості пластмас: м'якість, малу жорсткість, низьку міцність, а у реактопластов - крихкість.
Знижену жорсткість пластмасових деталей слід компенсувати ребрами, введенням на вільних стінах реборд жорсткості доданням деталі жорстких склепінних форм. Слід всіляко намагатися не навантажувати деталі изгибающими зусиллями, а замінювати їх більш вигідними зусиллями стиснення. Неприпустимо навантажувати деталі изгибающими зусиллями від затягування кріпильних деталей. Для усунення зминання опорних поверхонь, при силовий затягуванні слід підкладати під головки кріпильних деталей опорні шайби досить великого діаметра або підсилювати отвори під кріпильні деталі втулками
Пластмасові зубчасті колеса
Пластмасові зубчасті колеса застосовують (в парі з металевими шестернями) в передачах, що несуть помірні навантаження (допоміжні приводи, приводи приладів і т. Д.). Передачі з пластмасовими зубчастими колесами відрізняються безшумністю, плавністю ходу і (при правильно обраної навантаженні на зуби) високою довговічністю. Пластмасові колеса можуть працювати при мізерної мастилі, а при невеликих навантаженнях і малих окружних швидкостях - без змащення
При орієнтовних розрахунках можна виходити з умови, що навантаження на 1 см ширини зуба не повинна перевищувати 20 - 30 кгс / см для посилених пластиків (тканинних і шаруватих) і 15 - 20 кгс / см для пластиків, без наповнювачів. (Для порівняння зазначимо, що питоме навантаження в сталевих шестернях з загартованим або азотированного зубом досягає 200 кгс / см, а в окремих випадках 500 кгс / см). Поряд зі зниженою міцністю слід враховувати низьку теплопровідність пластиків, що утрудняє тепловідвід від поверхонь тертя
Для виготовлення зубчастих коліс застосовують переважно текстоліт, древеснослоїстиє пластики, капрон, нейлон та Поліформальдегіди. Текстолітові і древеснослоїстиє колеса виготовляють механічною обробкою; капронові, найлоновая і поліформальдегідние колеса - литтям під тиском.
Умова міцності і довговічності коліс з текстоліту і деревно-шаруватих пластиків полягає в тому, щоб шари тканини (або дерева) були спрямовані перпендикулярно робочих поверхонь зубів
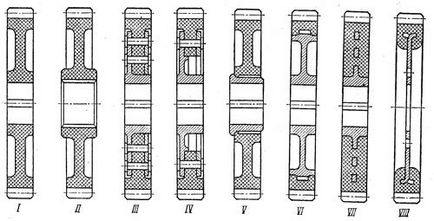
На малюнку представлені способи кріплення пластмасових коліс на валах. Установку коліс безпосередньо на валу з передачею крутного моменту шпонкой (I) застосовують тільки для слабонавантажених коліс через небезпеку розбивання з'єднання. При підвищених навантаженнях доцільно застосовувати посадку на шліцах зі збільшеним діаметром і довжиною маточини (II).
Міцніше і надійніше установка на дискових маточинах (III, IV) з кріпленням коліс до диска заклепками або болтами. Обов'язкова установка під головки заклепок (а також під гайки і головки болтів) масивних підкладних шайб.
У литих зубчастих коліс передбачають посадочні пояса, армовані сталевими втулками (V). Високою міцністю і надійністю відрізняється конструкція VI, де вінець колеса запресовується на диск з рифленим поясом великого діаметру.
На малюнку VII показана конструкція колеса, запресованого на дискову маточину з перфораціями. Легконавантажених зубчасті колеса (VIII) отримують запрессовкой вінця на диск, що приєднується до валу болтами. Вінець фіксується на диску звичайними способами, наприклад лапками, відігнутими в диску
Джерело: П.І. Орлов "Основи конструювання" т.3