Зварювання неплавким електродом
Установки для автоматичного зварювання поздовжніх швів обичайок - в наявності на складі!
Висока продуктивність, зручність, простота в управлінні і надійність в експлуатації.
Зварювальні екрани і захисні шторки - в наявності на складі!
Захист від випромінювання при зварюванні і різанні. Великий вибір.
Доставка по всейУкаіни!
Зварювання неплавким електродом в захисних газах (СНЕЗГ) - це процес, в якому в якості джерела теплоти застосовують дугового розряд, що порушується між вольфрамовим або вугільним (графітовим) електродом і виробом.
Останнім часом зварювання вугільним електродом знаходить обмежене застосування і використовується, як правило, при виготовленні виробів невідповідального призначення.
Як не плавиться найбільш широко застосовують вольфрамові стрижні. Вольфрам - найтугоплавкіший з відомих матеріалів (по температурі плавлення поступається лише вуглецю). Температура плавлення його дорівнює 3645 К, а щільність - 19,3 г / см 3. Вольфрам має низький коефіцієнт теплопровідності [λ 177,8 ÷ 200,7 Вт / (м * К)], найнижчу швидкість випаровування. Оскільки вольфрамові електроди при робочій температурі характеризуються досить високою хімічною активністю до кисню, то в якості захисних газів застосовують аргон, гелій і азот, є по відношенню до вольфрамовим сплавів інертними.
Застосовувані вольфрамові електроди повинні відповідати вимогам ГОСТ 23949-80.
Для зварювання в середовищі інертних газів застосовуються електроди 00,5-10 мм з чистого вольфраму (ЕВЧ), вольфраму з присадками: діоксиду торію (ЕОТ), оксидів лантану (ЕВЛ) і ітрію (Еві).
Приклад умовного позначення електрода марки ЕВЛ ф 2,0 мм, довжиною 150 мм: «Електрод вольфрамовий ЕВЛ-2-150 - ГОСТ 23949-80».
У нас в країні широкого поширення набули електроди марок ЕВЛ і Еві. Вони витримують велику струмовий навантаження і мають підвищену ерозійну стійкість при зварюванні в порівнянні з електродами марки ЕВЧ. Діаметр вольфрамового електрода вибирається в залежності від величини зварювального струму (табл. 2.5). Вольфрамові електроди використовуються з заточкою під кутом 20-90 °.
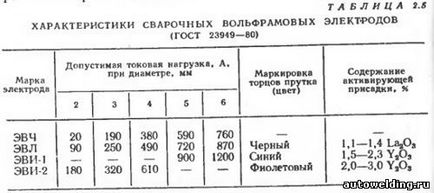
Сварка постійним струмом прямої полярності характеризується максимальною проплавляющей здатністю. У широкому діапазоні параметрів режиму аргонодугового зварювання на постійному струмі прямої полярності на токах до 600 А частка теплової потужності, що вводиться у виріб, становить 40-85%, втрати на нагрів вольфрамового електрода - приблизно 4-6%, а променеві втрати від стовпа дуги - 7-30%.
Сварка на постійному струмі зворотної полярності застосовується для стикових з'єднань з алюмінієвих і магнієвих сплавів. Втрати на нагрівання не плавиться-анода становлять> 50% загальної потужності дуги і в кілька разів перевищують частку потужності, що витрачається на нагрів вольфрамового електрода-катода, т. Е. Енергетично зварювання струмом зворотної полярності невигідна.
Концентрація нагріву на виробі в цьому випадку нижче, шви мають меншу глибину і велику ширину проплавлення, ніж при зварюванні струмом прямої полярності або змінним струмом. Перевагою зварювання дугою зворотної полярності є те, що катодна пляма постійно знаходиться на виробі і внаслідок катодного розпилення відбувається ефективне руйнування оксидної плівки із забезпеченням високої чистоти поверхні зварювальної ванни. Однак значна теплове навантаження на вольфрамовий електрод-анод і небезпека потрапляння матеріалу електрода в шов обмежують потужність дуги і продуктивність цього процесу. Як правило, зварювання ведеться на токах до 150 А Слід зазначити, що низька концентрація нагріву, блукання і відхилення стовпа дуги вкрай ускладнюють зварювання на струмі зворотної полярності кутових з'єднань.
Сварка змінним струмом є найбільш поширеним процесом при виготовленні конструкцій з алюмінієвих і магнієвих сплавів. Руйнування оксидної плівки відбувається в напівперіод зворотної полярності, коли основний метал є катодом. Так як розігрітий вольфрамовий електрод краще еміттіруєт електрони, ніж алюміній, виникає розбаланс струмів прямої і зворотної полярності; він компенсується схемою управління джерела зварювального струму. Компенсація постійної складової зварювального струму забезпечує умови для повного руйнування оксидної плівки.
До складу обладнання для ручного зварювання постійним струмом входять: джерело зварювального струму з крутопадаючих зовнішньої статичної характеристикою (ВДУ-305, ВДУ-504, ВДУ-505, ВДУ-601, ВСВУ-300); зварювальний пальник (табл. 2.6); пристрій для початкового порушення зварювальної дуги (ОСППЗ-ЗООмА, УПД-1, ВІР-101, ОСПЗ-2М та ін.); апаратура управління зварювальним циклом і газової захистом.
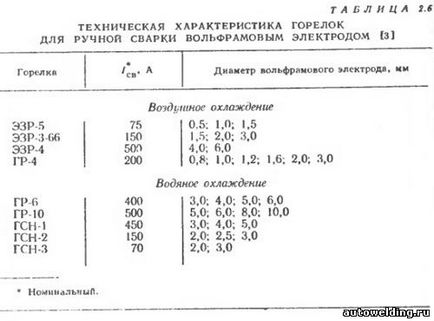
Устаткування для ручного зварювання змінним струмом, крім основних вузлів, що входять до складу обладнання постійного струму, включає в себе: пристрій для стабілізації горіння дуги (наприклад, стабілізатор-збудник дуги ВСД-01); пристрій для компенсації постійної складової зварювального струму.
До складу обладнання для автоматичного зварювання входять: зварювальний установка, зварювальний головка, пристрій для переміщення зварювальної головки і вироби, апаратура керування механізмами автомата. Універсальними автоматами тракторного типу є автомати АДСВ-6 і АДГ-506.
Автомат АДСВ-6 призначений для зварювання неплавким електродом в аргоні поздовжніх швів виробів; комплектується уніфікованої пальником АСГВ-4.
Автомат АДГ-506 призначений для зварювання прямолінійних швів у всіх просторових положеннях; комплектується випрямлячем ВДУ-506 і збудником дуги ВІС-01. Зварювальний трактор переміщається за спеціальною направляючої стрічці, що входить в комплект автомата.
Для зварювання труб випускається ряд спеціалізованих автоматів.
Техніка зварювання. Зварювання можна виконувати як з присадкою, так і без неї. Для якісного зварювання металів, особливо тонколистових, слід забезпечити точну збірку і припасування крайок, що зварюються. При автоматичному зварюванні допускаються зазори (табл. 2.7).
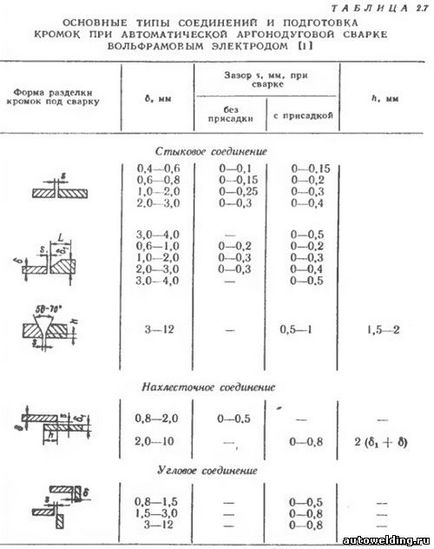
Аргонодуговую зварювання вольфрамовим електродом застосовують для стикових, кутових, з'єднань внапуск в різних просторових положеннях. Форма підготовки крайок залежить від товщини елементів, що сполучаються і можливості проводити зварювання з одного або двох сторін.
Так, наприклад, стикові з'єднання стали товщиною до 3-4 мм, а алюмінію до 5-6 мм зварюються без скосу кромок. Проплавлення кореня шва стикового з'єднання з обробленням кромок зазвичай здійснюється без присадного дроту, потім оброблення заповнюється розплавленим металом за необхідне число проходів з подачею присадного дроту.
При необхідності ведення процесу на вертикальній площині шов слід виконувати зверху вниз для товщини до 5 мм і від низу до верху для великої товщини. У цих випадках зварювання рекомендується виконувати одночасно з двох сторін. При використання такого прийому можна зварювати впритул елементи, наприклад з алюмінієвого сплаву товщиною до 16 мм.
Сварка горизонтальних стикових швів на вертикальній площині і стельових стикових швів утруднена через імовірність витікання розплавленого металу зі зварювальної ванни, тому їх слід уникати; там, де уникнути таких швів не можна, їх виконують з обробленням кромок в кілька проходів.
Для формування кореня шва можна використовувати мідні або сталеві знімні підкладки, флюсових подушку. При зварюванні активних металів необхідно не тільки отримати хороший проварена в корені шва, але і забезпечити захист від повітря зі зворотного боку розплавленого і нагрітого металу. Це досягається використанням мідних і інших підкладок з канавками, в яких подається захисний інертний газ. При зварюванні труб і закритих судин газ пропускають всередину судини.
При з'єднанні встик металу товщиною до 10 мм ручну зварку ведуть справа наліво. Присадний пруток при ручному зварюванні тонколистового матеріалу вводять не в стовп дуги, а трохи збоку зворотно-поступальними рухами. При автоматичного і напівавтоматичного зварювання електрод розташовують перпендикулярно поверхні виробу. Кут між ним і присадочной дротом (зазвичай ф 2-4 мм) повинен наближатися до 90 °. У більшості випадків присадний дріт подається в головну частину зварювальної ванни і знаходиться попереду дуги по ходу зварювання.
Виліт кінця електрода з сопла не повинен перевищувати 3 5 мм, а при зварюванні кутових швів і стикових з глибокої обробленням 5-7 мм. Довжина дуги повинна підтримуватися в межах 1,5-3 мм. Для попередження окислення вольфраму і захисту розплавленого металу в кратері після обриву дуги подачу захисного газу припиняють через 5-10 с, а включають подачу газу за 15-20 с до порушення дуги (для продувки шлангів від повітря). Порушення дуги досягається або за допомогою осцилятора, або шляхом торкання електродом вироби при зменшеному до 7-10 А струмі запалювання. У разі ручного зварювання алюмінієвих сплавів в разі відсутності осцилятора дуга повинна порушуватися на вугільній або мідній пластині.
Волченко В.Н. "Зварювання та зварювані матеріали. Том 2"