Спеціальні сплави - привіт студент!
Антифрикційними називаються сплави, службовці для виготовлення легко змінюваних труться машинних частин і сприяють зменшенню тертя і зносу деталей.
З антифрикционного сплаву виготовляють легко змінювані в міру зносу частини (вкладиші, підшипники); матеріал для цих деталей повинен володіти такими якостями, щоб при зносі їх стикається з ними важко замінна частина машини не стирається. Це можливо тільки в тому випадку, коли труться зроблені з різного матеріалу, причому матеріал найбільш цінною деталі повинен бути твердіше матеріалу, з якого зроблена легко змінюється в деталь: отже, твердість антифрикционного сплаву повинна бути нижче твердості шийки вала.
З іншого боку, антифрикційний сплав повинен також бути і досить міцним, щоб витримувати діючу на нього навантаження.
Крім того, необхідно, щоб антифрикційний сплав мав достатню пластичність, що дозволяє йому прірабативала до шийки вала, забезпечуючи таким чином рівномірний розподіл навантаження в різних точках, що труться.
Нарешті, антифрикційний матеріал повинен добре «тримати» мастило, т. Е. Утримувати тонкий шар мастила на всій площині зіткнення деталей, що труться.
Для задоволення таким різноманітним і почасти протилежним вимогам антифрикційний сплав повинен бути неоднорідним за структурою і складатися з пластичної маси з включеними в неї більш твердими зернами матеріалу.
Як типовий антифрикционного сплаву можна вказати на сплав, який має стандартну назву Б-83, структура якого складається з пластичної маси твердого розчину сурми і олова з твердими включеннями хімічних сполук SnSb (куби) і Cu3 Sn (голки) (фіг. 152).
Пластичність цього сплаву забезпечується присутністю твердого розчину, а твердість - кристалами названих вище хімічних сполук. Гарне утримання мастила на тертьових поверхнях тут досягається неоднаковою ступенем стирання поверхні сплаву; пластична маса спрацьовується швидше твердих кристалів, внаслідок чого на треться поверхні утворюються мікроканали, в яких буде утримуватися і вільно переміщатися мастильний матеріал.
Антифрикційні сплави прийнято розділяти на три основні групи: жовті, білі і чорні антифрикційні сплави; до перших відносяться бронзи, до других - бабіти, до третіх - антифрикційні чавуни.
Антифрикційні якості бронзи обумовлюються неоднаковою твердістю окремих складових її структури. Застосовувана для підшипників бронза містить олова зазвичай менше 13,9%; меншу твердість в такому матеріалі матимуть багатші міддю осі - дендрити і велику - понад оловяністие междуосние ділянки дендритів з включеними в них кристалами хімічної сполуки.
Належні якості виходять у бронзових підшипників при литві в металеві форми (швидке охолодження).
На фіг. 153 дана мікроструктура підшипникової бронзи, яка містить близько 10% олова. Бронзу застосовують в якості антифрикційного матеріалу при великих питомих навантаженнях на підшипник і найменшу кількість обертів вала, наприклад в прокатних станах.
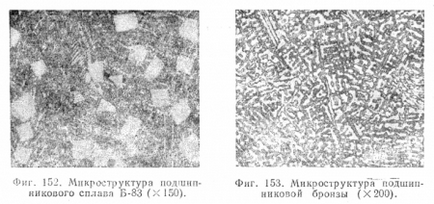
Білі антифрикційні сплави в залежності від переважаючого в їх складі металу можна розділити на бабіти з олов'яної, свинцевою, цинкової, алюмінієвої або магнієвої основою.
Бабіти на свинцевій основі за властивостями мало поступаються бабітом на олов'яної основі, але дешевше останніх; їх застосовують при середніх величинах питомого навантаження підшипника і середню кількість оборотів валу. На фіг. 154 дана мікроструктура бабіту зі свинцевою основою. Квадратні світлі кристали являють хімічна сполука SnSb, голки, зірочки - Cu3 Sn, темна частина являє евтектики свинцю і олова.
Останнім часом набули поширення бабіти зі свинцевою основою з невеликими кількостями кальцію і натрію. До них відноситься натрію-кальцієвий бабіт БК, призначений для заливки підшипників механізмів з максимальним питомим тиском до 200 кг / см 2. Структура такого баббита показана на фіг. 155
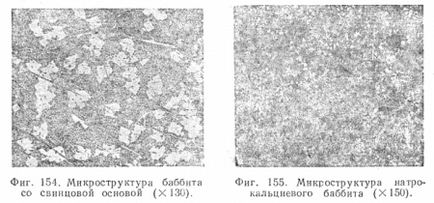
Починають також входити у вжиток як антифрикційні сплави з цинкової, алюмінієвої і магнієвої основою.
Останнім часом в якості замінників жовтих антифрикційних сплавів починають застосовувати чавуни (наприклад, ковкий чавун). З антифрикционного чавуну готують втулки і вкладиші, що працюють переважно при статичних або невеликих динамічних навантаженнях. При виборі підшипникового сплаву керуються умовами його роботи, властивостями сплаву і його вартістю.
Перші дослідні роботи в області теорії і промислового застосування антифрикційних сплавів належать проф. Анатолію Михайловичу Бочвара.
Припоями називають метали або сплави, що вживаються для з'єднання двох шматків металу.
Метал або сплав тільки в тому випадку може міцно зв'язати сполучаються шматки інших металів, якщо з кожним з них він здатний утворити сплав.
Припій вводять між сполучаються шматками металу в розплавленому стані; входячи в зіткнення з матеріалом спаюється предметів, припой розчиняє його, а при затвердінні пов'язує спаюється предмети в міцне ціле.
На фіг. 156 дана схематична картина розрізу шва, утвореного припоєм.
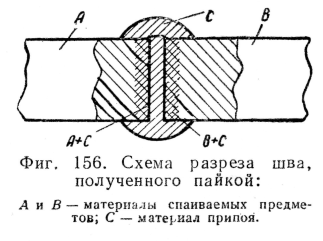
Температура плавлення припою має бути трохи нижче температури плавлення матеріалу спаюється предметів, так як в противному випадку спаюється предмети можуть бути в процесі паяння зіпсовані.
Для можливості розчинення матеріалу спаюється предметів в розплавленому припої необхідно, щоб поверхні їх були цілком чисті. Для цього спаюється поверхні перед паянням обпилюють, а також піддають хімічній чистці. Речовини, що застосовуються при паянні для очищення спаюється поверхонь від оксидів, називаються протравами. Як протрав застосовують соляну кислоту, нашатир, хлористий цинк і ін. Якщо очищає спаюється поверхні речовина не стікає, а залишається на них у вигляді тонкого шару, що оберігає поверхню від нового окислення при зіткненні з повітрям, то воно називається флюсом; в якості флюсу застосовують, наприклад, буру.
Так як температура плавлення припою для отримання хорошого спаяний повинна якомога ближче підходити до температури плавлення матеріалу спаюється предметів, залишаючись трохи нижче її, то для паяння різних матеріалів користуються різними припоями.
Залежно від температури плавлення припої поділяються на легкоплавкі і тугоплавкі, а так як зазвичай легкоплавкие припої мають порівняно малу міцність, то їх називають слабкими, а тугоплавкі - міцними.
Склад міцних латунних припоїв коливається в середньому в межах 36- 65% Сu і 35-64% Zn; температури плавлення їх знаходяться в інтервалі від 800 до 900 °. Ці припої застосовують зазвичай для споювання сплавів міді; чим більше міді в матеріалі піддається Паяні вироби, тим міцніше повинен бути припій.
Для споювання заліза і сталі хорошим припоєм є мельхіор (сплав міді та нікелю). Алюміній добре піддається пайку різними сплавами міді і олова; свинець внаслідок поганої розчинності в алюмінії непридатний для пайки останнього. До складу припоїв для споювання алюмінію вводять також і алюміній.
Як слабких припоев застосовують сплави олова та свинцю. Найбільш легкоплавкий з цих сплавів, відомий під назвою третнік, має евтектичних склад: 63% Sn і 37% Рb; температура його плавлення 182 °.
Для підвищення твердості до складу легких припоев вводять іноді невелика кількість сурми.
Додаток вісмуту до оловянносвінцовому приспіваю сильно знижує температуру плавлення останнього: так, наприклад, припой складу 15,5% Sn; 32% Рb і 52,5% Bi плавиться при 96 °; особливо легкоплавкі вісмутові припои вживаються при паянні сплавів олова і свинцю.
В описі способів отримання сплавів було сказано, що сплави можна отримувати, зокрема, пресуванням порошкоподібної суміші компонентів.
Цей метод, відомий вже більше ста років, останнім часом набув широкого розвиток під назвою порошкової металургії, а сплави, одержувані шляхом пресування, почали називати порошковими або металокерамічними, так як процес спікання металевих порошків схожий з процесом спікання керамічних мас. Причиною, що викликала розвиток застосування цього способу, є можливість виробляти пресування порошкової маси в штампах, з яких можна отримувати готовий виріб, а також можливість отримувати вироби з нерасплавляемих металів (наприклад - вольфраму) і, нарешті, створювати вироби з високою рівномірно розподіленим пористістю.
Металевий порошок можна розглядати як тіло з неповним контактом між складовими його частинками, тоді як в суцільному металі контакт має місце по всій поверхні зерен. Поверхня зіткнення частинок в порошкоподібної маси не перевищує 0,001% повної поверхні частинок. Операція отримання вироби з порошку зводиться до збільшення контакту між його частинками. Зі збільшенням контактної поверхні підвищується міцність маси, а також всі її механічні властивості. Це досягається механічним і тепловим впливом на порошкоподібну масу.
Отримання виробів методом порошкової металургії складається з наступних операцій: а) отримання металевих порошків, б) пресування суміші порошків в штампах, відповідної виготовляється виробу форми, в) нагрівання спресованої маси до температури, що лежить трохи нижче точки її плавлення, в результаті чого маса сплаву спікається .
В даний час операцію пресування іноді поєднують з спіканням, застосовуючи гаряче пресування.
Якщо до металевого порошку додають порошок з неметалічного матеріалу, то отриманий пресуванням з наступним спіканням матеріал прийнято називати металокерамічним сплавом.
Методи порошкової металургії в ряді випадків дозволяють спростити і скоротити технологічні процеси отримання виробів складної форми і точних розмірів; в деяких випадках порошкова металургія є і єдиним способом, наприклад, при виготовленні виробів з вельми тугоплавких матеріалів.
Порошкову металургію застосовують при виробництві ріжучого інструменту (пластинки з твердих сплавів), дрібних деталей машин складної форми, деталей електротехнічного і радіотехнічного обладнання, самозмащувальних пористих підшипників. При виробництві порошкових сплавів застосовують тиску до 5-10 т / см 2 і отримують усадку до 80% початкового насипного об'єму.
Спікання виробляють в відновлювальної атмосфері. При спіканні має місце подальше збільшення контактної поверхні і, як наслідок, усадка до 4% від початкового (до нагрівання) обсягу.
Залізні металокерамічні сплави можуть бути пористими, щільними і полуплотнимі (в залежності від питомої тиску пресування); спікання їх виробляється при 800-1000 °; час спікання 20-50 хв.
Ряд виробів, що піддається в роботі стирання (втулки, вкладиші для підшипників, зубчасті колеса), в даний час виготовляють з пористого залізо-керамічного матеріалу, який просочують маслом, що заповнює його пори і здійснює мастило в процесі роботи.
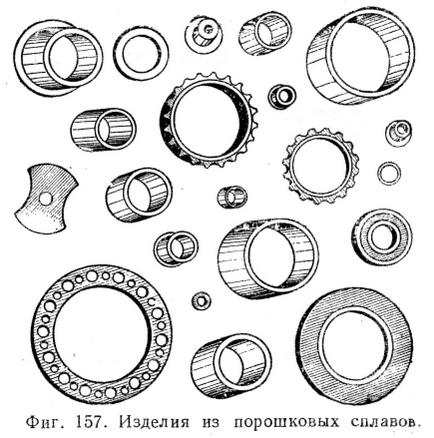
Приклад мікроструктури порошкового сплаву був наведений вище на фіг. 139; на фіг. 157 показані вироби, виготовлені з порошкових сплавів.
Завантажити реферат: У вас немає доступу до завантаження файлів з нашого сервера ЯК ТУТ скачували
Пароль на архів: privetstudent.com