Шпиндельні вузли верстатів
Шпиндельні вузли призначені для передачі обертального руху і крутного моменту від коробок швидкостей до оброблюваної деталі або інструменту. У конструкцію шпиндельного вузла входять опорні підшипники, власне шпиндель і зубчасті колеса, повідомляють йому обертання. Вали здійснюють обертальний рух і передають крутний момент шпинделям. Вали в процесі своєї роботи відчувають деформації кручення, вигину, розтягування і стиснення. Вали в залежності від конструкції можуть бути гладкі, ступінчасті, шпонкові і шліцьові. У коробках швидкостей найчастіше застосовуються шліцьові вали. Деталі, монтовані на валу, закріплюють за допомогою шпонок. Для зменшення маси і габаритних розмірів сильно навантажені вали верстатів виготовляють порожнистими. Порожні вали необхідні за умовами конструкції, щоб пропустити через них інший вал або деталь, наприклад, шпинделі токарних, фрезерних та інших верстатів. Шліцьові вали забезпечують плавне переміщення зубчастих коліс і муфт уздовж вала. Для монтажу рухомих зубчастих коліс і зубчастих блоків зазвичай застосовують шести- і четирехшліцевие вали.
Шпиндель верстата служить для передачі обертання оброблюваної деталі або інструменту. Шпинделі свердлильних, розточувальних та деяких інших верстатів крім обертального руху здійснюють одночасно поступальний рух, а шпинделі хонинговальних верстатів одночасно здійснюють зворотно-поступальний рух. Шпиндель є вельми відповідальною деталлю верстата. Від точності обертання шпинделя залежить точність обробки деталей. Основні вимоги до шпинделям верстатів наступні.
- Точність обертання, що визначається радіальним, осьовим і торцевих биттям переднього кінця шпинделя. Норми точності по ГОСТ 18097-72.
- Жорсткість, що характеризується величиною пружних деформацій шпинделя під дією сил, що виникають при обробці.
- Вібростійкою. Ця вимога пред'являється особливо до шпинделям швидкісних верстатів при виконанні оздоблювальних операцій.
- Зносостійкість тертьових опорних поверхонь при опорах ковзання і при поздовжньому переміщенні шпинделя (наприклад, на свердлильних і розточувальних верстатах).
Шпинделі виготовляють у вигляді порожніх або суцільних валів; на кінцях шпинделів закріплюються затискні пристрої, оправлення або ріжучий інструмент. Кінці шпинделів токарних верстатів з ЧПУ виконують згідно з ДСТУ 12595-72 або ГОСТ 12593-72 з циліндричним отвором, конусом Морзе і метричних конусом. Кінці шпинделів фрезерних верстатів з ЧПУ виконують згідно з ДСТУ 836-72 (конусність отвору шпинделя 7:24 за ГОСТ 2701-72). Кінці шпинделів свердлильних верстатів з ЧГ1У виконують із зовнішнім конусом Морзе по ГОСТ 9953-67, внутрішній конус Морзе з конусностью 7: 4 по ГОСТ 2701-72.
На кресленнях шпинделів крім необхідних розмірів для їх виготовлення вказуються технічні вимоги.
Виготовляють шпинделі з вуглецевої сталі 45 (загартуванню з високим відпусткою до твердості HRC = 24 ÷ 30). Поверхня шпинделя повинна володіти високою твердістю, тому застосовують сталь 40Х з загартуванням шийок струмами високої частоти до твердості HRC = 48 ÷ 60. Застосовують також інші леговані стали: хромоалюмініевие стали 40X10 і 35ХМЮА з азотуванням (при цьому досягається висока зносостійкість); марганцевисті стали 50Г2 з загартуванням і відпусткою до HRC 28-35. Для шпинделів, які працюють в підшипниках ковзання, застосовують сталь 20Х з подальшою цементацією (на глибину 0,1-1,0 мм), загартуванням і відпусткою до HRC 56-62.
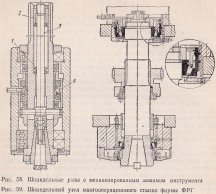
Шпиндель з механізованим затискачем інструмента наведено на рис. 58. Зажим інструмента в шпинделі здійснюється пакетом тарілчастих пружин 1 через гайку 2 і шомпол 3. З іншого кінця шомпол 3 має замок для оправок. Завівши замок шомпола в паз оправлення, повертають її на 90 ° і ставлять перемикач на пульті управління верстата в положення «затиснуті». При цьому мастильний матеріал перестає надходити в гідравлічний циліндр 4, пружини розходяться, затягуючи оправлення в шпиндель.
Нові типи шпиндельних вузлів. Працездатність шпиндельних вузлів значною мірою визначає технічний рівень і показники якості верстатів. Розвиток виробництва верстатів з ЧПУ і широке застосування інструментів з нових матеріалів істотно підвищили вимоги до шпиндельним вузлів верстатів, що викликало необхідність зміни їх конструкції. В шпиндельних вузлах використовуються підшипники нових типів з роликами. Ці шпиндельні вузли призначені для середніх і важких токарних, фрезерних, фрезерно-розточувальних і шліфувальних верстатів; їх використовують при роботі на високих швидкостях з помірною і великим навантаженням.
Представляють інтерес шпиндельні вузли, в яких попереднє натяг підшипника здійснюється гідроприводом, наприклад, багатоопераційний верстат Producent S1 Reinhard Bohll. Діапазон частот обертання на багатоопераційним верстаті становить 11,2-45 000 об / хв. Розташований на кінці шпинделя конусний роликовий підшипник (рис. 59) забезпечує високу продуктивність різання на верстаті шляхом регулювання тиску мастильного матеріалу в гідравлічній камері у всьому діапазоні частот обертання шпинделя.
Цей універсальний багатоопераційний верстат виробляє фрезерування, свердління, нарізування різьблення, розгортання, профільне фрезерування, а також обробку поверхонь за допомогою головки, обладнаної ЧПУ. Верстат відповідає сучасному рівню техніки. Нові конусні підшипники мають бічне завзяте кільце, яке переміщається в зовнішній обоймі і знаходиться в контакті з роликами. Вперте кільце навантажується в ущільненої камері системою регулювання тиску. Регулюванням тиску масла всередині гідравлічної камери досягається попереднє натяг підшипника у всіх діапазонах частот обертання і навантажень, що дає оптимальну динамічну характеристику шпинделя. Направляючий борт внутрішньої обойми забезпечує захист підшипника в разі зниження тиску до нуля.
Конусний роликовий підшипник забезпечує:
- роботу системи шпинделя з оптимальним регулюванням у всьому діапазоні частот обертання;
- підвищену статичну і динамічну жорсткість шпинделя;
- високу точність обробки круглих перетинів;
- оптимальні результати при важких режимах різання; підвищення стійкості інструменту.
Шпинделі на аеростатичних опорах. Найбільш важливими вузлами шліфувальних верстатів є шпиндельні вузли шліфувального круга і вузли шпинделів оброблюваної деталі, оскільки експлуатаційні характеристики цих вузлів (точність обертання, статична і динамічна жорсткість, нагрів, несуча здатність і довговічність) в значній мірі визначають якість шліфувального верстата в цілому. Шпиндельні вузли з такими опорами мають наступні переваги в порівнянні з шпиндельними вузлами на опорах кочення:
- високою точністю обертання внаслідок усредняющего дії газової мастила (плівки);
- відсутністю металевого контакту, а, отже, і зносу опор, що полегшує високу довговічність при незмінній якості шліфування;
- малим тертям, обумовленим невеликий динамічною в'язкістю газу (що забезпечує збільшення потужності, що передається на шліфувальний круг) і, отже, малим тепловиділенням в опорах вузла (що призводить до повного виключення часу, необхідного для розігріву шпинделя, і сприяє збільшенню продуктивності;
- майже повною відсутністю вібрацій;
- можливістю балансування круга безпосередньо на шпинделі.
Для підвищення точності обробки кілець на шліфувальних верстатах базування оброблюваної деталі виробляють на обертовому шпинделі, точність обертання якого в кілька разів перевищує точність (відхилення від круглості) деталі, яку необхідно отримати після її обробки.
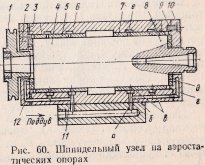
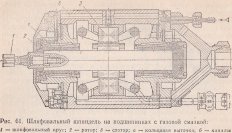
Шпиндельна головка консольно-фрезерного верстата з ЧПУ (рис. 62). Шпиндель 17 отримує обертання від шлицевого вала IV, який виступає з станини, через конічну передачу, змонтовану на підшипниках 1, 2 і 20, вал V і косозубих циліндричну передачу 4, змонтовану на підшипниках 5. шпиндель обертається в гільзі 16, що має осьовий переміщення в корпусі головки. Нижньою опорою шпинделя є дворядний роликовий підшипник 15 з конусним отвором. Верхня опора шпинделя - здвоєний радіально-завзятий підшипник 3.
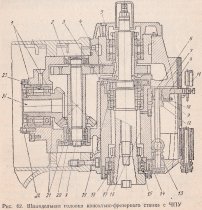
Переміщення гільзи шпинделя здійснюється вручну за допомогою знімного маховичка. Обертання передається через конічну пару ходовому гвинту 6, взаимодействующему з полугайкамі 7, кронштейном 8, який жорстко, прикріплений до гільзі 16.
При переміщенні гільзи необхідно відпустити затискний гвинт, квадратна головка якого розташована на передній стінці головки шпінделя. Для точного вимірювання величини переміщення гільзи шпиндельная головка забезпечена індикаторним пристроєм 11 і механізмом переміщення, що містить гайку 12 і зубчасту передачу 13 і 14. При монтажі і демонтажі регулювання зачеплення конічних зубчастих коліс виробляють переміщенням склянок 21. Для цього відпускають три гвинта 23 і три болта 22 . вгвинчуванням і вивінчіваніем гвинтів виробляється регулювання, затягування проводиться болтами. Бічний зазор між зубами конічної передачі повинен бути 0,17-0,24 мм. Довжина контакту не менше 50% довжини зуба, ширина - не менше 50% робочої висоти зуба.
Підшипники 3 верхньої опори шпинделя встановлюють з попереднім натягом, величина якого регулюється під шліфуванням кілець 19. Попередній натяг нижнього підшипника 15 повинен забезпечуватися посадкою підшипника на конічну шийку шпинделя шляхом подшліфованія півкілець 18. Осьовий зазор підшипників проміжного валу V повинен бути 0,02-0, 03 мм. Для вибірок зазору в парі гвинт - гайка необхідно відпустити гайку 10 і гвинт 9, потім поворотом рухомої гайки зубчастої передачі 13 усунути зазор і законтрить її. Мінімальна сила на рукоятці підйому пиноли не повинна перевищувати 40 Н.
Для збільшення продуктивності верстатів з ЧПУ такого типу на Красногорському механічному заводі успішно проведена модернізація шпиндельних головок і є досвід тривалої експлуатації верстатів, що дає хороші результати. Модернізація полягає в тому, що замість одного шпинделя в головці встановлені 12 шпинделів, які працюють одночасно за програмою, при цьому збільшені частоти обертання шпинделів в 4 рази, а сама шпиндельная головка також закріплюється в отворі станини болтами, встановленими в кільцевому Т-образному пазу. Шпинделі отримують обертання від валу V, на якому встановлено косо зубне зубчасте колесо z = 70.
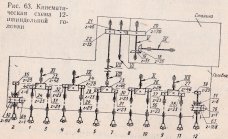
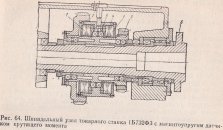
Використання компенсаційних і робочих датчиків зменшило пульсації результуючого вихідного сигналу в 5-6 разів в порівнянні з сигналами робочого датчика. При роботі верстатів з магнітокерованих датчиками в адаптивній системі управління забезпечений надійний, без поломок перехід від швидкого ходу (700-1000 мм / хв) на робочу подачу при досягненні торкання інструменту з деталлю завдяки малому значенню постійної часу вимірювання (0,002 с при частоті живлячої напругу 1000 Гц). Застосування в адаптивних системах міні-ЕОМ (система CNC) дозволяє істотно розширити алгоритми оптимального та граничного регулювання без значного збільшення витрат.
Адаптивна система управління з такими датчиками зменшує час обробки деталей в 1,5-3,2 рази.