Послуги з переробки пластмас
Отримують поліетилентерефталат поліконденсацією терефталевой кислоти (безбарвні кристали) або її диметилового ефіру з етиленгліколем (рідина) по періодичній або безперервній схемі в дві стадії За техніко-економічними показниками перевагу має безперервний процес отримання поліетилентерефталату з кислоти і етиленгліколю. Етерифікацію кислоти етиленгліколем (молярне співвідношення компонентів від 1: 1,2 до 1: 1,5) проводять при 240-270 0 С і тиску 0,1-0,2МПа. Отриману суміш біс (2-гідроксіетил) терефталату з його олигомерами піддають поліконденсації в декількох послідовно розташованих апаратах, які мають мішалки, при поступовому підвищенні температури від 270 до 300 0 С і зниженні розрядження від 6600 до 66 Па. Після завершення процесу розплав поліетилентерефталату видавлюється з апарата, прохолоджується і гранулюється або направляється на формування волокна. Матирующие агенти (TiO 2), барвники, інертні наповнювачі (каолін, тальк), антипірени, термо- і світлостабілізатори і ін. Добавки вводять під час синтезу або в отриманий розплав поліетилентерефталату. При швидкому охолодженні ПЕТФ аморфний і прозорий, при повільному - кристалічні (до 50%).
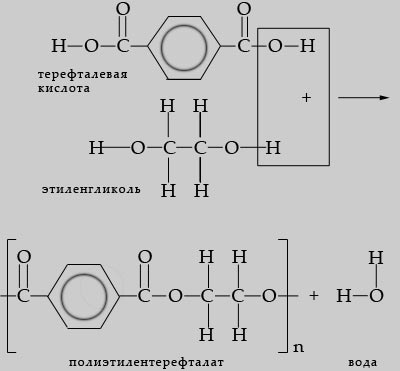
Властивості поліетилентерефталату: ММ = (20-50) * 10 3, показник плинності розплаву (230 0 С / 2,16кг, г / 10хв) 15; температура склування (температура розм'якшення) 95-100 0 С; температура плавлення 255-265 0 С; температура розкладання 350 0 С; діапазон технологічних температур 270-280 0 С; термостійкість розплаву 290 0 С; морозостійкість до -50 0 С; вологопоглинання ПЕТ - 0,3%, ПЕТ (преформа) - 0,1-0,3%; допустима залишкова волога ПЕТ - 0,02%, ПЕТ (преформа) - 0,005%; щільність 1,37 г / см 3; усадка (при виготовленні виробів) 0,2-2,0%.
Хімічні властивості: Має високу хімічну стійкість до бензину, масел, жирів, спиртів, ефіру, розбавлених кислот і лугів. Поліетилентерефталат не розчинний у воді і багатьох органічних розчинниках, розчинний лише при 40-150 0 С в фенолах і їх алкіл- і хлорзамещенних, аніліні бензиловий спирт, хлороформі, піридині, дихлоруксусной і хлорсульфоновой кислотах і ін. Нестійкий до кетонів, сильних кислот і лугів .
Має підвищену стійкість до дії водяної пари.
Фізичні властивості: аморфний поліетилентерефталат - твердий прозорий з сірувато-жовтуватим відтінком, кристалічний - твердий, непрозорий, безбарвний. Відрізняється низьким коефіцієнтом тертя (в тому числі і для марок, що містять скловолокно). Характеризується високою термостійкістю розплаву (290 0 С); деструкція на повітрі починається при температурі на 50 0 С нижче, ніж в інертному середовищі.
Експлуатаційні властивості: Експлуатаційні властивості зберігаються в діапазоні температур від -60 до 170 0 С. Має підвищену стійкість до дії водяної пари. Може покриватися автомобільним лаком. Дає відмінну блискучу поверхню.
Поліетилентерефталат переробляється литтям під тиском, екструзією, формуванням. З нього виготовляють такі вироби: великогабаритні деталі кузова автомобіля; рамка решітки радіатора; корпус приводу склоочисника; корпусні та каркасні деталі; несуча плата праски; рамка дверцята мікрохвильової печі; корпусу швейних машин; ручки електричних і газових плит; деталі двигунів, насосів, компресорів; деталі антифрикційного призначення; зубчасті колеса, ролики, ланцюги, кулачки, муфти, підшипники; ланцюга; деталі вентилів; корпусу і робочі колеса насосів; деталі електротехнічного призначення; роз'єми; прозорі вироби медичного призначення; ПЕТ-преформи (спеціальні марки).
Преформи - це заготовки для отримання пляшок і банок з полімерів методом видувного формування. Преформи виробляють методом лиття під тиском. Температура переробки 280 - 300 0 С. При таких температурах можлива термодеструкція поліетилентерефталату. Це означає, що ПЕТ втрачає свої чудові механічні властивості. Пляшка, виготовлена з зазнала деструкції ПЕТ, має жовтуватий відтінок і підвищену крихкість. Особливо це позначається при транспортуванні: при трясці у таких пляшок іноді відвалюються і лопаються денця. Значно збільшується схильність виробів до деструктивному старіння під дією кисню і ультрафіолету - гарантійні терміни зберігання скорочуються в десятки разів.
Крім того, при термодеструкції можливе виділення вельми шкідливих речовин, які мігрують в рідину, налиту в пляшку, а також отруюють робітників і близько живуть жителів при виробництві преформ. Допустимі концентрації шкідливих речовин, що виділяються при виробництві преформ, представлені в таблиці.
Допустимі концентрації шкідливих речовин, що виділяються при переробці поліетилентерефталату:
Міграція в модельні середовища в готових виробах, мг / л
1 - вихідне сопло;
2 - адсорбер;
3 - перемикачі;
4 - повітродувка;
5 - основний нагрівач;
6 - нагрівач регенератора;
7 - вихідна труба;
8 - мікрофільтр;
9 - повітроохолоджувач.
Пристрій спеціального агрегату для сушіння ПЕТ показано на малюнку. Сировина засмоктується з мішка вакуумним завантажувачем (на малюнку не показаний). Завантажувач має власне дозуючий пристрій, за допомогою якого гранули ПЕТ порційно подаються в бункер таким чином, щоб він був завжди заповнений сировиною. Сировина переміщається в бункері зверху вниз так, щоб під час перебування кожної порції в бункері було не менше чотирьох годин. Знизу в бункер через вихідне сопло подається підігріте нагрівачем повітря. Відібравши вологу від сировини, повітря через фільтр і холодильник потрапляє в адсорбер-осушувач і потім знову в бункер. Адсорберов два. Коли один працює, інший регенерується. У робочому контурі датчики безперервно вимірюють ступінь сухості повітря - точку роси. Перевищення допустимого значення точки роси є сигналом того, що робочий адсорбер пересичений, заслінки автоматично перемикаються, і роль адсорберов змінюється.
Поліетилентерефталат - кристалізується полімер. Преформу при її виробництві слід охолоджувати швидко, так, щоб ПЕТ не встиг закристалізуватися і затвердів, тобто перейшов в склоподібний стан, зберігши аморфну, некристалічні структуру, яку він має в розплавленому стані. З ростом температури в'язкість падає настільки, що полімер набуває здатності деформуватися за розумні проміжки часу. На цьому і заснований спосіб отримання пляшок з преформ - досить розігріти преформу до температури близько ста градусів, щоб за секунди з неї можна було видути пляшку.
Але в розплавленому стані величина в'язкості ПЕТ дуже низька - рухливість дуже велика і полімер може встигнути частково перейти в термодинамічно вигідніше - кристалічний стан. Візуально це видно по побілінню окремих ділянок преформи, особливо в області кінця сферичної частини, у ливника. Температура плавлення кристалів ПЕТ близько 250 0 С і при температурі виробництва пляшок кристалічні ділянки преформ деформуватися - формуватися в пляшку не можуть. Тому при виробництві преформ необхідно холодильне обладнання, яке дозволяє охолоджувати прес-форми з максимальною інтенсивністю і отримувати мінімальну величину кристалличности у виробі. Існують міжнародні стандарти, що регламентують допустиму величину ступеня кристалічності в преформ. Діаметр плями кристалличности в області ливника не повинен бути більше 6 мм.
Загальна ступінь розтягування преформи при виробництві пляшок близько десяти (добуток ступеня розтягування уздовж і поперек осі). Це означає, що будь-який дефект, який має преформа (пляма, подряпина, облой в місцях стикування формотворчих частин і т.п.), переходять на пляшку в десятикратному масштабі. Тому міжнародні стандарти строго регламентують вимоги до якості поверхні і мікродефектів преформ. Не повинно бути видимих оку включень, непроплавов, подряпин. Утворений при литті облой обламується при укладанні преформ і під дією електростатичних сил прилипає до поверхні преформи, а потім, подплавляя при видуве пляшки, спотворює поверхню виробу. Тому величина облоя повинна бути мінімальною. Для того щоб ці вимоги виконати, необхідно виготовляти прес-форми з високими розмірної точністю і якістю поверхонь.
Температура, 0 С
TC - температура сопла;
T1 - температура першої зони обігріву;
T 2 - температура другої зони обігріву;
T 3 - температура третьої зони обігріву;
T 4 - температура четвертої зони обігріву;
T ЗАГ - температура зони завантаження матеріалу;
П редварітельная сушка необхідна тільки при несприятливому збері. тривалість сушки складає 4-5 год.
Параметри процесу лиття.
Тиск уприскування: високе 1 2 00-1400 бар (100-140 бар - на манометрі термопластавтомата). З урахуванням максимального тиску упорскування на термопластавтомате - 1400 бар.
Швидкість уприскування: поверхня пресованих виробів краще при меншій швидкості уприскування.
Тиск витримки (підпресування). високе покращує якість поверхні, застосовувати 50-70% тиску лиття.
Час витримки (підпресування): рекомендується невеликий час витримки до 20% від часу охолодження.
Подушка (залишкова): 3 - 5 мм, в залежності від обсягу дозування; більше обсяг - більше подушка.
Час охолодження: має бути настільки тривалим, щоб литий виріб охололо до безпроблемного вилучення з пресформи; визначається товщиною стінок вироби, температурою стінок пресформи, температурою розплаву матеріалу.
Обороти шнека: високі, повинні бути підібрані таким чином, щоб Пластикація закінчилася мінімально завчасно охолодження.
Протитиск: 3 0- 10 0 бар (3 - 10 бар по манометру термопластавтомата).
Перевищення температури понад 290 ° С призводить до розкладання полімеру.