Піролізний котел тривалого горіння своїми руками
Технічно найбільш досконалими вважаються котли, в яких відбувається повне спалювання палива з максимально можливим поглинанням виділяється теплоти. Оскільки схеми такого роду доступні широкому колу людей - спробуємо розібратися з самостійним виготовленням піролізного котла для великих порцій палива.
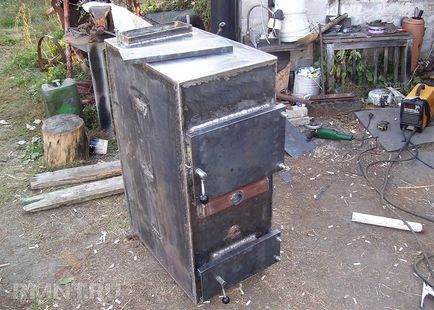
За рахунок чого можлива тривала робота
На відкритому повітрі навіть частково сирі дрова згоряють дуже швидко - буквально за 1-1,5 години. Причиною всьому вільний доступ кисню - в закритій топці котла він відсутній, за допомогою заслінки поддува дозується порція надходить кисню, і горіння відбувається менш інтенсивно.
Однією з головних проблем такого способу спалювання органічного палива виявилася його здатність «горіти» навіть без доступу кисню. При високих температурах відбувається піроліз - термічний розклад твердого палива на летючі газоподібні сполуки. Кисень для цього процесу не потрібен, достатньо розігріти ятати до 400-500 ° С. При цьому відбуваються колосальні втрати теплотворення - найбільш енергетично цінна складова вугілля або дров просто виноситься остаточний тягою в димар, не встигаючи прогорати повністю.
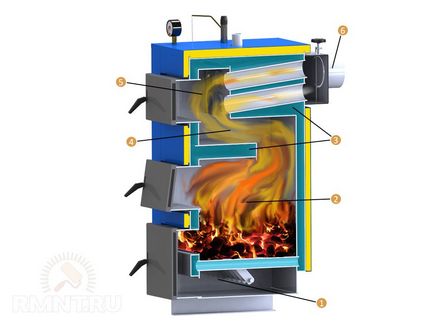
У конструкції кожного сучасного котла на твердому паливі повинна бути передбачена додаткова подача повітря для догорання виділилися газів. При цьому інтенсивність і швидкість згоряння закладки регулюється не об'ємом надходить кисню, а температурою нагріву палива. Дійсно, якщо розігріти всю закладку відразу, то горючі гази виділяться дуже швидко і про тривалій роботі котла доведеться забути. Однак якщо нагрівати тверде паливо окремими порціями, можливе поступове його розкладання в генераторної камері і ефективне повне згорання в другому відділенні топки. При цьому потік газів інвертується, вони рухаються зверху вниз під дією тяги, створеної ежекцію.
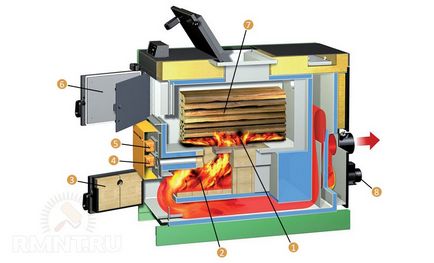
Матеріал виготовлення
Піролізні котли характеризуються підвищеною температурою робочої зони. У камері газифікації горіння не відбувається, однак зворотний потік тепла здатний розігрівати стінки до 500-600 ° С. Найбільшому температурного впливу піддається низ газогенераторного відсіку - саме ця частина контактує з займистими газами і відчуває серйозну термічну навантаження. Рекомендується низ камери закладки виконувати у вигляді чавунного колосника або спеціального вогнетривкого вироби з тонкої прорізом або поруч невеликих отворів.
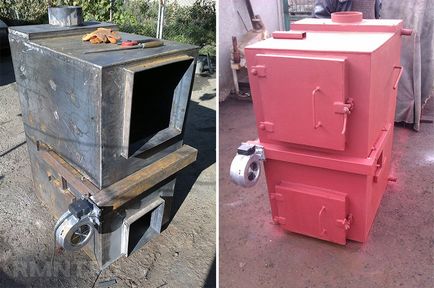
Технологія зварювання таких металів визнається помірно складною, але відтворюється в кустарних умовах із застосуванням дугового зварювання покритими електродами без захисного середовища. Основним чинником, що погіршує якість звареної конструкції, вважається освіту гарячих і холодних тріщин, обумовлене високою різницею температур на відносно малій лінійній ділянці металевого виробу.
Для усунення негативних факторів термічного впливу використовують такі технологічні прийоми:
- Нарізка деталей з плавною подачею ріжучого інструменту, ніж виключається перегрів крайок.
- Обмеження щільності зварювального струму на 20-25% в порівнянні з конструкційної сталлю, зварювання в м'яких режимах.
- Обмеження температури зварювальної ванни, виконання багатопрохідного шва з високою швидкістю без бічних коливань.
- Правильна обробка з'єднуються крайок згідно ГОСТ 5264 та їх зачистка металевою щіткою.
- Підкладка під виворіт шва металевого тепловідведення, кування шва в процесі охолодження.
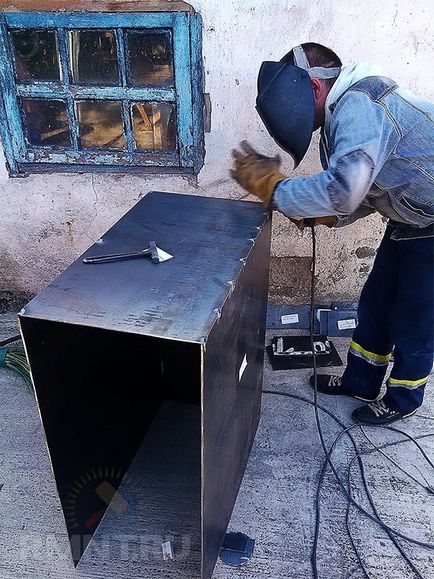
Після зварювання конструкцій рекомендується їх первинний отжиг при температурі не менше 700 ° С протягом 2,5-3 годин. Досить завантажити внутрішність звареного корпуса кам'яним вугіллям і розпалити пальне, забезпечивши слабкий примусовий піддув. Перед проведенням відпалу бажано протравити зварювальні шви спеціальною пастою, відповідної використовуваної марці стали.
Визначення розмірів і потужності
Перш ніж приступити до виготовлення піролізного котла, слід провести розрахунок розмірів камер топки і додаткових відсіків. В якості вихідних даних приймається необхідна теплотворна потужність, яка визначається з урахуванням ККД саморобного котла близько 75-80%. У домашніх умовах можна виготовити твердопаливні котли потужністю до 20-25 кВт, більш продуктивні агрегати вимагають використання жароміцних сталей значної товщини, які погано піддаються зварюванню в домашніх умовах.
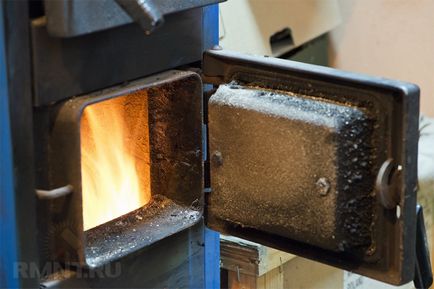
Потужність котла і тривалість його роботи визначаються об'ємом камери газифікації. Без урахування ККД теплотворність більшості поширених порід деревини становить близько 4-5 тис. Ккал / кг, що приблизно відповідає 4-4,5 кВт · год теплової потужності. Ці значення застосовні тільки для деревини з вологістю не більше 25%. Суть розрахунку проста - визначити необхідну миттєву потужність і помножити її на кількість годин роботи. Варто пам'ятати, що піролізні котли навіть досконалих конструкцій мають граничну тривалість роботи не більше доби, а самостійно вироблені агрегати слід розраховувати максимум на 12-15 годин безперервного горіння.
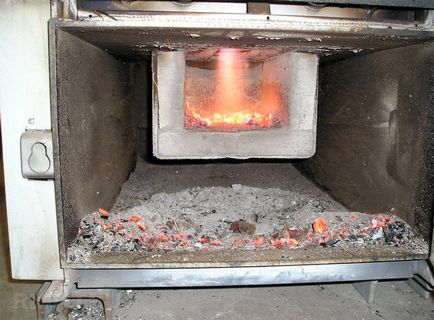
Обсяг камери закладки визначається з розрахунку 2 літри на кожен кілограм дров. До отриманого значення потрібно додати близько 30%, адже в піролізному котлі використовують неколотие чурки, які неможливо укласти впритул. Розмір камери згоряння газів повинен становити не менше 30-40% від обсягу камери газифікації. Найбільш вигідною вважається структура котла, в якій дві камери розташовані одна над іншою, мають однакову форму, але відрізняються по висоті.
Збірка двухкамерной топки
Матеріалом для виготовлення стінки камер краще вибрати гарячекатаний лист товщиною не менше 8 мм, в ідеалі - 10-12 мм. Чим товще метал, тим складніше процес зварювання, однак конструкцію з дуже тонкої сталі гарантовано поведе і викрутить в непередбачуваних напрямках. Саме тому серед деталей, з яких збирається котел, не повинно бути дрібних елементів зі співвідношенням сторін більше 2: 1.
Основа двухкамерной топки - зовнішні бічні стінки. Вони загальні для обох камер, з'єднуються за допомогою передньої стінки, в якій пророблені два прямокутні отвори для дверцят. Нижня отвір призначений для обслуговування камери згоряння, його висота повинна бути близько 120-150 мм, ширина - не менше 300 мм, розташовується отвір з відступом в 150 мм від нижнього краю. Верхній отвір призначений для завантаження камери газифікації, ніж воно буде більше - тим краще, розташовуватися отвір повинен не ближче 100 мм до верху камери. Знизу і ззаду топка замикається цільними листами, які вирізають за зовнішніми габаритами камери згоряння, але не приварюють до закінчення складання внутрішніх деталей. Зверху котел накривається листом номінального перетину.
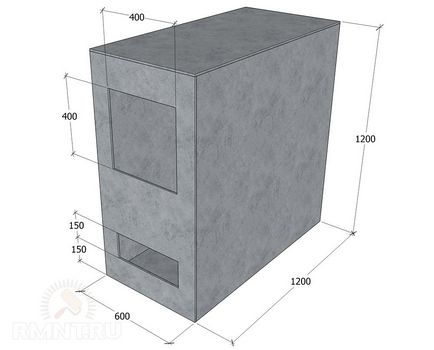
Приклад розмірів піролізного котла
Розділяти камери газифікації і згоряння буде цілісна плита, ширина якої відповідає внутрішньому відстані між стінками, а довжина - на 400 мм менше. У задній частині плити вертикально приварюється цільна перегородка, яка відділяє камеру завантаження по всій висоті, по центру уздовж горизонтальної частини вирізається отвір шириною 50 і довжиною в 400-600 мм. Зібрану Г-подібну перегородки не приварюють до завершення збирання теплообмінника.
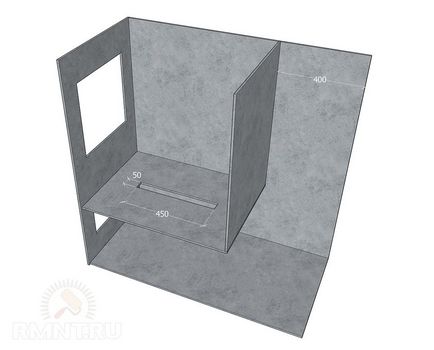
Теплообмінник для піролізного котла
Найкращою конфігурацією теплообмінника саморобного піролізного котла буде водяна сорочка нижньої камери і димоходного каналу. Це не найефективніший тип, однак виробництво власного стільникового теплообмінника викличе неминучі труднощі або з пошуком труб відповідної марки стали, або зі зварюванням різнорідних деталей.
Збірку деталей теплообмінника проводять на тому етапі, коли у котла зварені дно, передня панель і дві бічні стінки. Доступ для зварювальних робіт забезпечується з заднього боку котла. Насамперед встановлюється верхня перегородка сорочки. Це прямокутна плита з внутрішньої ширині топки і на 200 мм менше глибини камери згоряння. З боків плити потрібно видалити два прямокутних фрагмента шириною по 100 мм таким чином, щоб в передній частині плити залишилося два виступи довжиною по 200 мм. Отримана деталь приварюється до стінок і передньої панелі врівень з нижнім краєм отвору дверцята камери згоряння. При цьому вирізи в перегородці утворюють канали для циркуляції між нижньою зоною і бічними стінками теплообмінника.
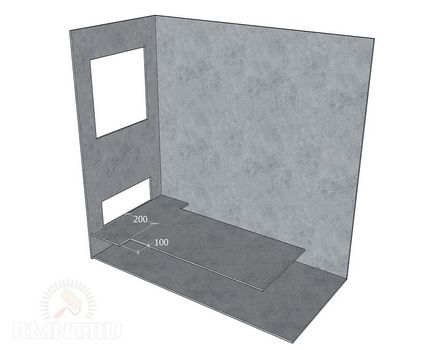
Внутрішні стінки сорочки виконуються по краю проточних каналів, мають висоту камери згоряння і примикають впритул до передньої панелі. Зверху їх накривають двома смугами шириною по 100 мм.
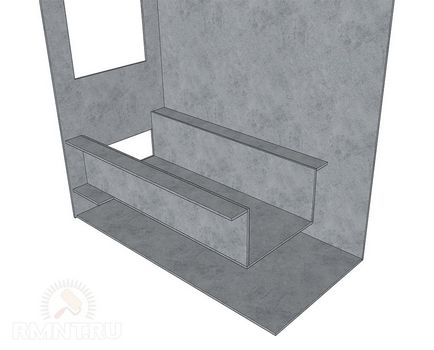
По довжині теплообмінник НЕ дістає до задньої стінки котла близько 200 мм і приблизно на таку ж відстань бічні канали виступають за Г-подібну перегородку між камерами. Коли вона буде встановлена, залишиться тільки сформувати подвійні стінки димоходного каналу, вирізати його вихідний отвір, закріпити задню стінку котла і врізати різьбові штуцери для підключення до опалювального трубопроводу. Врізка обратки виконується в одному з передніх нижніх кутів сорочки, подачу врізають в будь-який найвищій точці сорочки димоходу.
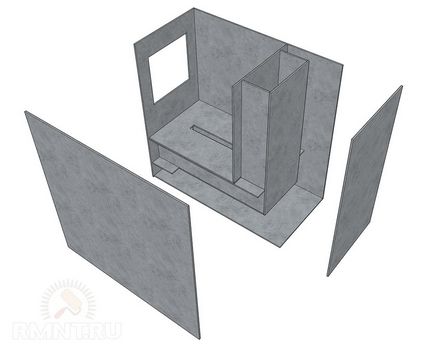
Зверніть увагу, що камера згоряння обмежена з усіх боків водяною сорочкою, крім перегородки з камерою газифікації. Це необхідно для передачі тепла, що забезпечує термічний розклад палива. При цьому прогріватися буде не вся закладка відразу, а тільки її шари, що примикають до розігрітим стінок.
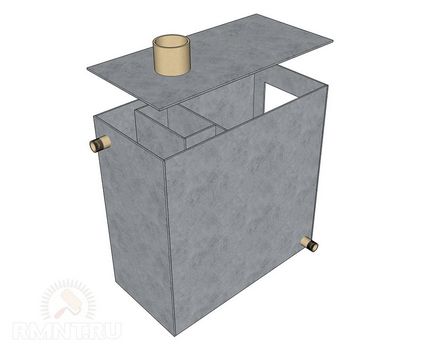
Додаткове обладнання
На жаль, піролізні котли не є незалежними. Через реверсного потоку газів потрібно примусовий наддув. Для моделей потужністю до 15 кВт він реалізується дутьевим вентилятором, який монтується на нижніх дверцятах. При цьому поповнення завантаження в процесі горіння неможливо.
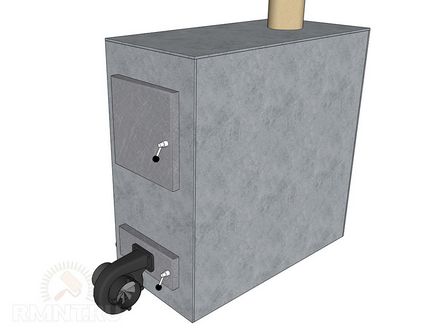
Більш потужні котли комплектуються вентилятором-димососом, який встановлюється на верхній стінці корпусу на виході димохідного каналу. При цьому виключається поява зворотної тяги і дверцята камери газифікації можна без наслідків відкривати навіть в процесі горіння.
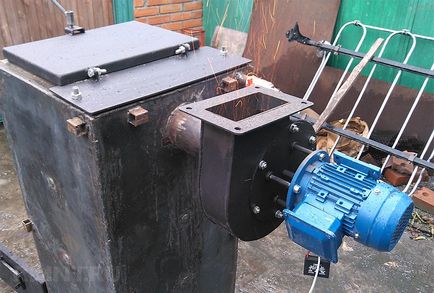
Особливу увагу потрібно приділити температурі теплоносія всередині сорочки. Після виходу котла на режим вона не повинна бути менше 60 ° С для запобігання утворенню конденсату. Це завдання вирішується шляхом установки вузла автоматичної рециркуляції, підмішують воду з подачі в обратку. Також потрібна установка групи безпеки для закритих опалювальних систем і основного циркуляційного насоса.
story: view | heating: - | 0.9938 | 58