коксохімічне виробництво
Основною сировиною для коксохімічного переділу є кам'яне вугілля, з якого отримують кокс, що служить основним видом палива в металургійних процесах. Отримані попутно з коксом продукти (газ, смоли, бензоли і т.д.) використовують як сировину для виробництва парфумерії, лаків, анілінових фарб, пластмаси, медикаментів тощо Хімічна продукція сучасних коксохімічних заводів становить близько 60% вартості коксу.
Коксування підлягають спеціальні сорти кам'яного вугілля, здатні в процесі сухої перегонки перетворюватися в тверду спечену масу.
Технологічний процес коксування включає підготовку шихти, суху перегонку (без доступу повітря) і спікання вугілля при температурах 1100-1200 0 С, уловлювання виділяються хімічних продуктів і обробку коксового пирога.
Підготовка шихти складається з прийому та складування вугілля, їх усереднення, дозування компонентів шихти, її збагачення і подальшого зневоднення. Крупнокусковой вугілля перед збагаченням попередньо подрібнюють.
Спікання шихти здійснюють в коксових печах, які представляють собою камери в формі витягнутого паралелепіпеда з габаритами по висоті, довжині, ширині до 8 × 18 × 0,65 м і вміщають понад 22 т сухої шихти. Група з 45-70 камер становить одну коксову батарею. Між камерами розташовані обігрівальні простінки, в яких рухаються продукти горіння доменного газу. Простінки у верхній частині з'єднані перехідними каналами. Повітря для спалювання газу попередньо нагрівають до 900-1100 0 С в регенераторах. На кожну камеру доводиться два регенератора, один з яких нагрівається продуктами горіння, а в іншому, раніше розігрітому регенераторі, відбувається підігрів доменного газу, що згорає в нижній частині простінка (рисунок 10.1). Через деякий час напрямок руху газів змінюється.
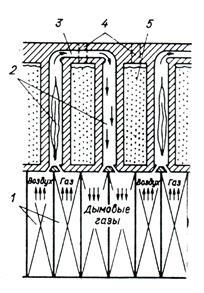
1 - регенератори; 2 - обігріваються вертикаль; 3 - обвідний канал;
4 - отвори для завантаження шихти; 5 - камера коксування
Малюнок 10.1 - Схематичний розріз коксової батареї
У камерах коксування, що працюють періодично, у міру зростання температури з шихти видаляються пари води і летючі речовини. При 350 0 С починається розкладання вугілля з виділенням смол. При 350-500 0 С шихта переходить в пластичний стан. При підвищенні температури до 1000-1100 0 С отримують кокс (спечену масу). Спікання коксівного вугілля супроводжується усадкою і появою пір. Виділяються смола і летючі речовини відсмоктуються для хімічної переробки.
Тривалість коксування становить 15-17 годин, сучасні батареї виробляють до 20 тис. Т. Коксу на добу.
Завантаження коксової камери проводиться через люки, розташовані в зведенні печі. Для видачі коксу відкривають дві протилежні дверцята, що закривають обидва кінці наскрізний коксової камери, і розпечений кокс за допомогою коксовиштовхувача видавлюється з неї.
Кокс з камери передається в гасильний вежу для мокрого (водою) або сухого (азотом) гасіння. Операція запобігає горіння розпеченого коксу. Після гасіння кокс піддається просівання, шматки класом 25-60 мм направляють в доменну плавку. Більш дрібний кокс використовують як відновник в різних металургійних процесах.
Основними хімічними продуктами коксування є коксовий газ, бензол, феноли, нафталін, кам'яновугільна смола, сульфат амонію і кам'яновугільний пек.
В екологічному відношенні коксохімічне виробництво є одним з найбільш небезпечних. На всіх його стадіях виділяється значна маса забруднювачів.
Великим джерелом токсичних речовин служать цеху коксохімічного виробництва, переробні продукти коксування: бензол, кам'яновугільну смолу і ін. На частку коксохімічного виробництва припадає понад 70% канцерогенів від їх загальної кількості, що утворюється в металургії.
Недостатністю коксівного вугілля ініціюються розробки по бескоксовой металургії, внедоменних способів виробництва заліза і його сплавів, а також заміні частини коксу в доменній плавці вугіллям і природним газом, вдувати через фурми.
На сучасному етапі розвитку промислового виробництва орієнтуються на глибоку переробку нафти, при якій отримують штучне паливо (рідке і газоподібне), мастила, нафтові бітуми і пеки, сировину для виробництва пластмаси, хімічних волокон, синтетичних каучуків, миючих засобів і т.д. Глибина переробки нафти в передових країнах досягає 90%, в нашій країні вона становить 62-64%. За обсягом споживання найбільше значення для народного господарства мають штучні рідкі палива (пальне), мастила та консистентні мастила.
Рідкі палива в залежності від їх призначення класифікуються на карбюраторні (авіаційний і автомобільний бензин) і дизельне, що відрізняється високою теплотою згоряння, що перевищує 40 тис. КДж / кг.
Карбюраторне паливо використовують у двигунах внутрішнього згоряння з запалюванням від електричної іскри.
Дизельне паливо використовують в поршневих двигунах внутрішнього згоряння із запалюванням його від стиснення при 550-600 0 С. До дизельного палива відносяться гас і соляровое масло.
Після відгону моторного палива з нафти залишається в'язка чорна рідина - мазут. Його використовують як паливо або переробляють в мастила і бензин.
Друга група нафтопродуктів (мастила) застосовується для зменшення тертя у всіх рухомих деталях і відведення від них тепла.
Третю групу нафтопродуктів - консистентні (мазеподібні) мастила - отримують додаванням до мастил загусники (масла, сульфідів, силікатів і ін.).
Видобуту нафту перед відправкою на переробку необхідно чистити від механічних домішок, води, газів, розчинених речовин, яку ведуть фізичними і хімічними методами, що включають стадію нагрівання нафти або нафтопродуктів до високих температур з поділом на фракції (суміші) або виділенням індивідуальних вуглеводнів.
Перегонка нафти (фізичний метод) заснована на різниці температур кипіння і конденсації органічних сполук, що входять до складу нафти. Перегонка полягає в поділі вихідної складної за складом рідини на окремі фракції (дистиляти).
Середні виходи різних дистилятів наведені в таблиці 10.1.
При переробці нафти вихід найбільш цінних продуктів (бензину) недостатній і зазвичай не перевищує 15%, що не може покрити всі зростаючий попит народного господарства на цей та інші види моторного палива. Збільшення їх виходу досягають застосуванням хімічних процесів переробки, різко збільшують вихід бензину (до 70% маси сировини).
Таблиця 10.1 - Виходи дистилятів при прямій перегонці нафти
Температура відбору, 0 С
При переробці із застосуванням більш високих, ніж при прямій перегонці, температур молекули органічних сполук нафти розпадаються на відносно дрібні з меншим числом атомів вуглеводні. Одночасно протікають вторинні процеси, в яких продукти розпаду утворюють молекули нових сполук, що відрізняються від вихідних будовою і складом. До вторинних відносяться процеси полімеризації (відщеплення водню від будь-якого з'єднання) і багато інших. Первинні і вторинні процеси переробки нафти і нафтопродуктів називають крекингом.
При крекінгу утворюється більше газоподібних речовин (водень, метан, бутан, пропилен, етилен і ін.), Які є сировиною для органічного синтезу.
Видобуток, переробка і транспортування нафти пов'язані з забрудненням навколишнього середовища. Потенційним його джерелом є мережа нафтопроводів. Щорічно відбувається до 700 великих розривів нафтопроводів, при цьому втрати досягають 7-20% видобутої нафти.
На загрозливому рівні знаходиться нафтове забруднення Світового океану. В даний час одна третина океанічної поверхні покрита нафтовою плівкою. Міжконтинентальна транспортування нафти, здійснювана нафтоналивними судами, становить майже половину загального обсягу морських перевезень.
Значним фактором забруднення навколишнього середовища є підприємства нафтохімічної та нафтопереробної галузей. Зона активного забруднення грунту становить 1-3 км від підприємства при загальному поширенні забруднюючих речовин, в тому числі потрапляють в сільськогосподарські культури, на відстань не менше 20 км.
Методи очищення від нафти і нафтопродуктів досить численні, проте універсального способу немає. Застосування того чи іншого методу визначається властивостями забрудненого середовища, її температурою, складом і властивостями нафти, масштабом забруднення, його розташуванням щодо населених пунктів, підприємств народного господарства і багатьма іншими факторами.