Деякі аспекти нестінг - інструмент деревообробний - компанія strike
Технологія нестінг (від англ. To nest - вкладати) - це спосіб розкрою плит (облицьованих і необлицьованих) ріжучим інструментом з отриманням деталей різних форм, розташованих на карті розкрою з максимальною щільністю.
Цей спосіб не передбачає розкрою дисковими пилами з використанням наскрізного різання і попереднього розкрою плит на прямокутні заготовки. Розкрій виконується, як правило, спеціальними кінцевими циліндричними алмазними фрезами діаметром 10 - 25 мм або профільними, наприклад, при обробці деталей меблевих фасадів. Після розкрою не потрібно доопрацювання заготовок під облицьовування або обробку.
Вперше ця технологія була застосована на домостроительном виробництві в США для вирізки отворів в готових панелях, а потім вона набула поширення як в меблевій, так і в деревообробній промисловості. Суть методу полягає у використанні обробного центру для розкрою плит повного формату на деталі різної, непрямокутної форми з подальшою обробкою кожної з них на тому ж обробному центрі до максимальної готовності елементів, з яких збирається виріб.
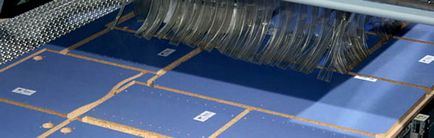
- Економія часу, що витрачається на виготовлення, за рахунок меншої кількості робочих операцій і, як результат, підвищення продуктивності, скорочення кількості обладнання і чисельності персоналу, зниження капіталовкладень і економія робочих площ;
- Скорочення тривалості виробничого циклу за рахунок виключення з нього проміжного зберігання, транспортування, навантаження-розвантаження проміжних деталей;
- Зменшення міжопераційних запасів і, як наслідок, скорочення виробничих площ, зниження шлюбу, пов'язаного з підйомно-транспортними операціями;
- Використання корисної площі заготовки (плити) по максимуму і, як наслідок, мінімізація відходів;
- Спрощення виробничого процесу і скорочення часу, що витрачається на розробку нових проектів для виробництва як серійної, так і замовний меблів за рахунок комп'ютерного проектування;
- Підвищення точності виготовлення деталей за рахунок того, що вся обробка меблевої заготовки виконується з однієї установки і на одному обладнанні.
Іншими словами, кількість виробів, серійність і оптимізація розкрою - це ті чинники, які вигідно відрізняють нестінг від традиційних технологій.
- Для виключення операції попереднього розкрою плити на дрібні заготовки, в машинному парку підприємства повинен бути обробний центр з столом, розміри якого забезпечують можливість обробки стандартної плити (як правило, 2800 х 2100 мм); в разі ручного завантаження плит і розвантаження отриманих заготовок виникають проблеми, а механізація або автоматизація цих процесів складні і вельми затратні;
- При розрахунку корисного виходу необхідно враховувати зазори між суміжними деталями, так як застосування фрез діаметром 10 - 25 мм. на відміну від пив при розкрої на круглопилковому обладнанні, веде до збільшення кількості м'яких відходів і додаткового навантаження на систему аспірації;
- Після кожної зміни профілів і розмірів заготовок доводиться міняти всмоктувальну платформу або калібрувати подкладной лист з метою надійного утримати заготовки вакуумною системою в процесі обробки;
- Після розкрою плити утворюється значна кількість дрібних кускових відходів, що підлягають видаленню зі столу верстата;
- При розкрої плит, облицьованих з двох сторін, з-за неможливості застосування підрізного пристрою доводиться використовувати дроги спеціальні інтегральні фрези і знижувати швидкість подачі, а отже, і продуктивність в разі появи дефектів (відколів) на крайках заготовок;
- Без перевстановлення заготовок на деяких моделях верстатів неможливо просвердлити всі необхідні горизонтальні отвори і вибрати гнізда, а також виконати обробку із зворотного боку;
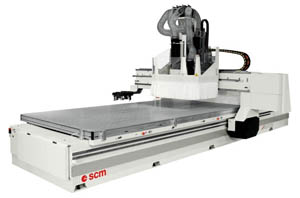
В даний час провідними виробниками освоєно випуск різного технологічного устаткування: від верстатів з матричним столом - для клієнтів з обмеженим бюджетом - до верстатів, обладнаних маятниковими столами з автоматизацією завантаження і розвантаження і спеціальними системами вакуумного кріплення різних заготовок і їх швидкої заміни.
На великих виробництвах доцільно використовувати кілька обробних центрів, встановлених на одну лінію. Завантаження заготовок може здійснюватися за допомогою автоматичного складу для плит або маніпуляторів. Оброблені заготовки транспортуються за допомогою маніпуляторів до наступного верстата, наприклад, кромкооблицювального, для подальшої обробки, а невикористані залишки матеріалу - назад на склад. Обробні центри з ЧПК, призначені для роботи за технологією нестінг, дозволяють обробляти солідні обсяги деталей, прісеем не для випуску серійної продукції, а для виконання індивідуальних замовлень.
Технологія нестінг може використовуватися і на невеликих підприємствах. Для таких фабрик, як правило, пропонується обладнання на базі обробних центрів із одним (наприклад, растрових) столом або на базі верстатів з ЧПУ для обробки як листових, так і брусків заготовок (в залежності від габаритів заготовок). Важливо, що такі обробні центри можуть використовуватися не тільки для нестінг - оброблені методом нестінг заготовки можуть, наприклад, подаватися в інший обробний центр, для свердління горизонтальних отворів. Крім того, на цих обробних центрах можна виготовляти продукцію без застосування нестінг. Завдяки жорсткій станині на них можна обробляти заготовки з масиву деревини, наприклад, деталі вікон, дверей, сходів.
З огляду на все вищесказане, технологію нестінг можна використовувати на різних видах фрезерних верстатів ЧПУ з різними робочими зонами. Все залежить від типу продукції, що виготовляється. Наприклад, якщо на підприємстві планується випускати корпусні меблі, для виготовлення якої потрібно багато криволінійної фрезерування, краще придбати верстат з робочою зоною на повний розмір аркуша. І тоді не потрібно буде купувати допоміжне обладнання.
Якщо планується виробництво корпусних меблів в основному з прямолінійними крайками, доцільно використовувати в комплекті з верстатом для нестінг форматно-розкрійний верстат - щоб зменшити кількість відходів. На деяких моделях обладнання можна встановити додаткові кріпильні засоби для заготовок максимальних розмірів, а при необхідності можна дооснастити верстати різними опціями, наприклад, пятіосевой обробними агрегатами мул пристроєм завантаження-розвантаження заготовок. Така модульна конструкція дозволяє невеликим виробництвам раціонально розпорядитися інвестиціями, закладаючи в бюджет підприємства збільшення фінанасових вкладень у міру зростання обсягу виробництва.
Для ефективного використання технології нестінг необхідно обладнати верстат вакуумним столом - для рівномірного кріплення плитного матеріалу. А також опцією автоматичної зміни інструменту - для зменшення протяжності робочого циклу.
Ще одна важлива перевага технології нестінг - економічність. Витрати на обслуговування одного верстата, що працює з високою завантаженням і виконує відразу кілька операцій, істотно нижче, ніж на обслуговування декількох верстатів, що виконують ті ж операції і той же обсяг роботи.
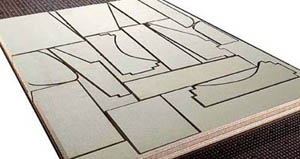
Деякі виробничники помилково вважають, що розкрій заготовок можна дуже якісно, швидко і у великих обсягах виконувати на розкрійних центрах, а верстати для нестінг тут не потрібні. Звичайно, якщо на підприємстві серійне виробництво і 90% деталей прямокутної форми, оптимальний варіант - розкрійний центр. Але якщо підприємство виконує індивідуальні замовлення, невеликими партіями, і частина деталей криволінійної форми без нестінг не обійтися.
Але перш ніж прийняти остаточне рішення, слід з'ясувати, чи є у вас все необхідне для використання цієї технології, а якщо немає, чи готові ви довести виробництво до рівня, який вимагається при використанні нестінг. Однією з неодмінних умов є автоматична обробка даних для такого верстата і наявність комп'ютерної мережі на підприємстві. Більш того, конфігурація комп'ютерної мережі повинна забезпечувати автоматичну передачу даних на ЧПУ верстата.
При розрахунку економічної ефективності технології нестінг необхідно також враховувати витрати на підкладку (плита MDF товщиною 6-8 мм. Яку потрібно періодично фрезерувати і міняти в міру зносу), що виконує функцію вакуумної присоски, і спеціальну фрезу для вирівнювання площини підкладки (вирівнювання по осі Z) .
ДЕЩО ПРО різальний інструмент
Основні відомості про інструмент можна почерпнути з різних джерел, наприклад, на сайтах виробників ріжучого інструменту для верстатів з ЧПУ. Виділимо найбільш важливі моменти, які слід враховувати при виборі.
Оптимальним з точки зору продуктивності і співвідношення «ціна-якість» є алмазний інструмент. Однак можна використовувати і твердосплавний інструмент (як напайнимі, так і зі змінними пластинками), але слід пам'ятати, що ресурс цього інструменту значно менше, ніж алмазного. Алмазним можна обробити 5-10 тис. М матеріалу, після чого можна його ув'язнити, а твердосплавний прослужить набагато менше - їм можна обробити від 500 до 1000 м. У фрез, які використовуються при технології нестінг, має бути максимальна кількість ріжучих елементів, розташованих по спіралі, що забезпечує максимальні жорсткість і продуктивність інструменту. З таким інструментом можна сміливо працювати а швидкості подачі від 15 м / хв. (Якщо дозволить встановлена потужність головного шпинделя).
Який вибирати ріжучий інструмент: стандартний або економ-класу, -решать вам. Зрозуміло, що на великих виробництвах доцільно використовувати стандартний, як найбільш економічний, а на малі виробництва - інструмент економ-класу. Але у цього правила, як і у всіх, є винятки - все залежить від індивідуальних умов і завдань конкретного виробництва. Інший обробляє інструмент, наприклад, для фрезерування пазів і свердління - звичайний (лівого або правого обертання), такий же, як і для інших верстатів з ЧПУ.
Інструмент в верстатах, що працюють за технологією нестінг, кріпиться:
- У патронах; ниболее поширені патрони HSK 63 F і ISO 30 (SK 30) на Цанги затискні, тип ER (ER 16, ER 20, ER 25, ER 32 і ER 40 (DIN 6499));
- У термозажімних патронах HSK 63 Аж
- У гідрозажімних патронах SK 30, SK 4 і патронах Weldon.
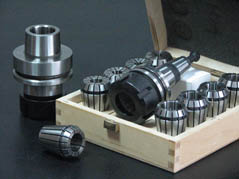
Як правило, високоточні патрони і цанги ER 16, ER 20, ER 25 застосовуються на невеликих обробних верстатах з діаметром хвостовика до 18 мм, а ER 32 і ER 40 - на великих з діаметром хвостовика до 25 мм. Наприклад, цанговий патрон HSK 63 F і цанги ER 40 з діаметром до 25 мм і термозажімние патрони (TheroGrip) застосовуються на верстатах таких фірм, як Homag, Eima, IMA, Dubus, Weeke, Biesse, SCM, Morbidelli, Masterwood. Для патрона ISO 30 застосовуються цанги ER 32 з діаметром до 20 мм. які використовуються в основному, на верстатах фірм IMA, Biesse, Reichenbacher, Weeke, Bulleri, Busellato, Stegherr. На цих верстатах можна також використовувати гідрозажімние патрони SK 30 і SK 40 і патрони Weldon.
Переваги цангових затискачів: універсальність і проста заміна цанг для хвостовиків різного діаметру; середні вимоги до допускам на розміри і шорсткість поверхні хвостовика; велика жорсткість і висока стійкість при обертанні; невисока вартість. Мінус - необхідність періодичної заміни (зазвичай не рідше одного разу на півроку).
Переваги термозажімних патронів: мінімальне биття інструмента в шпинделі і, як наслідок, можливість працювати на високих швидкостях подачі; можливість заточування різального інструменту в одному і тому ж патроні без перевстановлення; підвищення продуктивності обладнання. Недоліки: досить висока вартість; необхідність використання спеціального обладнання для заміни інструменту в патроні.
Гідрозажімние патрони SK 30 і SK 4, а також патрони Weldon мало поширені на українських підприємствах, пожтому на них остаавліваться не будемо.
Слід також звернути увагу робітників і ІТП підприємств, що використовують інструмент для нестінг, що для досягнення максимальної продуктивності цього обладнання і підвищення стійкості фрез доцільно використовувати кінцеві фрези максимального діаметра і правильно встановлювати фрези в патрон. На жаль, часто доводиться зустрічатися з тим, що при замовленні інструменту та встановлення кінцевої фрези в патрон виробничники зовсім не звертають уваги на співвідношення довжини ріжучої частини інструменту і товщини оброблюваної заготовки, забуваючи про золоте правило: довжина ріжучої частини повинна бути більше товщини заготовки на 3 - 5 мм. Менше не доцільно, так як фреза повинна забезпечити правильний викид стружки. Крім того, при установці інструменту в патрон слід максимально зменшити виступаючу частину фрези (максимально засунувши фрезу в патрон). Від виконання цієї умови залежать і величина биття шпинделя, і термін його служби, і швидкість подачі, і продуктивність обладнання, і стійкість інструменту, і, як наслідок, розмір фінансових витрат на його придбання і сервіс. Слід додати, що на фрезах діаметром понад 16 мм виробники часто завдають на хвостовик фрези знак у вигляді стилізованої літери К, який позначає оптимальну кордон установки фрези в патрон.