шнекове буріння
Шнекове буріння - це один з найстаріших способів буріння свердловин, який з часом майже не змінювався і прийшов в наші дні з самими невеликими принциповими вдосконаленнями.
Недоліком є обмеження по максимальній глибині, яку можна досягти без застосування додаткового обладнання. Однак переваги роблять шнекове буріння найпопулярнішим способом створення свердловин.
Всі, хто пов'язаний з бурінням свердловин навісними гідробур, гідно цінують швидкість виконуваних робіт, універсальність застосування обладнання, фінансову доступність і відносно не складну технологію.
Шнекове буріння застосовується найчастіше для свердловин невеликої глибини (до 20 метрів) шнеками невеликих діаметрів (до 1500мм).
Перерахуємо кілька найпопулярніших напрямків робіт, при яких застосовується шнекове буріння:
- установка дорожніх огороджень, дорожніх знаків, огорож, стовпів і опор різного призначення,
- взяття проб грунту з різної глибини,
- створення буронабивних паль,
- пересаджування дерев,
- загвинчування гвинтових паль,
- лідерних буріння для забивання паль і т.п.
Найпоширеніші методи шнекового буріння - рейсовий і потоковий.
При рейсовому способі буріння використовується шнек, який нарощується штанговими удлинителями для досягнення заданої глибини. Шнек забуривается на глибину витків, витягується з свердловини в міру наповнення витковой частини буримой породою. Порода скидається в стороні від свердловини, шнек занурюється назад за наступною порцією грунту.
Цей процес триває до досягнення необхідної глибини. Продуктивність такого методу залежить, в тому числі від довжини гвинтової частини шнека. Але тут не можна забувати про те, що, чим більше діаметр, тим важчий вантаж витягується базовою машиною зі свердловини.
Сам шнек і подовжувачі є значною металевою конструкцією, а разом з грунтом, особливо при великій глибині буріння, цей комплекс може опинитися на межі вантажопідйомності базової машини. На шнеках виробництва ТП Імпульс врахована ця особливість - кількість витків залежить від серії шнека і його діаметра, але з урахуванням максимально можливого обсягу породи, який належить цим шнеком витягти.
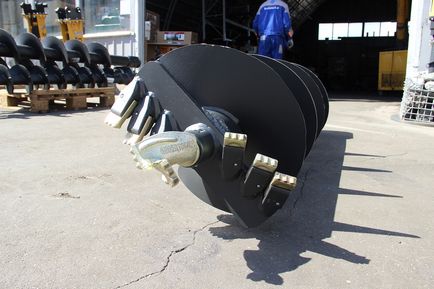
При поточному способі буріння вихід породи з вибою відбувається постійно на всій глибині буріння. Цей спосіб більш продуктивний, ніж рейсовий. При роботі потоковим способом не треба постійно витягати шнек з породою, тому що Бурим порода сама рухається по всій довжині шнека до гирла свердловини. Досягається така продуктивність тим, що реборда йде по всій довжині шнека і всіх подовжувачів. Поєднуючи шнек і подовжувачі таким чином, щоб на стику останній виток шнека переходив в перший виток подовжувача і так далі, в залежності від глибини, виходить шнековая колона, яка виробляє безперервне (потокове) транспортування Бурим грунту з забою на поверхню.
Вибір способу буріння залежить від поставленого завдання.
Повністю гвинтова шнековая колона завжди більш продуктивна, але коштує дорожче, ніж шнек з подовжувачами-штангами. Якщо буриться свердловина глибиною до 5 або 10 метрів, то рейсовий спосіб буріння буде комфортним, а якщо 10 метрів і глибше, найкращим буде потоковий метод.
Є види робіт, при яких потоковий спосіб не просто краще, але саме він і необхідний. Це ті роботи, які вимагають ідеально чіткі діаметр, вертикальність і рівність по всій глибині свердловини, наприклад, лідерних буріння для подальшої забивання паль або створення свердловин для виготовлення буронабивних паль.
Для досягнення найбільшої ефективності і якості буріння основна увага приділяється робочому інструменту - шнек.
Слово «Шнек» німецького походження і має такі значення, як равлик, завиток, спіраль.
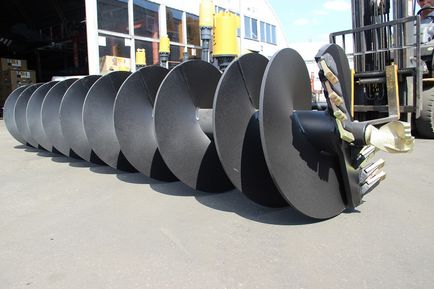
Складається шнек з підстави у вигляді стрижня, на якому, уздовж осі, закріплені спіральні витки. За своєю суттю це конвеєр, який доставляє по трубі сипучі матеріали.
Шнек бурової оснащений знизу ріжучої частиною, яка руйнує бурим породах, і приєднувальних хабом.
Транспортування матеріалу здійснюється одночасно з проходкою свердловини - це і є суть шнекового буріння.
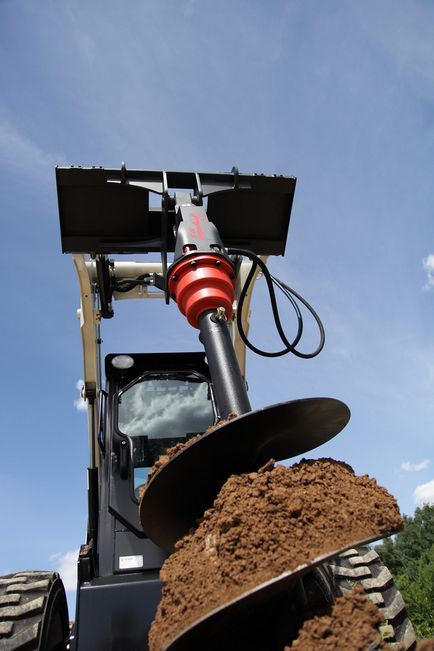
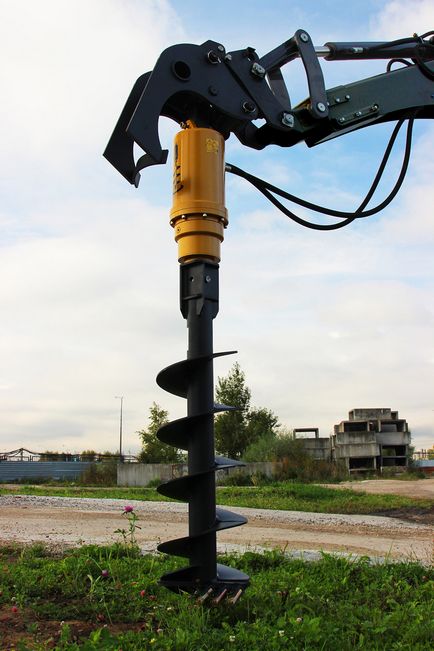
У всіх сферах діяльності людини неприпустимі відхилення в бік крайнощів.
У випадку зі шнеками це виражено в тому, що кількість зруйнованої ріжучими головками породи не повинно бути маленьким, тому що це скоротить продуктивність, і не повинно бути великим, тому що заб'є межвитковое простір і буде зупиняти просування породи по свердловині. Таким чином, шнеки виробництва ТП Імпульс виготовляються виходячи з того, що продуктивність шнекового транспортера повинна бути вище або дорівнює продуктивності ріжучої частини шнека.
Безпосередньо підйом породи по шнековому транспортеру можливий лише за умови, коли кут лінії спіралі менше значень тертя породи об поверхню реборди. Цим найважливішим деталям Технопарк Імпульс приділяє максимальне значення при проектуванні і виготовленні шнеків.
Михайло Михайлович Протодьяконов (1874-1930г.г. Життя) був великим українським, а потім і радянським вченим в галузі гірничої справи. Шкала коефіцієнта твердості гірських порід стала першим реальним способом, який оцінив гірські породи по буримости, вибуховості і зарубаемості. Ця шкала - лише один з багатьох глобальних праць професора Михайла Михайловича в гірничодобувній галузі.
Застосування по Бурим матеріалами.
Класифікація гірських порід за міцністю (шкала Протод'яконова):
Технопарк Імпульс виготовляє для Компанії Традиція-К шнеки і подовжувачі всіх типів і розмірів для обох способів буріння.
Ці шнеки призначені для використання в комплекті з відповідними моделями гідровращателей Delta. або Імпульс, або будь-який інший марки для буріння в грунті свердловин заданого діаметра на задану глибину при температурі навколишнього повітря від -40 ° С до + 40 ° С.
Шнеки, виготовлені Технопарком Імпульс, підібрати досить просто, тому що вони розбиті на серії, кожна з яких має свої обмеження по максимальному крутному моменту.
Шнеки різних серій мають свої посадочні розміри, що, в більшості випадків, дозволяє уникнути помилки при установці невідповідних шнеків на гідровращателі Delta або Імпульс.
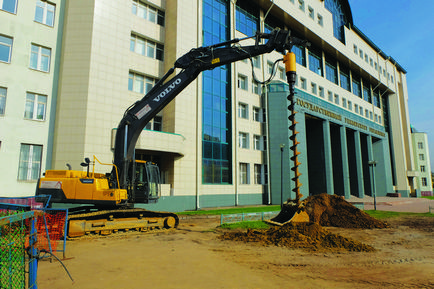
На першому етапі для підготовки до виробництва було виділено кілька мільйонний бюджет. Далі була проведена ретельна підготовка, під час якої пророблялися всі нюанси виготовлення цього, на перший погляд, не складного вироби. В процесі настройки верстатних ліній проводилося навчання робітників.
Для того що б передати свій тридцятирічний досвід з Англії приїхали робітники і конструктори Auger Torque, а так же господар компанії Алістер Райнер.
В результаті багатоденного навчання були передані всі технології та секрети виробництва шнеків Auger Torque. У процесі навчання і виробництва перших шнеків було освоєно безліч нюансів і фірмових секретів, про які навіть не здогадується кустарний виробник.
Виробляються шнеки поетапно на кількох виробничих майданчиках, що входять в єдину мережу. Метал і труби для підстав приходять на склад. Після розвантаження і сортування матеріал відразу потрапляє (ні тіні сумніву!) В виробничий процес.
Чому немає нічого скільки-небудь цікавого про етап «зберігання»?
Тому що виробництво шнеків і подовжувачів - процес безперервний, часто цілодобовий. Як тільки запущений техпроцес, починається виготовлення комплектуючих шнека. У міру виготовлення вони переміщаються на ділянку виробничої комплектації: підстава, реборди, ріжучакромка, власники зубів, самі зуби, пілот / забурнік і хаб.
Коли комплект зібраний, його переміщують на збірку, де, використовуючи редуктор, полуавтоматом зварюють комплектуючі в виріб - майже готовий шнек.
Щоб уникнути навіть мінімальних відхилень, ми використовуємо лазерний контроль під час збирання і безпосередньо перед виходом зі складального цеху.
Заготівля шнека зібрана і спрямована на дробемет, який подає дріб до 1000кг / хв. За рахунок спрямованого потоку абразиву майбутній шнек очищається від окалини. Далі проводиться чистова мехобработка і назад в дробемет для підготовки поверхні до фарбування. У малярської камері проводиться забарвлення шнека і сушка. Тепер він надійно захищений від корозії.
До того, щоб вони остаточно стало шнеком, залишилося дві операції - установка ріжучих елементів і фінальний контроль якості. Установка зубів і пілота-забурнікі - найпростіше, що відбувається в виробництві шнека, тому що установка ріжучих елементів неймовірно легка за рахунок запатентованої системи кріплення, і це дуже цінують наші замовники: заміна зношених елементів на нові проводиться «в полях» швидко без будь-яких спец. пристосувань. Повністю зібраному шнеку при проходженні через ОТК присвоюється індивідуальний серійний номер і «видається» власний паспорт, який одночасно є і інструкцією по використанню.
Все, шнек готовий і переміщений на склад готової продукції в очікуванні важкої роботи.
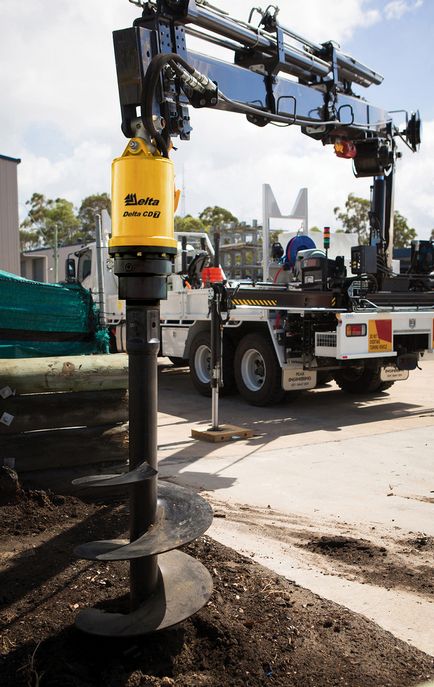
Досвід, якість, технології - шлях до успіху.
Кустарний шнек не просто зменшує продуктивність буріння або має менший ресурс. Все не так безневинно. В результаті використання невірних геометричних параметрів забурнікі на вал гідровращателя передаються як надмірна момент опору, так і руйнівні для зубчастих елементів планетарного механізму вібрації. В результаті механізм планетарного редуктора перегрівається, а зуби шестерень передчасно зношуються. Також це додаткові витрати палива екскаватора і навантаження на гідросистему.
На обивательському рівні шнек можна порівняти з победітовим свердлом. Фірмове свердло і перфоратор зажене в бетон, як в масло, за секунди. І якщо його не перегрівати, то послужить воно вірою і правдою.
А можна купити свердло на ринку дешевше. Виглядають майже однаково, але через пару отворів його можна просто викинути. Забурник перегрівся, затупився і замість сантиметрів в бетоні ви, обливаючись потом, стоїте на місці і згадуєте прислів'я «скупий платить двічі».
З неоригінальним шнеком це може бути і тричі, і гірше в разі виходу з ладу гідровращателя.