Схеми операцій точіння
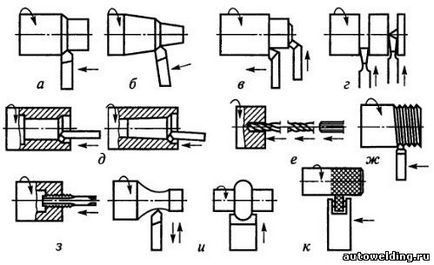
Малюнок 40.1. Схеми операцій точіння.
Основні види токарних робіт: стрілками показані напрямки переміщення інструменту і обертання заготовки (рис. 40.1):
а - обробка зовнішніх циліндричних поверхонь; б - обробка зовнішніх конічних поверхонь; в - обробка торців і уступів; г - виточування пазів і канавок, відрізки заготовки; д - обробка внутрішніх циліндричних і конічних поверхонь; е - свердління, зенкування і розгортання отворів; ж - нарізування зовнішньої різьби; з - нарізування внутрішньої різьби; і - обробка фасонних поверхонь; до - накочення рифлень
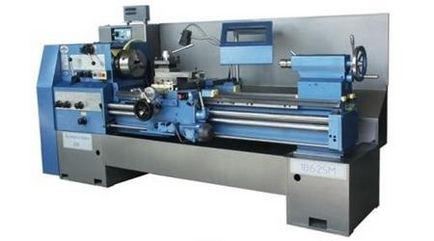
Малюнок 40.2. Верстат токарно-гвинторізний.
При роботі на токарних верстатах застосовують різні ріжучі інструменти: різці, свердла, зенкери, розгортки, мітчики, плашки, різьбонарізні головки, фасонний інструмент та ін.
Токарні різці є найбільш поширеним інструментом і застосовуються для обробки площин, циліндричних і фасонних поверхонь, нарізування різьблення і т.д. (Рис. 40.3).
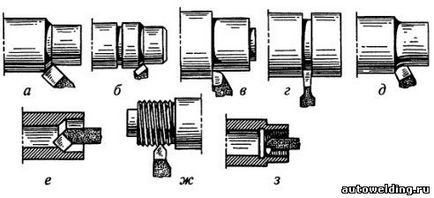
Мал. 40.3. Токарні різці для різних видів обробки:
а - зовнішнє обточування прохідним відігнутим різцем; б - зовнішнє обточування прямим прохідним різцем; в - обточування з підрізанням уступу під прямим кутом; г - прорізання канавки; д - обточування радіусної галтелі; е - розточування отвору; ж і з - нарізування різьби зовнішньої і внутрішньої відповідно
Переміщення ріжучого інструменту під час токарної обробки і його кріплення на токарно-гвинторізний верстаті забезпечують кілька вузлів (складальних одиниць). Нижче наведено короткий опис роботи деяких з них.
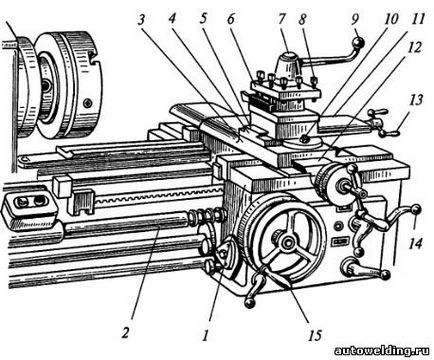
Мал. 40.4. супорт:
1 - нижні санчата (поздовжнього супорта); 2 - ходовий гвинт; 3 - поперечні санчата супорта; 4 - поворотна плита; 5 - напрямні; 6 - резцедержатель; 7 - поворотна головка резцедержателя: 8 - гвинт для кріплення різців; 9 - рукоятка повороту резцедержателя; 10 - гайка; 11 - верхні санчата (поздовжнього супорта); 12 - напрямні; 13 і 14 - рукоятки; 15 - рукоятка поздовжнього переміщення супорта
Супорт (рис. 40.4) складається з нижніх санчат (поздовжнього супорта) 7, які переміщуються по напрямних станини за допомогою рукоятки 15 і забезпечують переміщення різця вздовж заготовки. На нижніх санчатах по напрямних 12 переміщуються поперечні санчата (поперечний супорт) 3, які забезпечують переміщення різця перпендикулярно до осі обертання заготовки. По напрямних 5 поворотною плити переміщаються (за допомогою рукоятки 13) верхні санчата 11, які разом з плитою 4 можуть повертатися в горизонтальній площині щодо поперечних санчат 3 і забезпечувати переміщення різця під кутом до осі обертання заготовки. Різцетримач (він же - чотирьохпозиційна резцовая головка) кріпиться до верхніх санчат 11 за допомогою рукоятки 9 і дозволяє вводити різець в роботу з мінімальною затратою часу.
За технологічними можливостями точіння умовно поділяють на:
- чорнове точіння - видалення дефектних шарів заготовки, розрізання, відрізка і підрізування торців заготовки. Зрізається поверхнева «кірка» і основна ( »70%) частина припуску на обробку, дозволяє отримувати шорсткість 50 ... 12,5 Ra.
- напівчистове точіння - зняття 20 ... 25% припуску і дозволяє отримувати шорсткість 6,3 ... 3,2 Ra і точність 10 ... 11-го квалітету. Заготівля отримує форму, близьку до деталі.
- чистове точіння - забезпечує одержання шорсткості 3,2 ... 1,6 Ra і точність 7-9-го квалітету. Деталь отримує остаточну форму і розміри.
- тонке точіння - дозволяє при зрізанні дуже тонких стружок отримувати на поверхнях деталі шорсткість 0,40..0,20 Ra і точність 5-7-го квалітету.
Як ріжучий інструмент при точінні використовують різці. Головним принципом класифікації різців є їх технологічне призначення.
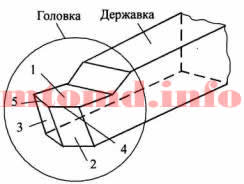
Мал. 40.5. схема різця
1 - передня поверхня; 2 - головна задня поверхня; 3 - допоміжна задня поверхня; 4 - головна ріжуча кромка; 5 - допоміжна ріжуча кромка
Розрізняють токарні різці (див. Малюнок 66):
-прохідні - для обточування зовнішніх циліндричних і конічних поверхонь;
-розточувальні - прохідні і наполегливі - для розточування глухих і наскрізних отворів;
-відрізні - для відрізування заготовок;
-різьбові - для нарізування зовнішніх і внутрішніх резьб;
-фасонні - для обробки фасонних поверхонь;
-прорізні - для протачіванія кільцевих канавок;
-галтельні - для обточування перехідних поверхонь між ступенями валів по радіусу.
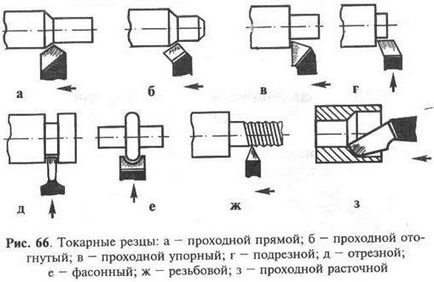
Класифікація токарних різців за характером обробки:
Класифікація токарних різців по напрямку руху подачі:
Класифікація токарних різців по конструкції:
- з привареною або припаяної пластиною;
- зі змінними пластинами.
Установка для закріплення заготовки залежить від типу верстата, виду оброблюваної поверхні, характеристики заготовки (L / D), точності обробки та інших факторів.
Свердління - основний спосіб отримання глухих і наскрізних циліндричних отворів в суцільному матеріалі заготовки. Як інструмент при свердлінні використовується свердло, що має дві головні ріжучі кромки. Для свердління використовуються свердлильні й токарні верстати.
Мал. 40.6. Вертикально-свердлильний верстат 2Н135
На свердлильних верстатах свердло здійснює обертальний (головний рух) і поздовжнє (рух подачі) уздовж осі отвору, заготовка нерухома (малюнок, позиція а).
При роботі на токарних верстатах (див. Рис. 40.7) обертальний (головний рух) здійснює обробляється деталь, а поступальний рух уздовж осі отвору (рух подачі) здійснює свердло (малюнок, позиція б).
Діаметр просвердлений отвори можна збільшити свердлом більшого діаметра. Такі операції називаються розсвердлюванням (малюнок, позиція в).
При свердлінні забезпечуються порівняно невисока точність і якість поверхні. Для отримання отворів більш високої точності і чистоти поверхні після свердління на тому ж верстаті виконуються зенкування і розгортання.
Мал. 40.7. Схеми свердління, зенкерування і розгортання
Засвердлюванням називається процес образо-вання отворів в суцільному матеріалі ріжучим інстр-рументом - свердлом. Для свердління застосовують спіраль-ні свердла різних діаметрів. Спіральне свердел про (рис. 40.8 а) складається з робочої частини і хвостового-ка, яким воно закреп-ляется в шпинделі верстата.
Робоча частина свердла складається з цилиндрич-ської і ріжучої. На ци-ліндріческой частини рас-покладені дві гвинтові канавки 4, які пред-призначаються для відводу стружки в сторону. По краях канавок знаходяться стрічки 5. Вони служать для зменшення тертя свердла об стінки отвору в деталі.
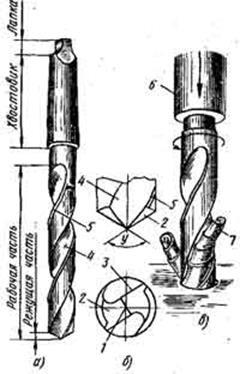
Мал. 40.8. Спіральні свердла: а - загальний вигляд, б -режущая частина свердла,
в -Свердла в процесі свердлі-ня; 1 - поперечна кромка, 2 - задня поверхня, 3 - ріжучакромка, 4 - канавка, 5 -ленточка, 6 - перехідна конусна втулка, 7 - стружка
Ріжуча частина свердла (рис. 40.8 б) складається з ко-нуса, на якому знаходять-ся дві ріжучі кромки 3, поперечна кромка 1 і задня поверхня 2. Кут заточування в залежно-сті від металу деталі мо-же коливатися в преде-лах 110-150 °.
Хвостовики бувають двох типів: конічні і циліндричні. Конічний хвостовик утримує свердло в шпинделі завдяки тре-нию, що виникає між конусом хвостовика і пере-Ходнев конусної втулкою 6 (рис. 40.8, в). Свердло із циліндричним хвостовиком зміцнюють в шпинделі верстата За допомогою кулачкового патрона. Лапка - кінцева частина свердла - служить упором при вибиванні свердла з гнізда або патрона.
При роботі свердло здійснює обертальної рух, під час кото-рого зрізається стружку металу, і поступальне переміщення, направо ленное уздовж осі обертання, при якому свердло поглиблюється в обрабат ваемого деталь.
Висока виробляй-ність і гарна якість роботи свердел можливі лише при правиль-ної їх заточування, інакше свердло при роботі буде зміщуватися з осі або його ріжуча частина буде ло-маться. Заточують свер-ла на заточувальних стайках або вручну на наждач-ном колі. Правильність заточки перевіряють шаблоном.