Пресування - студопедія
Технологія конструкційних матеріалів
МЕТОДИ ФОРМОВАНИЯ (ПЕРЕРОБКИ)
ПОЛІМЕРНИХ МАТЕРІАЛІВ У ВИРОБИ
Переробка полімерних матеріалів - комплекс процесів, забезпечують-вающий отримання виробів або напівфабрикатів із пластмас із заданими властивостями на спеціальному обладнанні. Переробці передує: 1) проектування раціональної конструкції вироби і формуючого інструмента (форми, головки); 2) вибір оптимального методу переробки; 3) розробка рецептури матеріалу, найбільш придатного для даного методу. Переробка включає приготування матеріалу і підготовку його до формування (гранули-вання, таблетування), сушку, формування виробів і їх подальшу обробку з метою поліпшення властивостей готових виробів (термічна обробка, радіаційне зшивання і ін.).
Процеси переробки найчастіше класифікуються за організаційно-технологічними ознаками, тобто виділяються підготовчі, основні, завершальні та допоміжні процеси.
До підготовчих процесів відносяться: змішання, попередній нагрів і сушка, таблетування, гранулювання і ін.
Основними процесами переробки є пресування, екструзія, лиття під тиском і ін.
До завершальним процесів відносяться механічна обробка і доробка відформованих деталей, зварювання та склеювання, фарбування та металізація виробів і ін.
Допоміжні процеси пов'язані, головним чином, з переробкою відходів, що утворюються при виготовленні виробів.
При переробці термореактивні матеріали (реактопласти) відчувають фізико-хімічні перетворення, а термопластичні матеріали (термо-пласти), в основному, тільки фізичні перетворення, пов'язані з розплавленням матеріалу і охолодженням виробів.
Пресування - це формування виробів під тиском з мате-ри-а-лов, нагрітих до вязкотекучего стану безпосередньо в порожнині формуючого інструмента (прес-формі) - між матрицею і пуансоном. Протягом короткого часу перебування в в'язкотекучий стані до матеріалу додається тиск, що діє аж до остаточного затвердіння розплаву і оформлення деталі. В результаті затвердіння утворюється сітчаста просторова структура матеріалу, і внаслідок цього виріб може бути вилучено з матриці при температурі пресування.
Пресування термопластичних матеріалів нерентабельно, тому що витяг відпресованих вироби можливо лише після охолодження його разом з формою до температури склування. Внаслідок цього знижується продуктивність і збільшуються енергетичні витрати.
Пресування здійснюється двома основними способами - прямим (компресійним) і литним (трансферним).
Пряме пресування - найбільш поширений спосіб. При цьому способі попередньо нагрітий або ненагретий, таблетований або порошкоподібний матеріал завантажують в прес-форму, яка замикається, і матеріал піддається тиску і нагрівання. Тиск передається безпосередньо на пресований матеріал аж до повного замикання прес-форми. Залежно від природи і властивостей матеріалу, що переробляється зазвичай виникає необхідність випуску з форми парів і газів, що виділяються з пресованого матеріалу в процесі реакції затвердіння. Для цього в процесі пресування виконують операцію підпресування, яка полягає в перемиканні гідропреса після певної витримки на зворотний хід, в підйомі пуансона на висоту, достатню для випуску газів (5-30 мм) і витримці його в такому положенні протягом 3-10 с. Після цього прес-форма знову замикається. При пресуванні великих товстостінних деталей з матеріалів з підвищеною вологістю подпрессовка проводять 2-3 рази.
Схема компресійного пресування представлена на рис.1, а.
У порожнину матриці розкритою прес-форми завантажують що переробляється. При замиканні прес-форми під дією зусилля преса пуансон створює тиск на пресований матеріал. Під дією цього тиску і теплоти від нагрітої прес-форми матеріал пластикується (переходить у в'язкотекучий стан), заповнює формоутворювальну порожнину прес-форми і твердіє. Після певної витримки прес-форма розкривається і за допомогою поршня з неї витягується готова деталь.
Прямим пресуванням отримують деталі середньої складності та невеликих габаритних розмірів з термореактивних матеріалів з порошкоподібною і волокнистих наповнювачем.
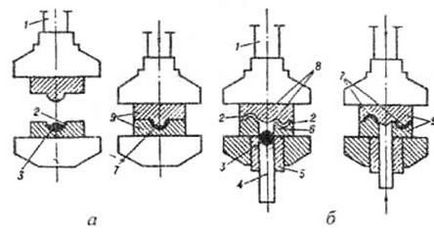
Рис.1. Схема формування виробів з реактопластів (а - компресійний пресування; б - литьевое пресування): 1 - верхній плунжер; 2 - оформляють гнізда пресформи; 3 - переробляється; 4 - поршень; 5 - трансферний циліндр; 6 - на пластину; 7 - виріб; 8 - літніковие канали; 9 - прес-форма
Недоліки компресійного пресування - поява облоя (грата) по лінії роз'єму прес-форми, необхідність підвищених зусиль пресування.
Литьевое пресування відрізняється від прямого тим, що пресований матеріал завантажують не в порожнину прес-форми, а в спеціальний обігрівається трансферний циліндр (рис.1, б). Розм'якшений матеріал впорскується матеріальним поршнем з трансферного циліндра через літніковие канали в замкнуту прес-форму. Після затвердіння матеріалу в оформляє порожнини прес-форми, її роз'єднують і витягують готові вироби.
Литьевое пресування раціонально застосовувати для виготовлення деталей складної конфігурації, з тонкими стінками, глибокими отворами, в тому числі різьбовими, до яких пред'являються підвищені вимоги по точності розмірів.
В процесі перетікання через літніковие канали матеріал прогрівається рівномірно, що забезпечує більш оптимальну структуру пресованої деталі, і знижує внутрішні напруження. При литтєвому пресуванні відпадає необхідність в подпрессовка, тому що утворюються гази можуть виходити через зазори між поршнем, циліндром і напівформах. В процесі ливарного пресування прес-форми працюють в більш сприятливих умовах, ніж при компресійному пресуванні, де вони піддаються зносу неуравновешен- ним потоком ще не розм'якшеного матеріалу.
Недоліком литтєвого пресування є підвищена витрата матеріалу, так як в завантажувальній камері і ливникових каналах залишається частина незворотного прес-матеріалу. Оскільки при литтєвому пресуванні пластицирован матеріал впорскується в замкнуту прес-форму, то по лінії роз'єму форми відсутня облой. Крім того, прес-форми для литтєвого пресування складніше по конструкції і дорожче прес-форм для прямого пресування.
Листи і плити з термореактивних матеріалів пресують пакетами на пресах. Заготовки матеріалу (з склотканини, бавовняної тканини і т.д.) просочують смолою і укладають між гарячими плитами пресів. Число укладених шарів тканини визначає товщину листів і плит. Габаритні розміри пресованих деталей обмежуються потужністю гідравлічного преса.
Методи пресування классіфіціуются також за величиною питомої тиску: пресування при високому (більше 4 МПа) і низькому (менше 4 МПа) тиску і по температурі: холодний (20 0 С), гаряче пресування (130 180 0 С для прес-матеріалів на основі фенолоформальдегідних смол), високотемпературне 200-210 0 С для тих же матеріалів).