Кускування залізорудних матеріалів
Кускування залізорудний МАТЕРІАЛІВ призначене для отримання з рудної дрібниці і концентратів збагачення міцних кускових продуктів, що володіють високими фізико-хімічними властивостями.
В даний час існує три основних способи окускования рудної дрібниці і концентратів: брикетування, агломерація і виробництво окатишів ..
Брикетування пилоподібних руд і концентратів було винайдено в 1880 році і застосовувалося спочатку, головним чином, в кольоровій металургії. Технологія брикетування включає зволоження і перемішування брікетіруемого матеріалу з невеликим (5-10%) кількістю сполучних добавок і формування брикетів на спеціальних пресах під тиском до 50-100 МПа. В якості сполучних використовуються рідке скло, сульфіт - спиртова барда, лігносульфонат, вапно і т.д. Після формування брикети для підвищення їх міцності сушать. Брикетування доцільно застосовувати при невеликих масштабах виробництва і при необхідності збереження вихідного складу шихти (наприклад, вуглецю або сірки).
агломерація
Агломерація є основним способом окускования рудної дрібниці, сурогатів руд і залізорудних концентратів. Поряд з Кускування в процесі агломерації видаляється до 95-98% сірки, що надходить з шихтою. Агломерація - процес спікання дрібнозернистих матеріалів шляхом їх нагрівання, часткового або повного розплавлення. У цих умовах реалізується термодинамічний прагнення дисперсних матеріалів до зменшення вільної поверхневої енергії. У чорній металургії найбільш поширеним є вакуумний варіант шарової агломерації (винайдений в 1906 г), в якому тепло, що забезпечує процес спікання, утворюється при горінні палива всередині спекаемого обсягу. Найпростіша установка для вакуумної шарової агломерації є чашу круглого, прямокутного або квадратного перетину, днище якої являє собою колосникові грати. Чашу встановлюють на вакуум - камеру, з'єднану з нагнітачем (ексгаустером), який в процесі спікання створює в ній розрідження (до 10-20 кПа) і, тим самим, забезпечує просмоктування через шар шихти повітря.
Як залізорудних матеріалів для агломерації використовують дрібниця залізної руди з верхньою межею крупності до 8-10 мм, залізорудні концентрати, а також відходи металургійного виробництва (прокатну окалину, шлами і пилу доменного і сталеплавильного виробництв і т.д.). Для підвищення техніко-економічних показників доменної плавки флюс, необхідний в доменній печі для зниження температури плавлення пустої породи і золи коксу, а також для отримання шлаку необхідного складу і властивостей, вводиться в піч з залізорудним агломератом. Так як порожня порода ЖРМ, в основному, кремниста, як флюс при агломерації найчастіше використовується вапняк, подрібнений до крупності 3-0 мм. Основним видом твердого палива є коксовий дріб'язок, також подрібнена до крупності 3-0 мм. До складу агломераційної шихти входить також повернення - некондиційні по крупності фракції агломерату (5 (8) - 0 мм).
Шихтові матеріали дозують в заданому розрахунковому співвідношенні, перемішують і огрудковується з додаванням води до отримання грудочок розміром 8-0 мм. Огрудкованої шихту завантажують шаром певної висоти (зазвичай від 250 до 500 мм) на колосникові грати агломераційної установки. Процес агломерації починається з зовнішнього нагріву (запалювання) шихти, який ініціює займання знаходиться в ній твердого палива. Запалювання проводиться шляхом засмоктування в шар шихти гарячих продуктів згоряння газоподібного, рідкого або твердого палива зі спеціального запального горна, встановленого над шаром. В процесі запалювання, яке зазвичай триває протягом 1-2 хвилин, поверхневий шар шихти товщиною 20 -30мм нагрівається до температури 1000 - 1200 о С. Після розігріву верху шару і запалення в ньому твердого палива процес спікання йде без зовнішнього джерела тепла за рахунок переміщення по шару теплової хвилі. Переміщення теплової хвилі забезпечується потоком повітря, просасивается через шар протягом всього періоду спікання, а підтримання необхідної максимальної температури в спекаемом шарі - теплом горіння твердого палива і окислення оксидів заліза. Необхідна кількість палива в шихті залежить від типу рудних матеріалів і параметрів процесу спікання і зазвичай становить від 3 до 6-7% її маси або 7-12% обсягу шихти.
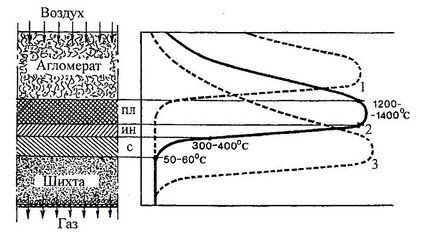
Мал. 4.6-3. Структура спікається шару і розподіл температур в шарі в послідовні моменти часу 1, 2, 3. зони: пл - плавлення; ін - інтенсивного нагріву; з - сушіння;
исокая питома поверхня частинок в обсязі шихти, незначне внутрішнє тепловий опір їх і відносно велика здається теплоємність шихти створюють досить сприятливі умови теплообміну між газом і твердим матеріалом. У зв'язку з цим процес агломерації має різко виражений зональний характер по висоті шару (рис. 4.6 -3).
Через 1-2 хвилини після завершення запалювання в спекаемом шарі утворюється п'ять характерних зон (зверху вниз у напрямку просасиванія повітря): зона охолодження агломерату, зона формування агломерату, зона інтенсивного нагріву шихти, зона сушіння, зона переувлажненной шихти. Що випаровується в зоні сушки волога може знову конденсуватися в нижележащей вихідної шихті, створюючи зону перезволоження, тільки в тому випадку, коли температура вихідної шихти нижче 50-600С. Якщо температура вихідної шихти становить 50-600С і більш, то конденсації вологи в ній і утворення зони перезволоження не відбувається. Газ із зони сушіння проходить шар вихідної підігрітою шихти НЕ перезволожуючи її.
Зону формування агломерату в свою чергу можна розділити на дві частини: зону кристалізації розплаву і зону плавлення шихти. З нижньої половиною зони формування агломерату (зоною плавлення) і, частково, з зоною інтенсивного нагріву поєднується зона горіння твердого палива. Засмоктуваний в шар повітря проходить через що утворюється зону готового агломерату, охолоджується і кристалізується розплав і, забираючи тепло продуктів спікання, нагрівається. Потрапляючи в зону горіння палива, повітря перетворюється в нагрітий агломераційний газ, що складається з продуктів горіння палива і газоподібних продуктів розкладання шихтових матеріалів. Температура газу стає вище температури матеріалу. Гарячий газ, рухаючись через шихту, що складається з відносно дрібних частинок і володіє високою питомою поверхнею, швидко віддає їй своє тепло. При цьому відбувається інтенсивне випаровування вологи з шихти (в зоні сушки) її нагрівання і займання твердого палива. Швидкість нагріву сухої шихти досягає 600-1000 0 С / хв і мало змінюється по ходу спікання.
Зони сушки, інтенсивного нагріву і горіння палива практично з однаковою швидкістю переміщаються зверху вниз до колосникових гратах, проходячи всю висоту шару за порівняно короткий проміжок часу (10-30 хв). При цьому висота зазначених зон практично не змінюється. Одночасно з зоною горіння вниз переміщається частково поєднана з нею зона плавлення, залишаючи за собою шар кристалізується розплаву і охолоджуючого аглоспека. Характерною особливістю агломераційного процесу є «концентрація» високотемпературної частини шару шихти в якій можлива поява розплаву в порівняно вузькій зоні: 20 - 60 мм. Зона плавлення представляє собою чергуються вогнища горіння частинок твердого палива (де відбувається локальна усадка розплавленого матеріалу з утворенням великих пір 5 - 15 мм) і частково розплавлені залишки шихти. Додаткову пористість дають процеси видалення гідратної вологи, СО2 карбонатів, вигоряння вуглецю палива, сірки, інтенсивний рух газових потоків через розплав.
Отриманий в складних нерівноважних умовах охолоджений продукт спікання - аглоспека - являє собою полімінеральна, полікристалічне пористе тіло, ослаблене внутрішньою напругою і тріщинами. Головною причиною збереження пористої структури агломераційного спека є структурна неоднорідність шихти, зокрема, точковий розподіл в ній частинок повернення, палива і флюсу, що перешкоджає вертикальної усадки зони формування агломерату.
Мінеральний склад залізорудного агломерату визначається складом шихтової суміші і залежить від технологічних параметрів його отримання. Основну роль у формуванні мінеральних фаз агломерату грають оксиди заліза, а також мінерали порожньої породи на основі оксидів кремнію, кальцію, магнію і алюмінію. Будь-агломерат - це полімінеральна тіло, що складається з декількох мінералів. Так як при нормальному ході процесу велика частина шихти проходить через плавлення, формування фазового складу агломерату відбувається в складних нерівноважних умовах швидкого охолодження гетерогенного розплаву.
Близько 97% всього агломерату в світі (більше 500 млн.т) проводиться на конвеєрних агломераційних машинах. Машини цього типу отримали широке поширення в багатьох країнах. В даний час в світі працює понад 1000 аглоленте сумарним подаванням понад 500 млн. Т агломерату на рік. Закордонне агломераційне виробництво початку XXIвека оснащено потужними агломашин площею спікання 400-600 м 2 на базі спікальних візки шириною 5,0 м. Продуктивність однієї такої машини досягає 20 тис.т агломерату на добу. На бразильської фірмеCST (CompanhiaSiderurgicadeTubarao) працює агломашина площею спікання 484 м 2 з найбільшою в світі шириною спікальних візки (5,5 м). Її продуктивність складає близько 6,5 млн.т агломерату на рік.
Процес спікання на конвеєрній машині (рис. 4.6 -5) є безперервним і здійснюється над вакуум-камерами її робочої гілки. Конвеєрна агломераційна машина являє собою замкнуту ланцюг рухомих спікальних візків (палет), що переміщаються по рейках верхній горизонтальній робочої гілки машини під дією зірочок 12 приводу, а по рейках нижньої похилої (2-3 °) холостий гілки машини в перевернутому положенні під дією горизонтальної складової власного ваги.
Сучасні агломераційні машини оснащуються розвантажувальними зірочками і мають горизонтальну холосту гілку. Захоплення спікальних візків з холостий гілки і транспортування їх на верхню робочу гілку машини також здійснюються за допомогою зірочок приводу. Візок сучасної машини складається з корпусу 1, комплекту колосників 2, чотирьох ходових роликів 3, бортів 4, пластин бортового ущільнення 5, пластини поздовжнього ущільнення типу «падаючий вантаж» 6 (рис. 4.6 -4).
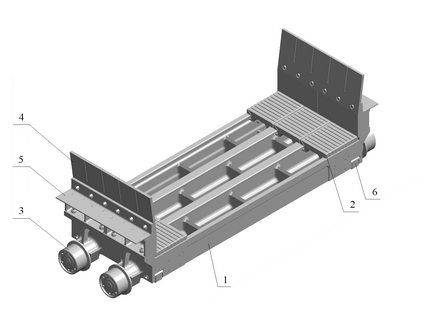
Мал. 4.6-4. Спікальних візок агломераційної машини
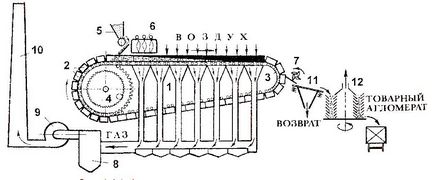
Мал. 4.6-5. Конвеєрна агломераційна машина
1 - вакуум-камери; 2 - спекательні візки; 3 - напрямні рух спікальних візків; 4 - приводний зірочка; 5-завантажувальний пристрій; 6 - запальний горн; 7 - дробарка агломерату; 8 - пиловловлювач; 9 - ексгаустер; 10 - труба; 11 - віброгуркіт; 12 - охолоджувач
На сталевій рамі кожної спікальних візки монтується три ряди колосників. Таким чином, ряд візків на машині є рухливу колосникові грати. Під час руху по робочої гілки візки проходять над вакуум-камерами, з'єднаними через збірний газопровід з ексгаустером. Спеціальне ущільнення перешкоджає прососов повітря в вакуум-камери через стик з рухомими паллетамі. Спекательні візки рухаються по робочої гілки машини одна за одною без розривів або зазорів. Просос повітря між візками в вакуум-камери виключається. Укладання захисного шару (ліжку) і шихти на рухомі візки проводиться спеціальними завантажувальними пристроями 5. Запалювання шихти здійснюють за допомогою стаціонарного газового горна 6. Під запальним гірському зона горіння твердого палива знаходиться в крайньому верхньому положенні. У міру руху палет зона горіння опускається вниз у напрямку до колосникових гратах, проходячи весь спікається шар за 10-30 хв (в залежності від висоти шару і вертикальної швидкості спікання). У той момент, коли зона горіння досягає шару ліжку, візок входить в закруглення розвантажувальної частини стрічки, утворене спеціальними криволінійними напрямними, перекидається і пиріг готового агломерату скидається в дробарку 7, потім на гуркіт 11 і в охолоджувач 12.
Продуктивність агломераційної машини прямо пропорційна площі її спікання, вертикальної швидкості спікання шихти і виходу придатного агломерату з спека:
де Q-продуктивність, т / год; Vсп - вертикальна швидкість спікання, віднесена до початкової висоти шару, мм / хв; Ш - насипна маса шихти, т / м 3; εс - вихід спека з шихти, т / т шихти; - вихід придатного агломерату,% від спека.
Вертикальної швидкістю спікання зазвичай називають середню швидкість переміщення по шару температурного максимуму теплової хвилі:
де Vсп - вертикальна швидкість спікання, мм / хв; H- висота шару шихти, мм; τ- час переміщення температурного максимуму теплової хвилі від верху шару до поверхні шару ліжку або до колосників спікальних візки, хв.
Вертикальна швидкість спікання при нормальному режимі процесу залежить від швидкості фільтрації повітря через шар і теплофізичних властивостей шихтових матеріалів:
де К - коефіцієнт, що залежить від властивостей шихти; Сг - середня питома теплоємність газу в нижній сходинці теплообміну; Сш.к - середня здається теплоємність шихти; ωг - швидкість фільтрації газу через шар. Найважливіший параметр, що визначає вертикальну швидкість спікання - швидкість фільтрації повітря через шар - визначається газопроницаемостью шихти і розрідженням під колосникових гратами машини. У загальному вигляді залежність швидкості фільтрації повітря від зазначених параметрів визначається рівнянням:
де Р - величина розрідження під шаром; -коефіцієнт гідравлічного опору шару; dекв і- середній діаметр гранул шихти і порозность шару відповідно, Г - щільність газу.
Знімання придатного агломерату з одиниці площі спікання машини називається її питомою продуктивністю (т / м 2 год). Агломерація є найпродуктивнішим способом окускования. Питома продуктивність агломашин досягає 1,5 -2,0 т / м 2 год.