Колісні пари електровозів і тепловозів
Колісна пара електровоза або вагона є найбільш відповідальним вузлом рухомого складу. Колісні пари електровозів сприймають і передають на
Колісна пара електровоза або вагона є найбільш відповідальним вузлом рухомого складу. Колісні пари електровозів сприймають і передають на рейки вертикальні навантаження від маси локомотива, при русі взаємодіють з рейкової колією, сприймаючи удари від нерівностей шляху і горизонтальні сили, через колісну пару передається крутний момент тягового дві-гатель, а в місці контакту коліс з рейками в тяговому і гальмівному режимах реалізуються сили зчеплення. Від справного стану колісної пари залежить безпека руху поїздів; тому до вибору матеріалу, технології виготовлення окремих її еле-ментів і формування колісної пари пред'являють особливі вимоги. В умовах експлуатації за колісними парами необхідний ретельний догляд і своєчасний огляд.
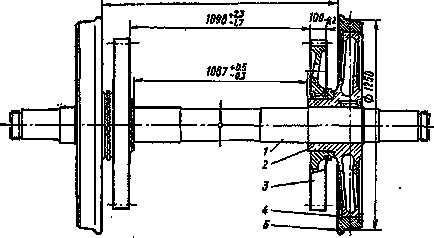
Колісна пара тепловоза і електровоза складається з осі, двох провідних і од-ного або двох зубчастих коліс. В даний час у колісних пар вітчизняних вантажних електровозів зубчасті колеса монтують на подовжених маточинах колісних центрів; раніше зубчасті колеса насаживались безпосередньо на вісь колісної пари. Метод креп-лення зубчастих коліс у пасажирських електровозів залежить від типу передачі. Конструкція колісної пари повинна забезпечувати необхідну міцність всіх її елементів і відповідати тре-бованіям ГОСТ 11018-64.
Колісні пари вантажних електровозів. Колісна пара (рис. 1) електровоза ВЛ10 складається з осі 1, двох колісних центрів 2, на ко-торие насаджені бандажі 5 до встановлених бандажними коли-цями 4 і зубчасті колеса 3.
Ось (рис. 2) виготовляють куванням з осьової стали Ос.Л ГОСТ 4728-59 з наступною нормалізацією і відпусткою, причому терми-етичні операції повинні проводитися при автоматичній регист-рації заданих режимів. У осі розрізняють наступні ділянки: буксові шийки 5, на які насаджують буксові підшипники, передпідматочинних частини 4, що представляють собою перехідні ділянки (на них кріплять лабіринтові кільця букс), подступічние частини 3, на які напресовують центри рушійних коліс, шей- кі2 під моторно-осьові підшипники тягового двигуна і середовищ-ню частину 1. Діаметри окремих, ділянок різні і переходи від однієї дільниці до іншої повинні бути плавними; їх називають перехідними галтелями. На кінцях осі є різьблення для гайок роликопідшипників, паз 6 для стопорною пластини і два отвер-сті М16 для болтів, що кріплять пластину. У торцях осі зро-лани центрові отвори для установки осі або колісної пари в верстаті.
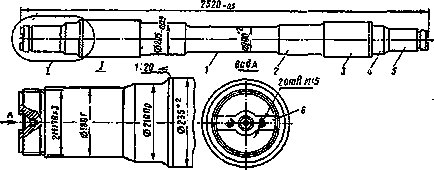
Осі рушійних колісних пар піддаються дії верти-Кальний і горизонтальних знакозмінних сил, а також скручені-ванию. Важкі умови роботи висувають особливі вимоги до матеріалу і способам обробки осі. Після обточування подступіч-ні частини і шийки осі накочуються роликами (сила натискання ролі-ка при початковій накатці 4 тс, а при кінцевій 2,5 тс) і шліфують (включаючи передпідматочинних частини). Особливу увагу приділяють виконанню і обробці перехідних галтелів, так як від цього залежать ступінь концентрації напружень і втомна міцність осі. При накатці і шліфовці усувають ризики і подряпини, біля яких зазвичай концентруються напруги, а при тривалій експлуатації можуть з'явитися тріщини.
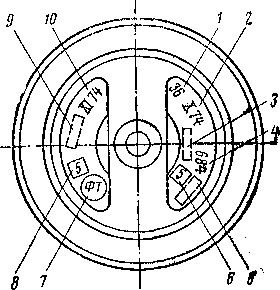
Оброблену вісь колісної пари вагону або локомотива піддають контролю ультра-звуковим і магнітним дефектоскопами, після чого на торці придатної осі ставлять клейма (рис. 3): 1 - товарний знак або номер заводу-виготовлювача необробленої осі; 2 - дата виготовлення; 3 - клейма приймання; 4 - порядковий номер осі заводу-виготовлювачем-теля необроблених осей; 5 - клейма ОТК заводу і представи-теля замовника, перевірили правильність переносу маркування і взяли оброблену вісь; 6 - умовний номер заводу, обра-бота вісь; 7 - знак формування колісної пари (ФТ - теп-овой метод; Ф - запрессовка); 8 - умовний номер заводу, фор-мировалось колісну пару; 9 - клейма ОТК заводу і предста-ставника замовника, який прийняв колісну пару; 10 - дата формиро-вання колісної кулі.
Центр 3 (рис. 4) рушійного колеса коробчатой конструкції виготовляють відливанням з вуглецевої сталі, він складається з удли-ненной маточини,
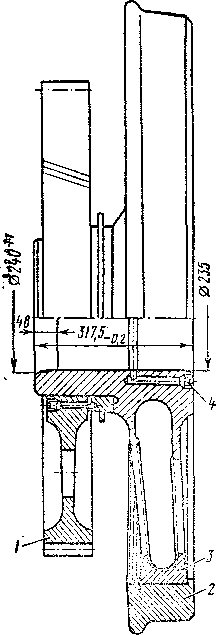
Бандаж є тією частиною колеса, яка безпосередньо взаємодіє з рейкою. На невелику контактну поверхню бандажа діють великі сили (від частки маси електровоза, сила зчеплення), бандаж сприймає динамічні навантаження, а при прослизанні піддається зносу. У зв'язку з цим матеріал бандажа повинен »володіти високою міцністю, щоб чинити опір зносу і зім'яту, і бути досить в'язким, щоб витримувати ударні нагруз.кі. У той же час бандаж повинен оброблятися на колісно-токарних верстатах, так як після досягнення встановлених норм зносу (прокату) необхідно відновлювати його профіль.
Необхідні властивості бандажная сталь отримує при введенні легуючих добавок і спеціальної термообробки. Бандажі отечест ських електровозів виготовляють зі сталі марки 60.
Основна поверхню катання бандажа має конусність 1: 20 (рис. 5), товщина нового бандажа 90 мм, товщина гребеня 33 мм на відстані 20 мм від його вершини. Ухил 1: 20 сприяє центрування колісної пари в колії і забезпечення більш рівномірного зносу поверхні кочення. Ухил 1: 7 передбачений для розміщення накату металу, що утворюється внаслідок пластичних деформацій.
Раніше випускалися електровози ВЛ8 і ВЛ23 мають банда пані діаметром 1200 мм, діаметр подступичной частини 220 мм, а зовнішній діаметр обода центру 1020 мм.
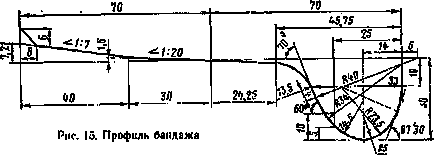
Колісні пари пасажирських електровозів ЧС2 і ЧС2 Т. Конструктивні відмінності від колісних пар вантажних електровозів обу-словлени різницею в конструкції подвешіванйя тягових двигуни-лей і тягових передач. Колісні центри 1 (рис. 6) литі спиць (12 спиць 2); до внутрішнього торця подовженою маточини 5 бол-тами кріплять маслоотражательних кільце 6, а до коническому раст-рубу 3 - вінець 4 зубчастого колеса. У маточинах колісних центрів є канали для подачі масла при расірессовке, а на посадочної поверхні діаметром 228 мм - чотири концентрично располо-женние і одна поздовжня канавки для кращого розподілу масла. Такі ж канавки є і на зовнішній поверхні удли-ненной частини стушши. Перед формуванням колісної пари кожен колісний центр піддають балансуванню. Середня частина 7 осі має діаметр 200 мм і перехід від подступичной частини (діаметр 230 мм) до середньої виконаний конічним. Гребені бандажів середніх колісних пар для кращого вписування візків в криві мають меншу товщину (23 мм).
Формування колісних пар електровозів. Згідно ГОСТ 11018-64 формування колісних пар проводять напресування або тепловим методом. Напресування зубчастих коліс на ко-лісовий центр виробляють в холодному стані з силою 50-80 тс; перед напресування посадочні поверхні протирають насухо і змащують чистим рослинним маслом, а привалочних торцеві поверхні зубчастого колеса і центру - суриком. При гарячої посадці маточину зубчастого колеса нагрівають рівномірно до температури 200-250 ° С, натяг повинен бути в межах 0,25-0,33 мм. Після гарячої посадки для перевірки міцності з'єднання до зуб-чатому колесу прикладають крутний момент 8,5 ± 0,5 тс-м; контроль положення зубчастого колеса перевіряють по загальній ризик.
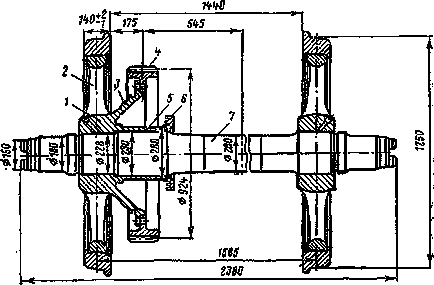
Бандаж на обід колісного центру насаджують нагрітим до тем-ператури 250-320 ° С, причому нерівномірність нагріву допускає-ся не більше 50 ° С; натяг повинен бути 1 -1,5 мм на кожні 1000 мм діаметра. Бандаж насаджують до упору бурти в торець обода ко-лісового центру, потім заводять бандажное кільце (при температурі бандажа не менше 200 ° С) і обжимають бурт бандажа на верстаті (температура бандажа повинна бути не менше 150 ° С). Щільність установки бандажа і кільця перевіряють постукуванням молотком.
Колесо в зібраному вигляді (див. Рис. 14) напресовують на вісь силою Г, рівній ПО-150 тс, натяг не повинен перевищувати 0,22 мм. Якість пресового з'єднання контролюють по діаграмі за-пресування (рис. 7); вона повинна мати односторонню опуклість вгору, допускається зниження сили До запрессовки (в кінці запресовування) до 5% на довжині / не більше 10%. Якість теплового соеди-вати контролюють на гідравлічному пресі шляхом триразового додатки осьової сили 65 ± 5 тс на кожні 100 мм діаметра під-ступичні частини осі; одночасно ведуть реєстрацію процесу.
У нових вантажних електровозів допускається різниця в диамет-рах бандажів однієї колісної пари не більше 0,5 мм і у комплекту колісних пар одного електровоза не більше 2 мм.
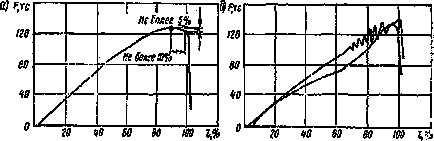
Види, терміни, порядок огляду, огляду, ремонту і формування колісних пар регламентовані Інструкцією щодо огляду, ремонту і формування колісних пар ло-локомотивів і електросекцій (ЦТ / 2306).