Барвистий апарат машин флексографічного і глибокого друку, особливості побудови, робота -
Барвистий апарат разом з формним циліндром є найважливішою складовою частиною флексографічного друкарської машини і лакувальних секцій в друкованих машинах, де лакування проводить одночасно з печаткою за один лістопрогон.
В даний час найбільший інтерес представляють два типи барвистих апаратів: дукторний (двоциліндровий), і ракельний, причому останнім часом в нових машинах частіше зустрічається ракельний тип.
Дукторного барвисті двоциліндрові апарати вперше з'явилися багато років тому, які тривалий час удосконалювалися і досі застосовуються в багатьох флексографських друкованих машинах. Вони відносно прості в обслуговуванні і наладці, мають досить гнучкі технічні можливості і недорогі. Ці барвисті апарати складаються з дукторного валика, растрированного (анилоксного) циліндра і барвистого корита.
Дукторний валик (краскопітающім, заглибні) переносить фарбу з барвистого ящика (корита) на Растеризувати циліндр. Це сталевий прогумований валик з дуже гладкою відшліфованою поверхнею.
В машинах великої ширини друку між дукторного валиком і Растеризувати циліндром виникає надмірно велика гідравлічний тиск, через що дукторний валик прогинається в середині. Тоді в процесі друкування в цій зоні передається шар фарби збільшеної товщини. Щоб цього уникнути, в деяких випадках при шліфуванні надають дукторного валика злегка бочкообразную форму.
При замовленні дукторного валиків слід повідомити постачальнику, які розчинники будуть застосовуватися в флексографських фарбах. В іншому випадку гумовий шар може розбухнути або почати руйнуватися.
Так як зараз все частіше застосовуються барвисті ракельні апарати, то можна припустити, що в майбутньому застосування дукторного валиків ще більш скоротиться.
Притиск дукторного валика до Растеризувати циліндру також має велике значення для рівномірної передачі фарби між ними. Притиск по обидва боки повинен бути однаковим і не надмірним, інакше можливий прогин циліндрів. Це вже призводить до порушення рівномірності подачі фарби на друкарську форму. Зміною міжцентрової відстані між дукторного валиком і Растеризувати циліндром можна регулювати кількість що подається на форму фарби. Це є великою гідністю барвистих апаратів даного типу. Недоліком їх є те, що при змінах швидкості роботи змінюється і кількість що подається на форму фарби, що веде до змін щільності відбитків.
Щоб цього уникнути, потрібно встановлювати в контакті з Растеризувати циліндром ракель, тоді, на форму передається тільки та фарба, яка знаходиться в осередках растрированного циліндра, а фарба з його поверхні повністю знімається.
На цій підставі в останні роки стали оснащувати дукторний барвистий апарат ще і ракельним пристроєм. Ракель притиснутий до Растеризувати циліндру зверху і під час обертання знімає з його поверхні надлишок фарби, подібно до того, як це відбувається в апаратах глибокого друку, де ракель притиснутий до поверхні формного циліндра. При цьому відбувається постійний знос поверхні растрированного циліндра, який в звичайних безракельних дукторного апаратах незначний. Проте, тривають розробки ракельних апаратів в зв'язку з підвищенням вимог до якості особливо, растрових напівтонових відбитків, і пошуки нових рішень.
Одне з них - це барвистий апарат ракельного типу. Одноциліндровий він як би доповнює ще не втратив свого значення двоциліндровий апарат дукторного типу.
Цей новий варіант побудови барвистого апарату для флексографічних друкарських машин виник недавно і за короткий час встиг поширитися повсюдно в нових машинах, призначених для високоякісного друку.
Барвистий одноциліндровий апарат складається з притиснутого до формному циліндру растрированного (анілоксового) циліндра, ракельного пристрою і барвистого корита.
Багато ракельні пристрої забезпечені механізмами осьового зворотно-поступального переміщення ракеля для видалення потрапляють на нього забруднень і сторонніх часток в фарбі. Спочатку в Європі була прийнята тільки «попутна», або позитивна, установка ракепя, а в США робили і пристрої із зустрічною, або негативної, установкою ракеля.
Майже всі флексографские машини, призначені для високоякісної растрової друку, оснащуються зараз барвистими ракельними апаратами. Ці апарати забезпечують нанесення тонкого, рівномірного і чітко визначеного по товщині шару фарби по всій довжині утворює форми при всіх швидкостях роботи машини. Дуже важливо точно притиснути ракель до циліндра з мінімально необхідним зусиллям, так як інакше відбувається посилене зношування поверхні растрированного циліндра.
Барвистий ракельний апарат має і деякі слабкі сторони. Крім підвищеного зносу поверхні растрированного циліндра до недоліків можна віднести і певна залежність товщини шару фарби, що наноситься на форму, від частоти растру на циліндрі. Тому доводиться застосовувати різні растрірованние циліндри з різною линиатурой при друкуванні зображень різного роду: тексту, плашок або напівтонових растрових ілюстрацій, тобто змінювати растрірованние циліндри при зміні характеру зображення. Це вимагає збільшення капіталовкладень - потрібні змінні растрірованние циліндри - і збільшення витрат часу на переналагодження машини при переході на друкування нового тиражу.
Однак, дуже сильна сторона барвистих ракельних апаратів це точна подача тонкого шару фарби на форму для отримання хорошого і стабільної якості флексографських відбитків. Стабільна подача особливо тонкого шару фарби на форму під силу тільки ракельним апаратів.
На основі позитивних результатів, отриманих при роботі із зустрічним ракелем, були розроблені і встановлені на багатьох флексографських друкованих машинах в тій чи іншій мірі закриті щілинні барвисті камери, зроблені з алюмінію, оснащені встановленим на виході з камери негативним ракелем.
Перевагами такої камери є рівномірна подача фарби по всій ширині під невеликим тиском, незначна циркуляція фарби, мінімальне випаровування розчинників завдяки використанню закритої системи, щадні умови роботи для растрированного циліндра завдяки спеціальному пристрою підвіски всієї камери і можливість простого і швидкого змивання апарату при зміні фарби.
Запатентована конструкція барвистою системи з камерним ракелем lnkJector. Вона складається з двох камер, розділених маленької вузької перегородкою. Обидві камери з'єднуються за допомогою невеликої щілини (менше 4 мм), яка розташована в верхній частині перегородки. Фарба або лак накачується в першу «подає» камеру під низьким тиском. Низький тиск рідини і обертання анілоксового вала сприяють надходженню фарби або лаку до входу в щілину з однаковою лінійною швидкістю по всій утворює анілоксового циліндра. Перебіг фарби в щілини супроводжується високим місцевим гідравлічним тиском, створюваним в зазорі.
Коли осередки анілоксового вала проходять подає камеру, вони на 80% наповнені повітрям. Під впливом сил, що виникають в зазорі, фарба або лак затікає на дно осередків, витісняючи з них повітря разом зі старою фарбою або лаком. Витісняється повітря з другої «випускний» камери виводиться разом з надлишками фарби. Дві сили впливають на процес, що відбувається всередині осередків. Перша сила, згадувана раніше локальне високий гідравлічний тиск. Але тиск саме по собі, незважаючи на його високе значення, діє лише на поверхню фарби в осередку, не впливаючи на її внутрішні шари у поверхні анілоксового циліндра. Друга сила - перепад тиску - є причиною виникнення вихрового потоку всередині осередків. При цьому повітря і відпрацьовані рідини не затримуються на дні комірки. Як тільки повітря і надлишки фарби проходять через зазор в випускну камеру, тиск знову падає.
Система lnkJector дозволяє рівномірно подавати фарбу по всій ширині друкованого поля і отримувати підвищену оптичну щільність, однакову по всьому відбитку. Оскільки кількість переданої фарби зменшено, менше часу потрібно для сушки. А це в свою чергу веде до збільшення швидкості друку і продуктивності. Результат друку більш передбачуваний, що особливо важливо при повторному друці замовлення.
lnkJector усуває такі проблеми, як тенение, вспенивание фарби і її витік. Завдяки високій стабільності система допускає мінімальний натиск між формним і друкованим циліндрами і анілоксовими циліндром.
При зупинках машини формовий циліндр повинен відводитися від друкованого циліндра, щоб не відбувалося прилипання запечатуваної стрічка до поверхні друкарської форми. Це проводиться шляхом невеликого підйому формового циліндра по вертикалі або невеликого його зміщення по горизонтальному напрямку. Одночасно формовий циліндр потрібно зупинити і відвести від барвистого апарату, щоб на формі не накопичувалася фарба.
Формовий циліндр при вимкненому натиску повинен зупинятися для змивки форми і, при необхідності, внесення невеликої коректури. Валики і циліндри барвистого апарату повинні в цей час обертатися, щоб фарба не засихала на їх поверхнях.
Від растрової флексографічного друку з програмним управлінням залишається один невеликий крок до модифікованої, а саме, глибокої непрямий (непрямої) печатки. Знайдена можливість друкувати цим способом на флексографічних машинах, встановлюючи там формні циліндри глибокого друку. Якість відбитків, які утворюються при цьому, близько до якості відбитків глибокого друку.
Цей спеціальний спосіб друку може застосовуватися для друкування на шорсткуватих поверхнях і на розтягуються матеріалах, які не можна запечатувати в звичайних машинах глибокого друку. За таким принципом можуть будуватися і планетарні машини. Замість звичайного формового циліндра в цьому випадку до друкованого циліндра притискається циліндр з гумовотканинної обтягуванням або прогумований валик такого ж діаметру, що і формовий циліндр глибокого друку.
Це означає, що для кожного формового циліндра певного діаметру повинен бути прогумований валик того ж діаметру, який встановлюється на тому місці, де в звичайній флексографічного машині встановлюється формовий циліндр. На місці растрированного циліндра встановлюється формовий циліндр глибокого друку, а на місці дукторного валика встановлюється ракельне пристрій, відрегульоване для певної подачі фарби. Всі інші елементи і пристрої друкарської секції залишаються тими ж, що і при флексографічного друку.
З точки зору техніки цей спосіб пресі не зустрічає значних труднощів, хоча й виникають проблеми з фарбами і гумовими обтяжку. Слід пам'ятати, що фарба при передачі від формового циліндра не повинна засихати на проміжному циліндрі, але після передачі на запечатується материал повинна закріплюватися в дуже короткий проміжок часу, до накладення наступної фарби. Це обмежує продуктивність машини даного типу. Швидкість друку на них, в залежності від типу проміжного сушильного пристрою не перевищує 150 м / хв.
Цей спосіб в останні роки втрачає своє значення, так як з'явилася можливість друкувати на розтягуються матеріалах при дотриманні хорошої якості приведення на звичайних машинах глибокого друку. Якість флексографічного растрового друку за ці роки значно покращився завдяки тривало вдосконалення друкарських машин і використання фотополімерних формних пластин. Ця конкуренція призводить до сильного зближення можливостей двох способів друку, що може привести до потужного імпульсу розвитку глибокого друку, яка недостігаема для інших способів друку за критерієм якості друку напівтонових зображень.
Це дуже важливий елемент флексографічного друкарської машини. Циліндр повинен бути дуже жорстким на вигин, мати найбільший можливий діаметр і високу радіальну точність близько 0,01 мм.
Для нанесення ячеистой растрової сітки на поверхню растрированного циліндра існують різні способи:
1. Накатка, при якій на поверхні циліндра одночасно развальцовивается безліч осередків.
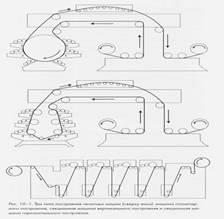
3. Травлення (фотохімічний спосіб, який застосовується для виготовлення формних циліндрів глибокого друку).
4. Електронне гравірування на геліоклішографе, при якому штихель вибирає обсяг осередків.
5. Лазерне гравірування керамічного шару (наприклад, оксиду хрому), при якому матеріал з осередків випаровується.
Растрові осередки найчастіше робляться у вигляді пірамід з гострою вершиною або у вигляді усічених пірамід. Осередки зазвичай утворюються безпосередньо на поверхні сталевої труби або, при тонких (високолініатурних) растрах, в шарі міді, що покриває сталеву поверхню.
Дуже важливо, щоб при покупці нової машини були чітко сформульовані вимоги до растру, інакше неможливо буде отримати потрібну товщину шару фарби, так як Растеризувати циліндр може передавати її в залежності від параметрів осередку більше або менше, ніж потрібно.
Для підвищення тиражестойкости Растеризувати циліндрів вже багато років ведеться робота з визначення найкращого, найбільш твердого типу їх поверхні.
Часто це завдання вирішується шляхом спеціального хромування, або подвійного хромування, яке значно збільшує зносостійкість поверхні.
Інший шлях - нанесення керамічного покриття. Поверхня виходила досить твердою і одночасно пористої. Новий тип Растеризувати циліндрів це керамічні циліндри, гравірування лазером. Уже зараз такий циліндр в сукупності з камерним ракельним пристроєм є, як вже говорили в розділі «барвисті апарати», найбільш сучасним краскопітающім пристроєм.
В даний час часто - особливо в швидкохідних машинах і машинах великої ширини - застосовують формні циліндри, виготовлені зі сталевої труби. В окремих випадках, при великій довжині зображення, застосовують алюмінієві формні циліндри. У друкарнях, що випускають пакувальну продукцію, і на шпалерних фабриках зазвичай застосовують насадні формні циліндри.
Формні циліндри забезпечуються поздовжніми і поперечними ризиками, щоб спростити розміщення фрагментарних друкованих форм при їх наклейці.
Все формні циліндри повинні встановлюватися таким чином, щоб їх можна було б швидко і легко замінити. Таким чином, і простої машини при зміні тиражу зведені до мінімуму. Тому дуже важливо мати прості в обслуговуванні підшипникові замки. В основному сучасні флексографские друкарські машини оснащуються підйомниками, щоб полегшити обслуговуючому персоналу зміну формних циліндрів.
Діаметр формового циліндра визначають виходячи з необхідного формату, тобто довжини відбитка, з урахуванням товщини форми і клейкої стрічки. Значення цих товщин можуть бути дуже різними, тому виробникам формних циліндрів дуже важливо знати всі ці розміри. При покупці машини слід точно задати «ціну поділки», щоб знати, з яким кроком можна змінювати довжину відбитка і як розраховувати зубчасті колеса для приводу формового циліндра і всієї машини.
Новинкою є застосування гільз, зокрема, тонких гільз з нікелю або синтетичного матеріалу, які за допомогою стиснутого повітря роздуваються і надягають або натягуються на базовий формовий циліндр, який може бути строго циліндричним або мати невелику конусність.
Близько 90% всіх нових машин, що випускаються зараз для флексографії, призначені для роботи із застосуванням гільз.
Побудова друкованого циліндра в секційних машинах. В даний час він зазвичай виготовляється з труби. Циліндр повинен бути розрахований на певне навантаження, щоб не відбувалося деформацій, при яких неможлива рівномірна друк по всій ширині матеріалу.
У сучасних машинах биття друкованого циліндра становлять близько 0,01 мм, а сам він встановлюється на підшипниках кочення. Поверхня циліндра обробляється тонким шліфуванням і тільки в рідкісних випадках хромується і піддається додатковій обробці. У швидкохідних машинах друкований циліндр може охолоджуватися зсередини водою, щоб підтримувати температуру запечатується і фарби на постійному невисокому рівні.
Загальний друкований циліндр в планетарних машинах робиться зі сталі або спеціального чавуну. У найбільш досконалих моделях машин биття його циліндричної поверхні близько 0,005 мм. Опори у циліндрів найменших розмірів, до 1500 мм діаметром, робляться на високоточних кулькових підшипниках, у великих і важких циліндрів - на роликових підшипниках. Застосовують циліндри з одинарної або подвійної стінкою. В обох випадках охолодженням водою підтримується постійна температура на поверхні циліндра, так як під дією подається для сушіння відбитків теплого повітря можуть виникнути деформації поверхні, що призведе до нерівномірності друку і несуміщення фарб на відбитку, а це, нагадаємо, сильні сторони машин цієї конструкції.