Аміачна селітра огляд технологій
У промисловості широко застосовується тільки метод отримання аміачної селітри з синтетичного аміаку і розведеної азотної кислоти. Метод отримання аміачної селітри з аміаку коксового газу і розведеної азотної кислоти перестали застосовувати як економічно невигідний.
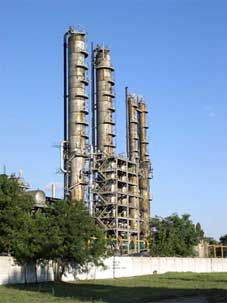
На сучасних заводах, які виробляють практично не злежуються аміачну селітру, гарячі гранули, які містять 0,4% вологи і менш, охолоджуються в апаратах з киплячим шаром. Охолоджені гранули надходять на упаковку в поліетиленові або тришарові паперові бітумірованние мішки. Для додання гранулам більшої міцності, що забезпечує можливість безтарних перевезень, і збереження стабільності кристалічної модифікації при більш тривалому терміні зберігання в аміачну селітру вносять такі добавки, як магнезит, напівводяний сульфат кальцію, продукти розкладанні сульфатного сировини азотною кислотою та інші (зазвичай не більше 0,5 % по масі).
При раціональному використанні тепла, що виділяється нейтралізації можна отримати за рахунок випаровування води концентровані розчини і навіть плав аміачної селітри. Відповідно до цього розрізняють схеми з отриманням розчину аміачної селітри з подальшим випаровуванням його (багатостадійний процес) і з отриманням плаву (одностадійний або безупарочний процес).
Можливі такі принципово різні схеми отримання аміачної селітри з використанням тепла нейтралізації:
- установки, що працюють при атмосферному тиску (надлишковий тиск сокового пара 0,15-0,2 ат);
- установки з вакуум-випарником;
- установки, що працюють під тиском, з одноразовим використанням тепла сокового пара;
- установки, що працюють під тиском, з дворазовим використанням тепла сокового пара (отримання концентрованого плаву).
У промисловій практиці знайшли широке застосування як найбільш ефективні установки, що працюють при атмосферному тиску, з використанням тепла нейтралізації і частково установки з вакуум-випарником.
Отримання аміачної селітри за цим методом складається з наступних основних стадій:
1. отримання розчину аміачної селітри нейтралізацією азотної кислоти аміаком;
2. випарювання розчину аміачної селітри до стану плаву;
3. кристалізація солі з плаву;
4. сушка і охолоджування солі;
5. упаковка.
Процес нейтралізації здійснюють в нейтралізаторі, що дозволяє використовувати тепло реакції для часткового випарювання розчину - ИТН. Він призначений для отримання розчину аміачної селітри шляхом нейтралізації 58 - 60% азотної кислоти газоподібним аміаком з використанням тепла реакції для часткового випаровування води з розчину під атмосферним тиском по реакції:
Безпека процесу нейтралізації забезпечується автоматичними блокуваннями, які припиняють подачу сировини в апарати ІТН при порушеннях співвідношення витрат азотної кислоти і газоподібного аміаку або при зростанні температури в реакційній зоні вище 180 0С; в останньому випадку в ІТН автоматично подається конденсат водяної пари.
Підігрівач азотної кислоти призначений для підігріву 58 - 60% азотної кислоти від температури, при якій він зберігається на складі, до температури 80 - 90 0С за рахунок тепла сокового пара з апарату ІТН. одогреватель газоподібного аміаку призначений для нагріву аміаку до 120 - 180 С. Донейтралізатор призначений для донейтралізаціі аміаком надлишкової кислотності розчину аміачної селітри, безперервно надходить з апарату ІТН, і вводяться в якості добавки сірчаної та фосфорної кислот. Висококонцентрований плав отримують в випарної апараті в один щабель під атмосферним тиском. Промивний і насосні установки необхідно для відмивання пилу аміачної селітри, що буря повітрям з вежі, аерозольних часток аміачної селітри з паро-повітряної суміші випарного апарату, повітря з веж, сокового пара з апаратів ІТН, а також аміаку з цих потоків.
Грануляційна вежа вона складається з трьох частин: верхня частина - зі стелею і перехідником до промивних скруберів; середня частина - власне корпус; нижня частина - з прийомним конусом. Продукт вивантажується на реверсивний конвеєр через прямокутну щілину в нижньому корпусі. Апарат для охолодження гранул в киплячому шарі призначений для охолодження гранул виходять з грануляційної вежі від 110 - 120 до 40 - 45 0 С.
Під псевдозріджених розуміється процес переходу шару зернистого матеріалу в «текуче» стан під дією потоку ожіжающего агента - повітря. Якщо під шар гранул з певною швидкістю подавати повітря, гранули починають інтенсивно переміщатися відносно один одного і шар їх набагато збільшується в об'ємі. Після досягнення певної швидкості найбільш дрібні гранули починають залишати межі шару і несуться потоком повітря. Таке явище відбувається, якщо тиск потоку повітря перевищує силу тяжіння гранул. Опір шару матеріалів майже не залежить від швидкості газу і дорівнює вазі матеріалу, що припадає на одиницю площі. Киплячий шар гранул набуває властивості, притаманні крапельної рідини. Температура всього обсягу киплячого шару гранул, як і будь-який киплячій рідини, практично однакова.
Сучасні великотоннажні агрегати хімічних виробництв мають ряд специфічних особливостей, які слід враховувати при розробці систем автоматизації таких об'єктів:
- послідовна технологічна структура з жорсткими зв'язками між окремими стадіями процесу при відсутності проміжних ємностей;
- велика продуктивність окремих апаратів, розрахована на повну
потужність агрегату;
- територіальне розосередження робочих місць апаратників.
Велика потужність і послідовна структура агрегату задають підвищені вимоги до надійності контролю, регулювання та захисту, так як вихід з ладу окремого елемента часто призводить до повної зупинки агрегату і, як наслідок, до великих економічних втрат.
Детальніше з поточною ситуацією і прогнозом розвитку українського ринку мінеральних добрив можна познайомитися в звіті Академії кон'юнктури Промислових Ринків «Ринок мінеральних добрив вУкаіни».